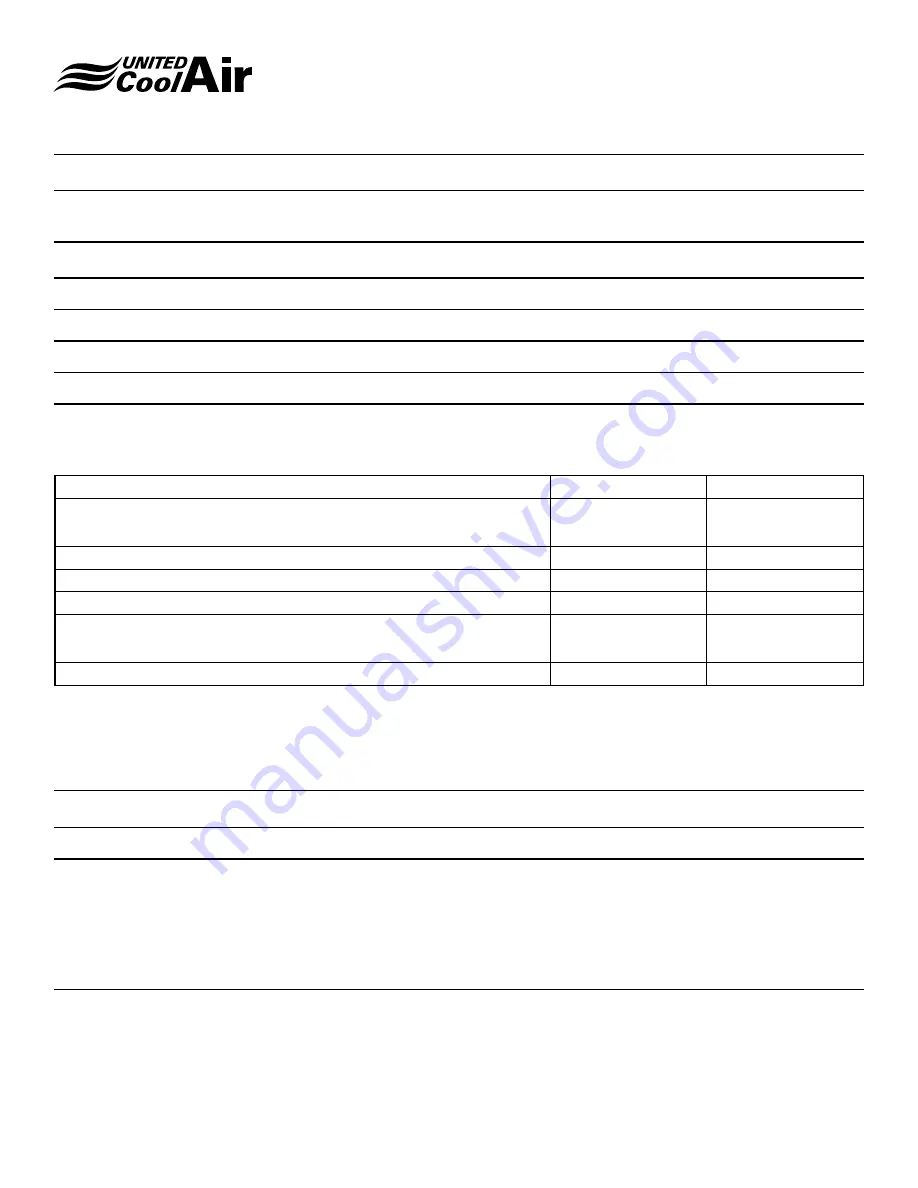
Installation, Operation and Maintenance Manual
C13-Series
43
Subject to change without notice.
10.20-IM (0818)
Verify that unit piping and heat exchangers will not be
subject to freezing conditions� ������������������������������������������������������������������������������Yes ___________ No ___________
No cooling fluid leaks�����������������������������������������������Circuit 1 ___________ Circuit 2 _________________
Cooling Fluid Type
If Glycol what percentage of mix:� ______________________ Good to a temperature of ______________________
Water / Fluid flow rate ���������������������������������������������������GPM __________________
Entering Water Temperature (EFT): °F ___________ Leaving Water Temperature (LFT): °F _________
Water / Fluid Pressure Drop across unit: ������������������������ PSI _________
Verify that all valves on each circuit are functioning properly� ������������������������������Yes ___________ No ___________
Verify water/fluid discharge pressure set point. ����������������������������������������������������Yes ___________ No ___________
Cooling Mode
_________________________________________________________________________________________________
System Air Temperatures �������������������������������������Return: °F _________ Supply: °F _________________
Compressor 1
Compressor 2
Suction Pressure:
Suction Line Temperature:
psi _______
°F ________
psi _______
°F ________
Saturation Temperature:
°F ________
°F ________
Suction Superheat:
° ________
° ________
Liquid Line Pressure:
psi _______
psi _______
Saturation Temperature:
Liquid Line Temperature:
°F ________
°F ________
°F ________
°F ________
Sub-cooling:
° ________
° ________
Electrical
Evap� Motor Amps ������������������������������������������������������������ L1 ____________ L2 ___________ L3 ____________
Compressor 1 Amps ��������������������������������������������������������� L1 ____________ L2 ___________ L3 ____________
Compressor 2 Amps ��������������������������������������������������������� L1 ____________ L2 ___________ L3 ____________
Heating Mode (Optional)
System Air Temperatures �������������������������������������Return: °F _________ Supply: °F _________________
Entering Water Temperature:������������������������������� Return: °F ________ Steam Pressure: psi __________
Leaving Water Temperature: ��������������������������������Return: °F _________
Electric kW: _________ Voltage: ___________
Amps: Stage1 ���������������������������������� L1 _____________ L2 ___________ L3 ____________
Stage2 ���������������������������������� L1 _____________ L2 ___________ L3 ____________
Misc� ____________________________________________________________________________________________
_________________________________________________________________________________________________
Technician (print name): _____________________________________________________________________________
Company: ________________________________________________________________________________________
Phone: __________________________________________________________ Fax: ____________________________
Signature: ______________________________________________________ Date: ____________________________
Summary of Contents for C13-Series
Page 2: ......