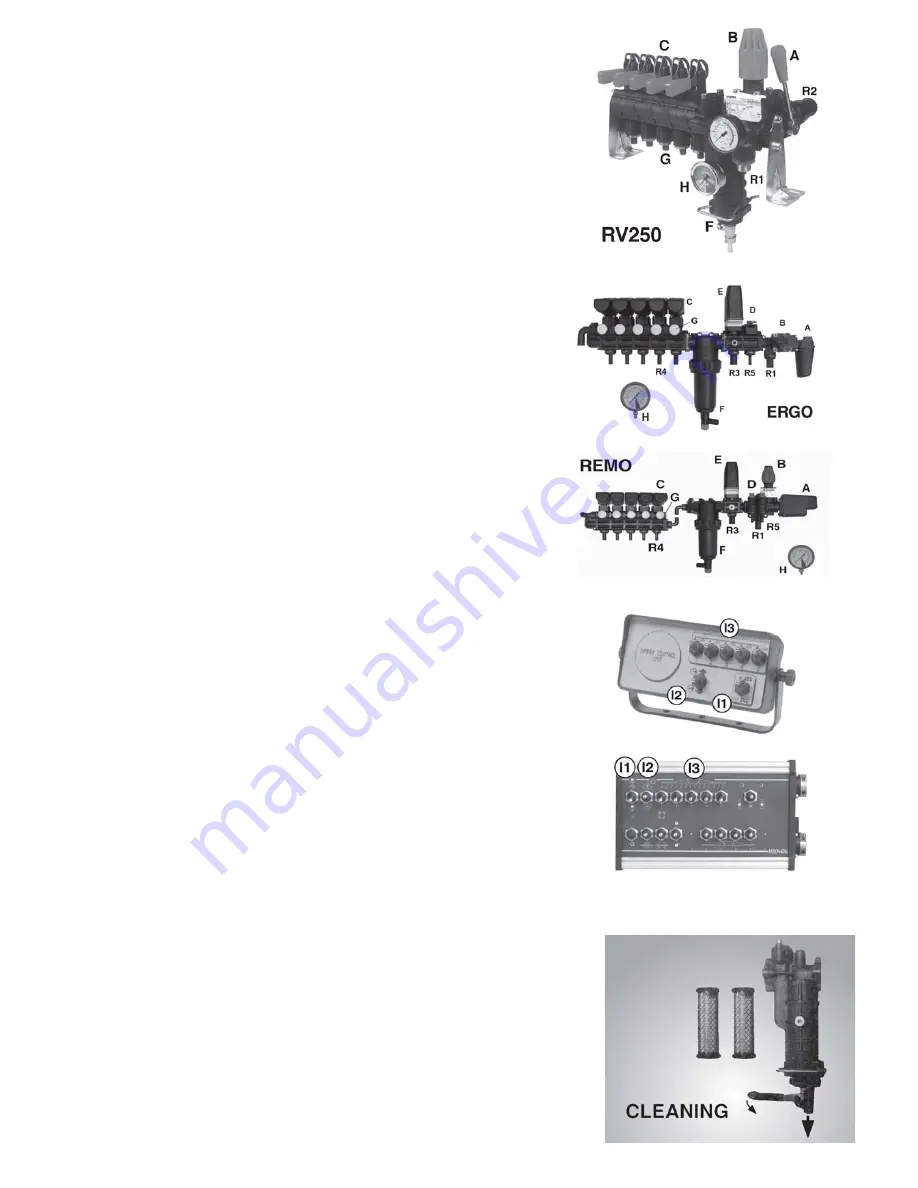
unigreen
15
Pressure regulators with a volumetric valve (RPN-DPR-ERGO-REMO)
Adjusting the maximum pressure valve
= put main control
A
in the drain position (“OFF”).
= loosen the hand wheel of maximum pressure valve
B
completely
(anticlockwise).
= open volumetric valve
E
completely.
= start the pump by activating the power-takeoff of the tractor at 540rpm
= open main control
A
(position “ON”), the manometer will be activated
= open the drain tap on filter
F
slightly (only ERGO and REMO)..
= close volumetric valve
E
completely. If the pressure rises over the
maximum limit of the system, make sure maximum pressure valve
B
is open
(see previous indications)
= open all of the section valves
C
(position “ON”)
= adjust maximum pressure valve
B
to a value over that of the working
pressure (generally 10-14 bar) and in any case lower than the safe maximum
pressure that the system can reach.
Adjusting the volumetric pressure.
= with the volumetric pressure valve
E
adjust the pressure to the value the
treatment will be done at (the pressure is indicated on the nozzles tables on
the basis of the tractor speed and litres/hectare to spray)
Warning! The working pressure must be adjusted with the volumetric
valve and not with the maximum pressure valve. In the case the working
pressure is too near to the calibrated pressure of the maximum pressure
valve, the proportional valve may not be able to compensate the speed
variations correctly.
Adjusting the compensated returns
= close only one tap of section
C
(position “OFF”).
= adjust the corresponding compensator
G
until you return to the pressure set
previously (displayed on the manometer).
= open and close the tap of section
C
and check that the pressure remains
constant.
= repeat the above operations for all the section taps.
If the types of nozzles aren’t changed the regulations carried out will guarantee
a constant spraying of the liquid also per treatments that are done at different
working pressures.
NB: if the type of nozzle is changed then the calibrating will have to be done
again.
4.9
DELIVERY FILTERS (ONLY EQUIPPED MODELS)
Particularly useful when using small (low volume) nozzles.
In a central position with a manometer after the filter that shows any blockages
in the cartridge. On the RVA version there is also a manometer before the car-
tridge to make it easier to find the problem.
The cleaning of the cartridge in the RPV-DPR-ERGO-REMO series is fully au-
tomatic (for ERGO and REMO see the previous paragraph), for the model RVA
you should open the drain with the relevant lever (Fig. N° 6) for 2-3 minutes
during the washing operations, as in the enclosed instructions.
You should clean the cartridge by hand periodically, on the basis of the product
used. To clean, stop the pump. Wear rubber gloves and the other personal pro-
tective equipment when cleaning. Follow the instructions in the enclosed
manual.
4.10 SPRAYING COMPUTER (OPTIONAL)
Scrupulously follow the instructions in the relevant manual when using.
We don’t recommend using the sprayer with the computer until you have had
at least one lesson from the UNIGREEN technicians.
FIG. 6
Summary of Contents for Campo 11
Page 27: ...unigreen 27...