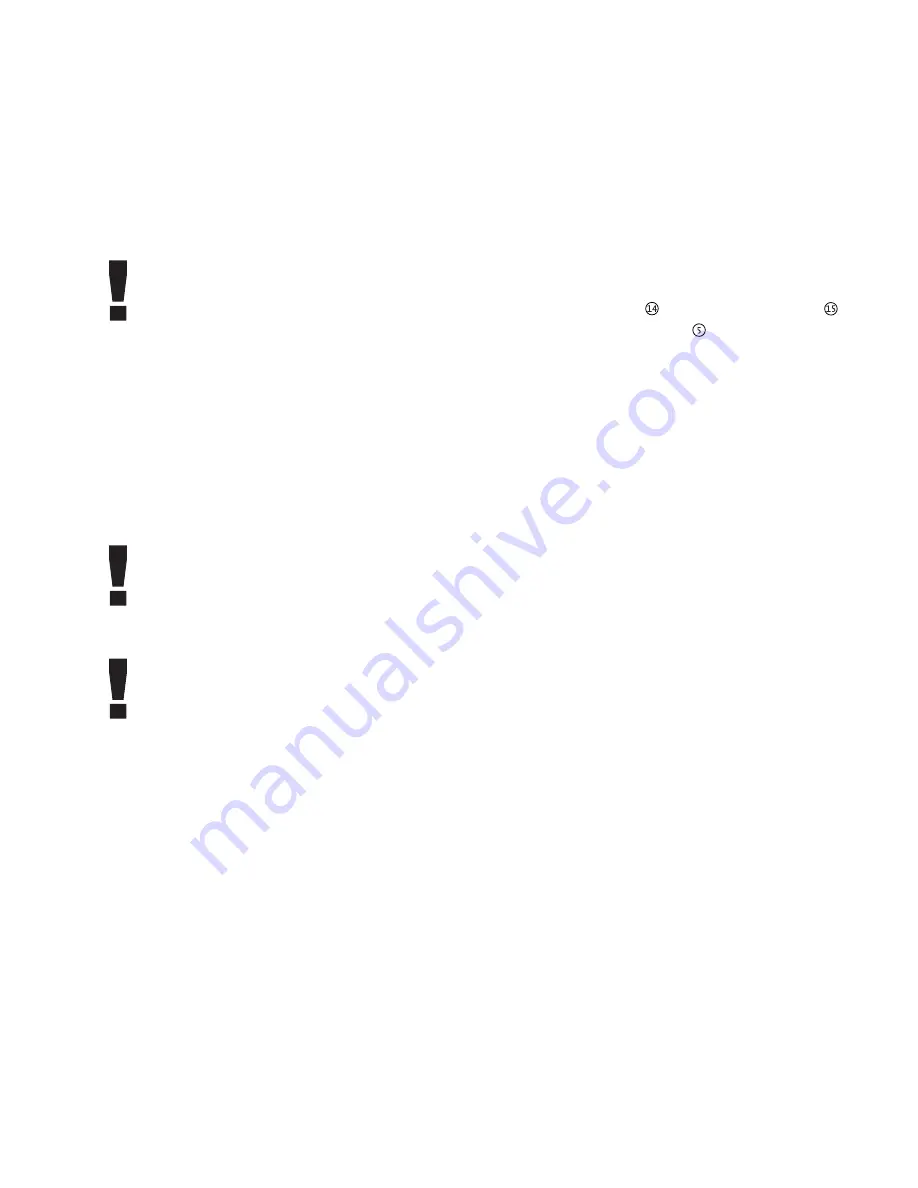
13
FORM CIM 0203
ing the necessary refrigerant, R-22 (See Step
7, page 13). A maximum length of 150 feet of
interconnecting tubing is permitted if a liq-
uid line receiver tank is installed close to the
condenser unit (assumes condenser/condens-
ing section above evaporator). If longer runs
are desired, consult factory for optional com-
ponents.
IMPORTANT! On units with more than
one refrigerant circuit, be careful not to in-
termix lines of the various circuits. If the
connections were labeled before disconnect-
ing the couplings, this should not be a prob-
lem. The 4 Ton Dual, 5 Ton Dual, 6 Ton, 8
Ton and 10 Ton units have 2 circuits (with
2 suction line couplings and 2 liquid line
couplings). The 12 Ton and 15 Ton units
have 3 circuits (with 3 suction line couplings
and 3 liquid line couplings). Half couplings
may be removed to make brazing to the in-
terconnecting tubing more convenient.
CAUTION: When brazing tubing to the
self-sealing couplings, be sure to use a wet
rag, running water bath or chill blocks on
the quick-connects to prevent overheating
the valves and damaging the seals.
NOTE: The interconnect tubing kit (Figure
14) contains a sufficient number of Schrader
access valves to permit you to install one in
each end of both the liquid and suction lines
of the field-supplied tubing. Each intercon-
necting line (suction, liquid, hot gas) must
have one of the supplied Schrader access
fittings installed into the field supplied tub-
ing. However, for short lengths of tubing,
only one Schrader in each line is necessary.
4.
Install the Schrader valve fittings into the tub-
ing before brazing the couplings onto the ends
of the tubing. Use a 1/4" hole to mount the
valve. Clean and debur the tubing before do-
ing any brazing to ensure that no chips or de-
bris are left in the refrigerant circuit. Remove
the Schrader valve cap and core before doing
any brazing.
5. After brazing the tubing to the self-sealing
coupling halves, evacuate each line to 500
microns. Check to make sure that each line
holds a vacuum after removal of the vacuum
pump (indicating no leaks). Add the appropri-
ate charge of R-22 Refrigerant using the
Schrader valves. Refasten male halves to outer
back panel of evaporator section with flanges
and screws (if they were removed for brazing
to tubing). Wipe off coupling seals and
threaded surfaces with a clean cloth to pre-
vent the inclusion of dirt or foreign material
into the system (See Figure 13). Lubricate rub-
ber seal (Item ) and metal seal (Item ) in
the male halves (Item ) with refrigeration oil.
Thread coupling halves together by hand to
insure proper mating of threads. Continue to
hand-thread each half-coupling to its mating
half until resistance is felt (approximately 1-
1/2 to 1-3/4 turns). Complete the connection
of the mating half-couplings with a wrench.
The suction line couplings (size-12) will be
totally engaged after an additional 5-1/2 to 5-
3/4 turns. The liquid line couplings (size-8)
will be totally engaged after an additional 4-
1/2 to 4-3/4 turns.
6.
Refrigerant piping shall be insulated in accor-
dance with local codes and / or applicable
ASHRAE Standards. Insulation exposed to
weather shall be suitable for outdoor use. Pro-
vide protection from water and shielding from
solar radiation as necessary.
7. Add R-22 refrigerant to the system to com-
pensate for the additional interconnecting tub-
ing as follows:
a. For 3/8" liquid line – add 0.6 oz. per foot
b. For 1/2" liquid line – add 1.2 oz. per foot
c. For 5/8" liquid line – add 1.8 oz. per foot
The suction line should be pitched downward
to the compressor, sloping approximately 1/4"
every ten feet to facilitate oil return.
“P” traps (field supplied) are required for all
suction line risers every 15 feet. When the
evaporator is above the condensing section,
an inverted “P” trap should be incorporated
as close as possible to the evaporator (this
minimizes floodback/oil slugging during the
off cycle). If the condensing section is more
than 20 feet above the evaporator, consult the
factory for specific refrigeration components.
Summary of Contents for 4CA1901
Page 2: ...2 FORM CIM 0203 ...