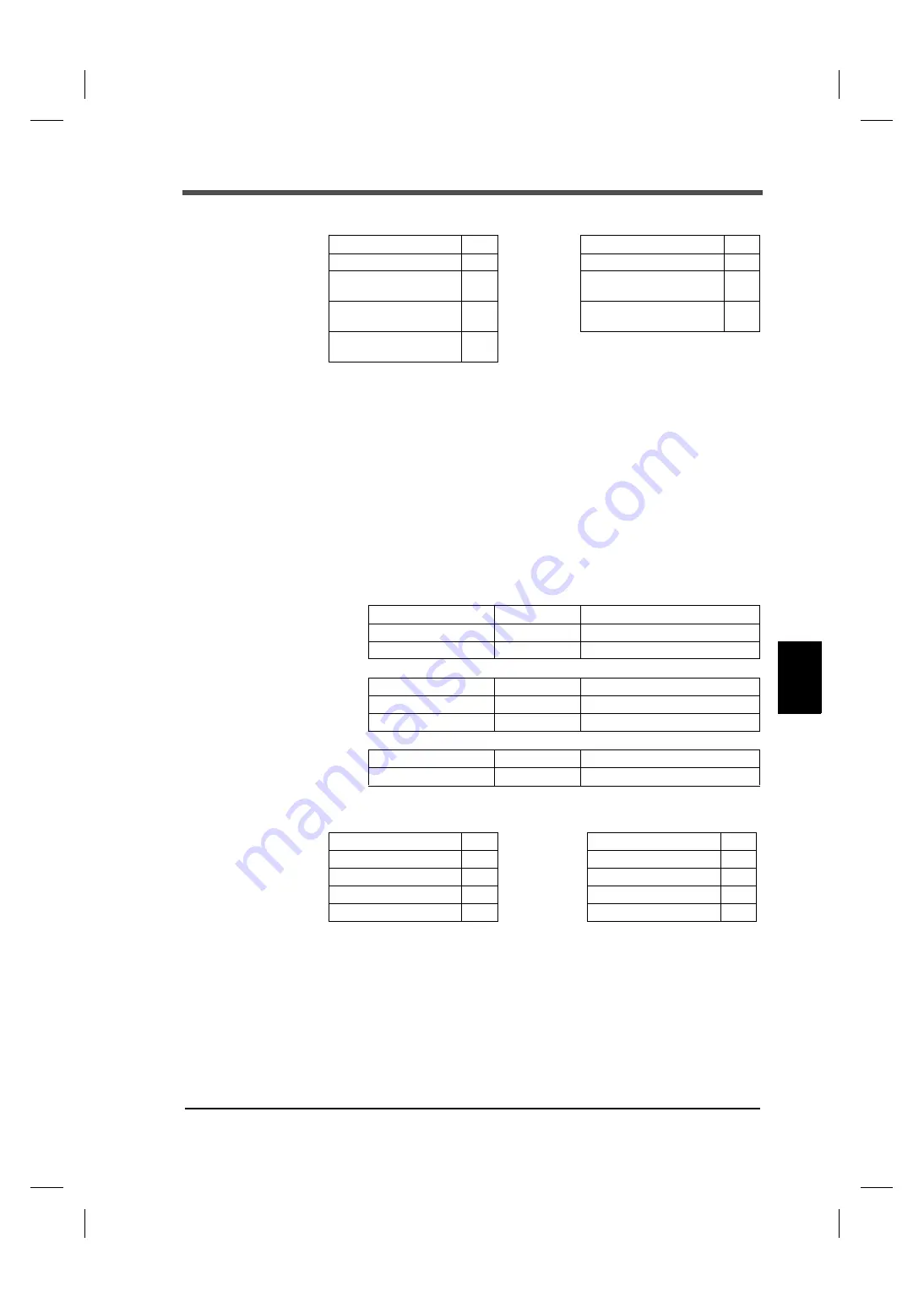
43
7
OPTION
43
OP
TION
Chapter
7
Example) Read the contents of linked with indicated value (address 30004).
Keep in mind that the relative address for reading the linked with indicated value is 0x03.
The example shows the case where the indicated value of the F331 is as follows:
05 (0x05) Write single coil
A slave coil is changed to ON or OFF.
If broadcast (0) is specified, all slave coils of the same address are rewritten.
To request, specify the coil address and output value.
0xFF and 0x00 correspond to ON, and 0x00 and 0x00 correspond to OFF.
No change is made with other data, which are considered as improper data.
Example) Turn on the hold/judge ON (address 00001).
Keep in mind that the relative address for writing in the hold/judge ON is 0x00.
In the case of normal writing, the response becomes identical to the request.
* To confirm coil execution, judge as complete with a normal response.
[Request]
Function
04
[Response]
Function
04
Start address; higher
00
Number of data bytes
02
Start address; lower
03
Linked with indicated value
(higher)
03
Number of registers;
higher
00
Linked with indicated value
(lower)
E8
Number of registers;
lower
01
Linked with indicated value: 1000 (0x03E8)
[Request]
Function
1
byte
0x05
Start address
2
byte
s
0x0000 - 0xFFFF
Output data
2
byte
s
0x0000 or 0xFF00
[Response]
Function
1
byte
0x05
Start address
2
bytes
0x0000 - 0xFFFF
Output data
2
byte
s
0x0000 or 0xFF00
[Error response]
Error code
1
byte
0x85 (fu 0x80)
Exception code
1
byte
01 or 02 or 03
[Request]
Function
05
[Response]
Function
05
Start address; higher
00
Start address; higher
00
Start address; lower
00
Start address; lower
00
Hold/judge ON; higher
FF
Hold/judge ON; higher
FF
Hold/judge ON; lower
00
Hold/judge ON; lower
00
Summary of Contents for F331
Page 1: ...OPERATION MANUAL 26MAY2014REV 1 02 DIGITAL INDICATOR F331 ...
Page 79: ...70 8 SPECIFICATIONS 70 SPECIFICATIONS Chapter 8 8 2 Dimensions Unit mm ...
Page 82: ...73 8 SPECIFICATIONS 73 SPECIFICATIONS Chapter 8 When the RS 485 option is equipped Unit mm ...
Page 83: ...74 8 SPECIFICATIONS 74 SPECIFICATIONS Chapter 8 When the RS 232C option is equipped Unit mm ...