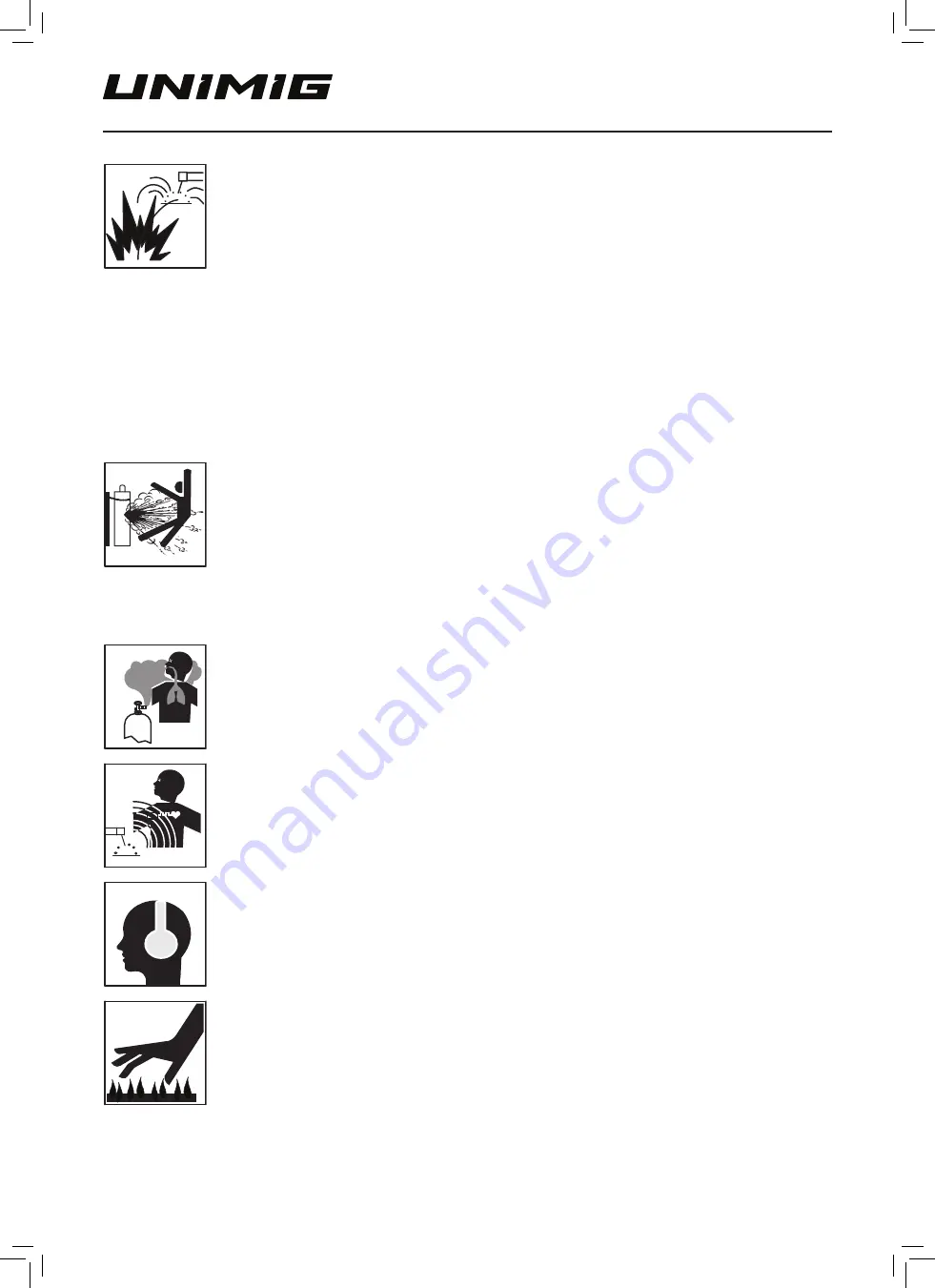
4
RAZOR COMPACT 250
OPERATING MANUAL
Fire hazard
• Welding/cutting on closed containers, such as tanks, drums, or pipes, can cause them to explode. Flying sparks from the
welding/cutting arc, hot workpiece, and hot equipment can cause fires and burns. Accidental contact of the electrode
to metal objects can cause sparks, explosion, overheating, or fire. Check and be sure the area is safe before doing any
welding/cutting.
• The welding/cutting sparks & spatter may cause fire, therefore remove any flammable materials well away from the working
area. Cover flammable materials and containers with approved covers if unable to be moved from the welding/cutting area.
• Do not weld/cut on closed containers such as tanks, drums, or pipes, unless they are correctly prepared according to the
required Safety Standards to ensure that flammable or toxic vapours and substances are totally removed, these can cause
an explosion even though the vessel has been “cleaned”. Vent hollow castings or containers before heating, cutting or
welding. They may explode.
• Do not weld/cut where the atmosphere may contain flammable dust, gas, or liquid vapours (such as petrol)
• Have a fire extinguisher nearby and know how to use it. Be alert that welding/cutting sparks and hot materials from welding/
cutting can easily go through small cracks and openings to adjacent areas. Be aware that welding/cutting on a ceiling, floor,
bulkhead, or partition can cause a fire on the hidden side.
Gas cylinders
• Shielding gas cylinders contain gas under high pressure. If damaged, a cylinder can explode. Because gas cylinders usually
are part of the welding/cutting process, be sure to treat them carefully. CYLINDERS can explode if damaged.
• Protect gas cylinders from excessive heat, mechanical shocks, physical damage, slag, open flames, sparks, and arcs.
• Ensure cylinders are held secure and upright to prevent tipping or falling over.
• Never allow the welding/cutting electrode or earth clamp to touch the gas cylinder, do not drape welding cables over the cylinder.
• Never weld/cut on a pressurised gas cylinder, it will explode and kill you.
• Open the cylinder valve slowly and turn your face away from the cylinder outlet valve and gas regulator.
Gas build-up
• The build-up of gas can cause a toxic environment, deplete the oxygen content in the air resulting in death or injury. Many
gases use in welding/cutting are invisible and odourless.
• Shut off shielding gas supply when not in use.
• Always ventilate confined spaces or use approved air-supplied respirator.
Electronic magnetic fields
• MAGNETIC FIELDS can affect Implanted Medical Devices.
• Wearers of Pacemakers and other Implanted Medical Devices should keep away.
• Implanted Medical Device wearers should consult their doctor and the device manufacturer before going near any electric
welding, cutting or heating operation.
Noise can damage hearing
• Noise from some processes or equipment can damage hearing.
• Wear approved ear protection if noise level is high.
Hot parts
• Items being welded/cut generate and hold high heat and can cause severe burns.
• Do not touch hot parts with bare hands. Allow a cooling period before working on the welding/cutting gun. Use insulated
welding gloves and clothing to handle hot parts and prevent burns.
RAZOR Compact 250 Manual APR23.indd 4
RAZOR Compact 250 Manual APR23.indd 4
6/04/2023 4:02:58 PM
6/04/2023 4:02:58 PM