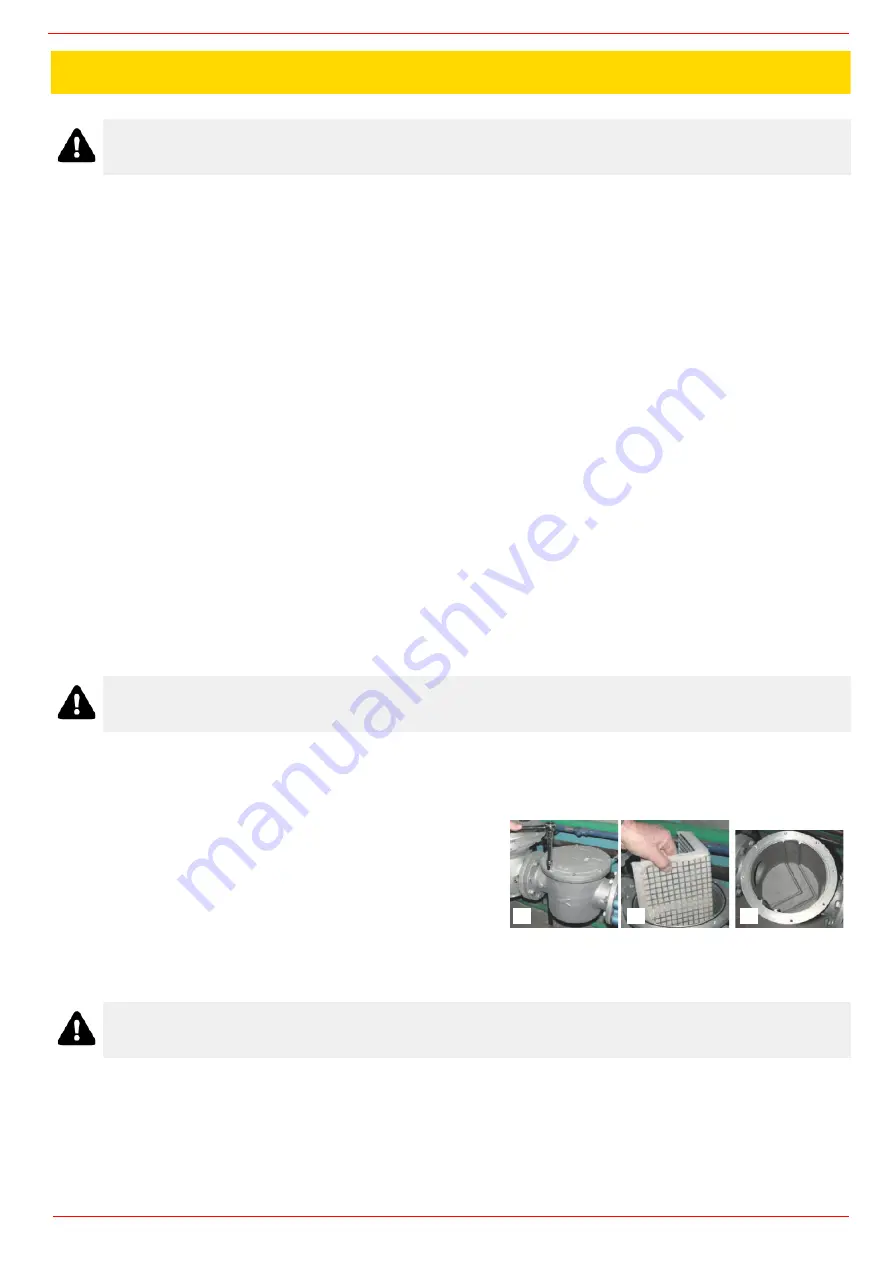
PART IV: MAINTENANCE
41
At least once a year carry out the maintenance operations listed below. In the case of seasonal servicing, it is recommended to carry
out the maintenance at the end of each heating season; in the case of continuous operation the maintenance is carried out every 6
months.
ROUTINE MAINTENANCE
Check that the gas meter is not moving when the burner is off. In case it is rotating, look for possible leaks.
Check the cleaning condition of the vent. Clean the vent by using exclusively a dry brush. If needed, disassemble it from the
motor’s shaft and wash it by using non corrosive detergents. Prior to disassemble the vent, take the measurements in relation to
the motor's shaft, so as to reassemble it in the same position.
Check that all parts in contact with combustive air (air box, protection mesh and Archimedean screw) are clean and free from any
obstruction that might impede free afflux. Clean it with compressed air if available and/or a dry brush or cloths. Eventually wash it
with non corrosive detergents.
Check the blast tube; it must be substituted in case of obvious cracks or anomalous holes. Slight deformations that do not affect
combustion may be tolerated
Check the condition of the burner-boiler gasket. Eventually substitute it.
Check the fan’s motor: no specific maintenance is needed. In case of anomalous noises when running, check the condition of the
bearings and eventually substitute them or completely substitute the motor.
Clean and examine the gas filter cartridge and replace it if necesssary;
Remove and clean the combustion head;
Examine and clean the ignition electrodes, adjust and replace them if necessary;
Examine and clean the detection electrode/photoelement (according to the burner models), replace it if necessary, in case of
doubt, check the detection circuit, after the burner start-up;
Clean and grease leverages and rotating parts.
At least every 2 months, or more often if needed, clean the room where the burner is installed.
Avoid leaving installations, papers, nylon bags, etc., inside the room. They could be sucked by the burner and cause malfunctio-
ning.
Check that the room’s vents are free from obstructions.
Gas filter maintenance
WARNING: ALL OPERATIONS ON THE BURNER MUST BE CARRIED OUT WITH THE MAINS DISCONNECTED
AND THE FUEL MANAUL CUTOFF VALVES CLOSED!
ATTENTION: READ CAREFULLY THE “WARNINGS” CHAPTER AT THE BEGINNIG OF THIS MANUAL.
ATTENTIONwhen servicing, if it was necessary to disassemble the gas train parts, remember to execute the gas
proving test, once the gas train is reassembled, according to the procedure imposed by the law in force.
WARNING: Before opening the filter, close the manual cutoff valve downstream the filter and bleed the gas; check
that inside the filter there is no pressurised gas.
PART IV: MAINTENANCE
C
B
A
To clean or remove the filter, proceed as follows:
1 remove the cap unscrewing the fixing screws (A);
2 remove the filtering cartridge (B), clean it using water and soap, blow it
with compressed air(or replace it, if necessary)
3 replace the cartridge in its proper position taking care to place it
inbetween the guides as not to hamper the cap replacement;
4 be sure to replace the “O” ring into its place (C) and replace the cover
fastening by the proper screws (A).