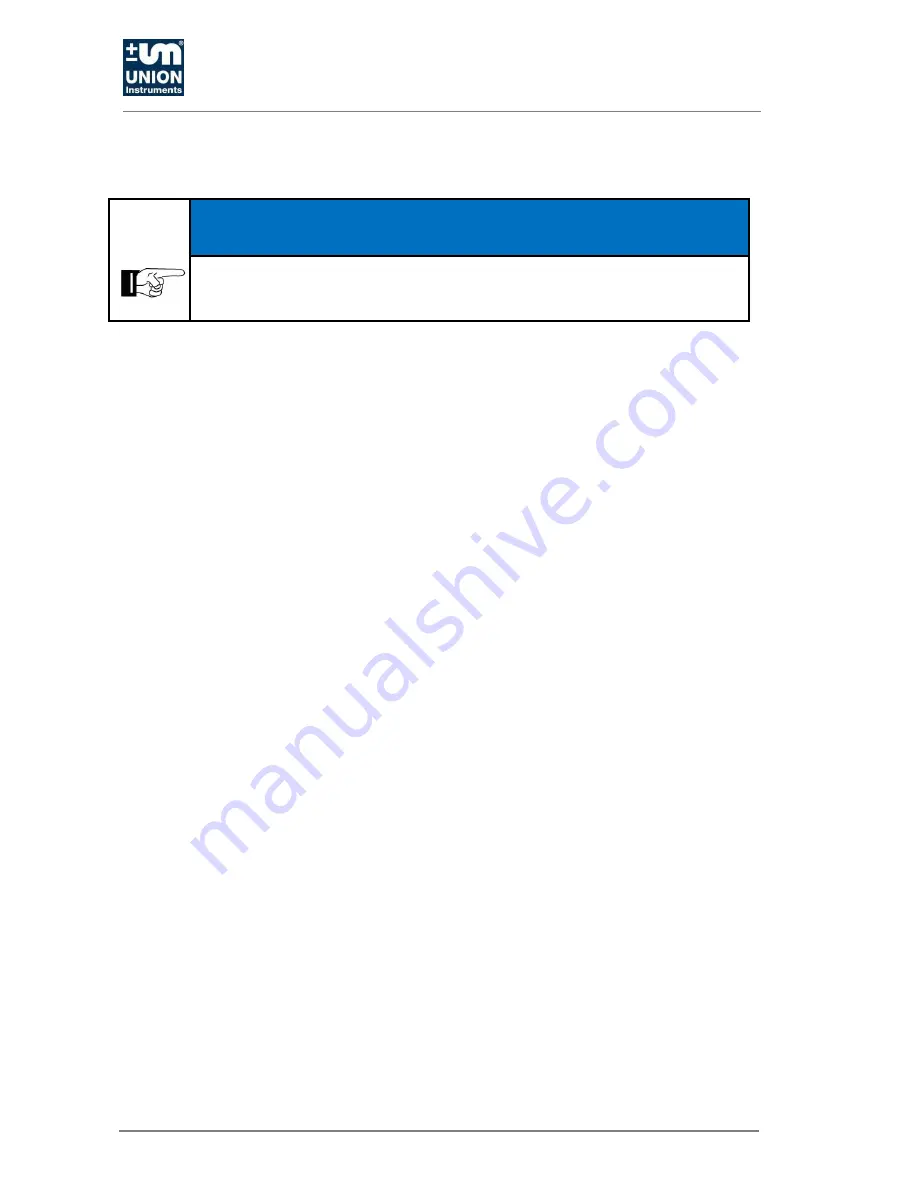
14
Safety information
3.6 Performing a workplace hazard analysis
NOTE
Depending on the National regulations and, if necessary, regardless of the CE
marking of the gas cooler, the owner must prepare a workplace hazard analysis!
Changes to these operating instructions may occur in the future due to further
technical developments. If you desire additional information or if specific problems
arise that are not covered in detail in this manual, you will receive information by
contacting the following address or local representative:
Union Instruments GmbH
Zeppelinstrasse 42
76185 Karlsruhe
Germany
+49 (0)721-680381-0
+49 (0)721-680381-33
http://www.union-instruments.com
Summary of Contents for Pury250 S
Page 1: ...Operating Instructions Gas Cooler Pury250 S ...
Page 5: ...1 Technical data 1 1 Dimensions Weight approx 12 6 kg 28lbs 5 ...
Page 10: ...10 EC Declaration of Conformity ...
Page 15: ...15 4 Protective equipment 4 1 Enclosure cover Fig 4 1 Enclosure cover ...
Page 32: ...32 Transport installation and acceptance ...
Page 34: ...34 Commissioning Switching on ...
Page 36: ...36 Description of the HMI and operator control elements ...
Page 49: ...49 Maintenance ...
Page 53: ...53 ...
Page 54: ...54 ...
Page 58: ...58 Service ...
Page 59: ...59 14 Related documents Declaration of Conformity Service documentation optional ...
Page 60: ...60 Related documents ...
Page 62: ...62 Disposal ...
Page 64: ...64 Spare parts ...