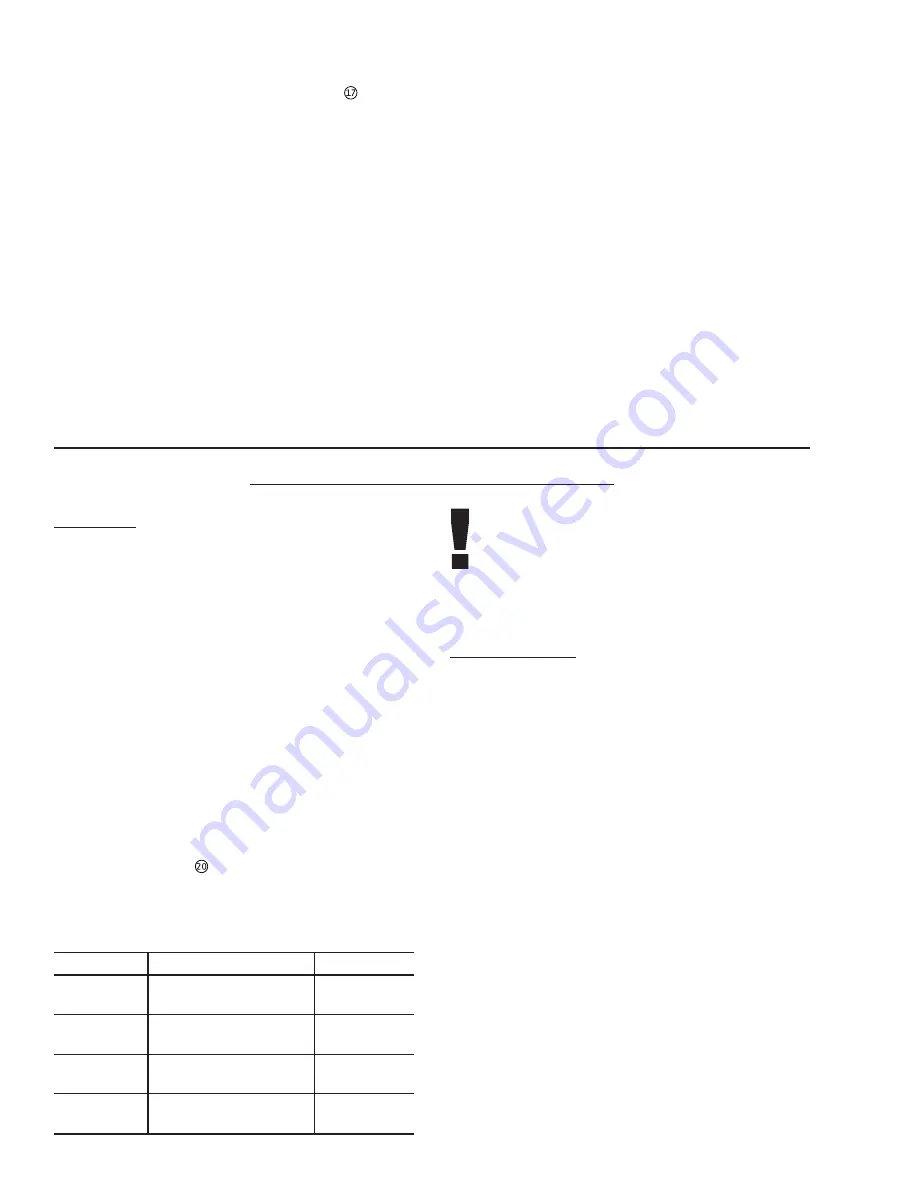
16
FORM CIM 0203
FILTERS
Do NOT
run unit without filters.
Throw-away filters are supplied with units of 2 Ton
and over, and are an Underwriters Laboratories
Class 2 pleated extended surface type. Filters should
be checked monthly for dirt accumulation and
changed when necessary. Replacement filters must
be the same type as originally supplied. Units un-
der 2 Ton are supplied with permanent filters. They
should be checked monthly for dirt accumulation
and cleaned when necessary.
Field access is attained by removing the cover lo-
cated on the side of the left front corner of the evapo-
rator section (Item , Figure 6, page 6). In some
situations, an external filter box will be incorpo-
rated or included in the mixing box.
NOTE: Unit must be shut off at the discon-
nect switch before the filters are serviced. Be
sure to check that the air flow direction arrows
on the filters point in the right direction.
CLEANING THE WATER-COOLED
CONDENSER
Cleaning a water cooled condenser helps to improve
the heat transfer rate, reduce operational cost, re-
store efficiency, prolong heat exchanger life, and
reduce pressure drop pumping cost. Deposits from
water or water treatments, such as scale, lime, rust,
or mud are removed.
Each installation is unique. Therefore, the fluid
quality and operating conditions will dictate when
the heat exchanger needs to be cleaned.
For future reference, it may be beneficial during
the startup to record the water pressure drop across
as well as the inlet and outlet water temperatures of
the water condenser. After a period of time these
values can be checked to see how much loss of op-
erating performance has occurred. If a 10% or
greater change has occurred it would be beneficial
to clean the heat exchanger.
A 5% solution of Phosporic Acid or Oxalic Acid
6); one for the condensing section (Item , Figure
6, page 6). All units require evaporator section drains
to be installed. Heat pumps and water cooled con-
densing units also always require the installation of
a condensing section drain. Units with air cooled con-
densers need a condensing section drain when units
are installed in areas which may permit rain to enter.
It is
EXTREMELY IMPORTANT
that the lines
attached to these connections contain a
trap
, to en-
sure positive draining. It is highly recommended that
the trap be primed with water prior to start-up.
The drain lines
must
be trapped because the coils
are located on the negative sides of the blowers.
The purpose of the condensate trap is to neutralize
the negative pressure created within the cabinet by
the blower.
This negative pressure can vary from less than 1"
up to 2" column. The condensate trap must be of
sufficient depth in water column to permit the con-
densate to flow from the drain pan (See Figure 17).
The “A” dimension must equal or exceed the nega-
tive static pressure developed by the supply air
blower. If it does not, the condensate will not drain
properly and may overflow the drain pan. The trap
must be at least 2-1/2" deep to maintain a water
seal under all operating conditions, especially dur-
ing blower start-up. When evaporator section was
installed, it should have been tilted 0.375" to 0.5"
down on the condensate drain side. Check to be
sure this was done. See Figure 10.
MAINTENANCE PROCEDURES
UNIT
FILTER SIZE/TYPE
QUANTITY
1 to 1-1/2
17-1/2 x 13-1/2 x 1
1
Ton
Permanent
2 to 5 Ton,
20 x 24 x 2
1
Single
Throw-Away
4 to 8 Ton
16 x 24 x2
2
Dual
Throw-Away
10 to 15 Ton
20 x 25 x 2
2
Triple
Throw-Away
Figure 18:
Filter Sizes And Types
Summary of Contents for 4CA1901
Page 2: ...2 FORM CIM 0203 ...