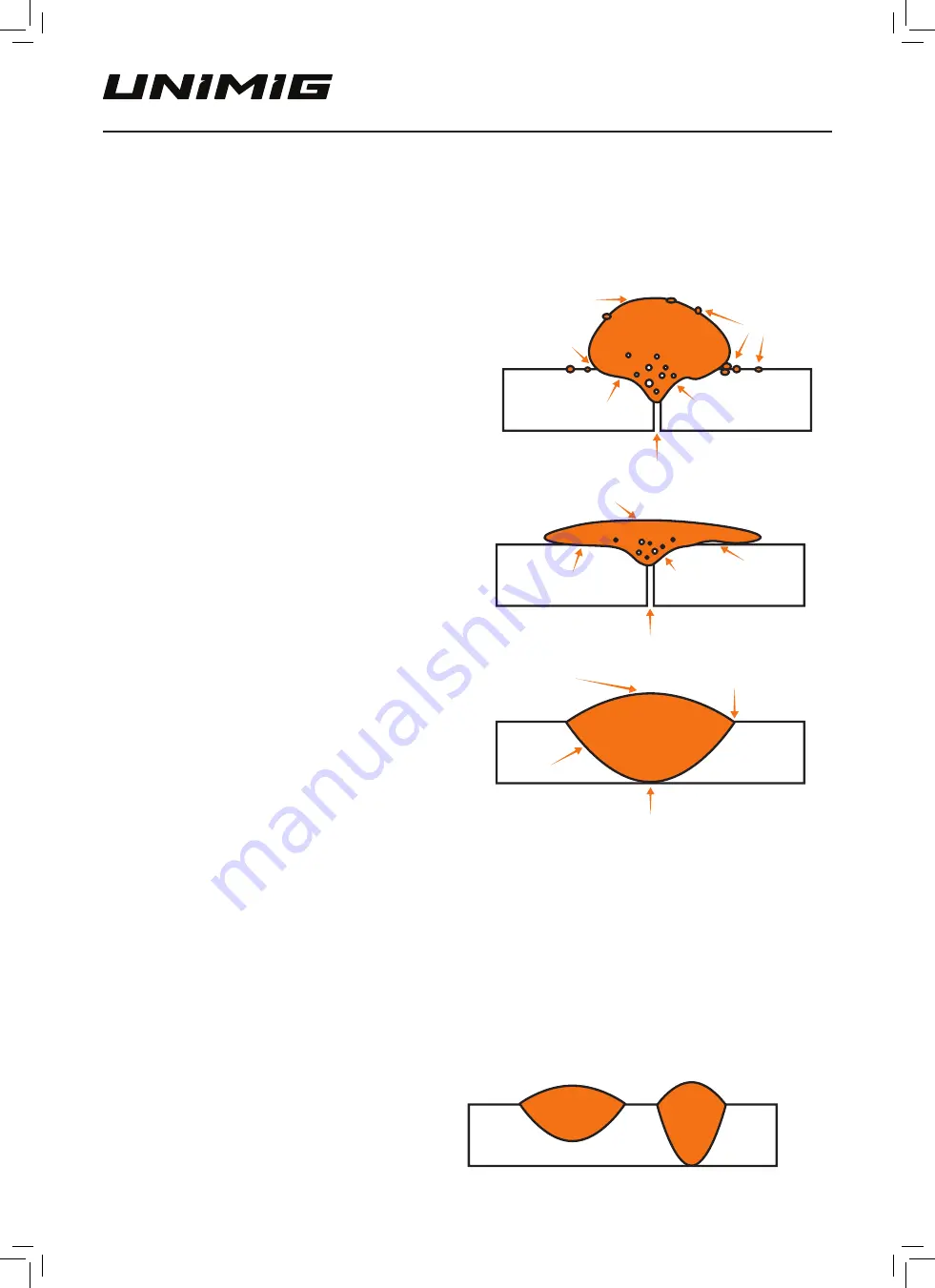
28
RAZOR COMPACT 250
OPERATING MANUAL
Travel Speed
Travel speed is the rate that the gun is moved along the weld joint and is usually measured in mm per minute. Travel
speeds can vary depending on conditions and the welder's skill and is limited to the welder's ability to control the
weld pool. The push technique allows faster travel speeds than the drag technique.
The gas flow must also correspond with the travel speed, increasing with faster travel speed and decreasing at a
slower speed. Travel speed needs to match the amperage and will decrease as the material thickness and amperage
increase.
Travel Speed Too Fast
Too fast a travel speed produces too little heat per mm of
travel resulting in less penetration and reduced weld fusion.
The weld bead solidifies very quickly, trapping gases inside
the weld metal and causing porosity. Undercutting of the
base metal can also occur, and an unfilled groove in the
base metal is created when the travel speed is too fast to
allow molten metal to flow into the weld crater created by
the arc heat.
Travel Speed Too Slow
Too slow a travel speed produces a large weld with a
lack of penetration and fusion. The energy from the arc
dwells on top of the weld pool rather than penetrating the
base metal. This produces a wider weld bead with more
deposited weld metal per mm than is required, resulting in
a weld deposit of poor quality.
Travel Speed Too Fast
High, narrow bead
Undercut
Lack of fusion
Porosity
Spatter
Lack of joint penetration
Lack of joint penetration
Lack of fusion
Porosity
Cold lap
Large, wide bead
Travel Speed Too Slow
Correct Travel Speed
Good penetration
Good toe fusion
Even shaped bead
Good sidewall fusion
Gas Selection
The purpose of the gas in the MIG process is to shield the wire, the arc and the molten weld metal from the
atmosphere. Most metals when heated to a molten state will react with the air in the atmosphere, without the
protection of the shielding gas the weld produced would contain defects like porosity, lack of fusion and slag
inclusions. Additionally, some of the gas becomes ionised (electrically charged) and helps the current flow smoothly.
• The correct gas flow is critical in protecting the welding zone from the atmosphere.
• Too low a flow will give inadequate coverage and result in weld defects and unstable arc conditions.
• Too high a flow can cause air to be drawn into the gas column and contaminate the weld zone.
Use the correct shielding gas. CO2 is suitable for steel and offers good penetration characteristics; the weld profile
is narrower and slightly more raised than the weld profile obtained from Argon CO2 mixed gas. Argon CO2 mix gas
offers better weldability for thin metals and has a wider range of setting tolerance on the machine. Argon-CO2 5/2 is
a good all-round mix suitable for most applications.
Correct Travel Speed
The correct travel speed keeps the arc at the leading edge
of the weld pool, allowing the base metal to melt sufficiently
to create good penetration, fusion and wetting out of the
weld pool producing a weld deposit of good quality.
Argon-CO₂
CO₂
RAZOR Compact 250 Manual APR23.indd 28
RAZOR Compact 250 Manual APR23.indd 28
6/04/2023 4:03:08 PM
6/04/2023 4:03:08 PM