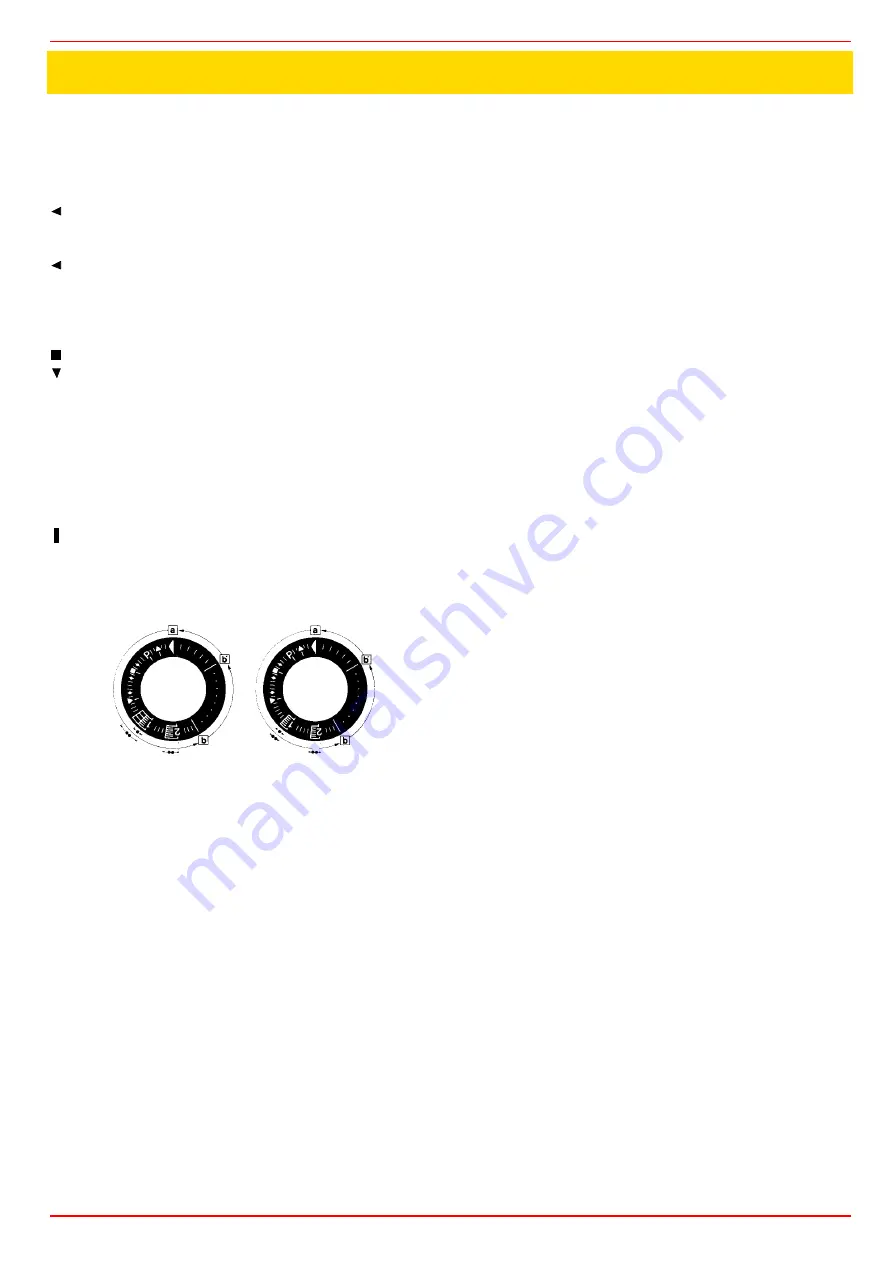
SIEMENS LFL 1.3.. CONTROL BOX
Automatic programme in the event of interruption and indication of posi-
tion when interrupted
By default, in the event of any kind of interruption, the flow of fuel is imme-
diately interrupted. At the same time the programmer stops and this indi-
cates the position at the time of the interruption.
A symbol on the indicator disc shows each time the type of stoppage:
No start-up (for example fault in the CLOSED signal for the
limit contact "Z" at terminal 8 or some other contact between
the terminals 12 and 4 or 4 and 5 is not closed).
Start-up suspended because of a fault in the OPEN signal
for the limit contact "A" at terminal 8.
Block due to absence of air pressure signal. From this
moment onwards any absence of air pressure will cause a
block.
Block due to malfunction of the flame detector circuit.
Start-up interrupted because there is a fault in the MINMUM
signal for the auxiliary contact of the damper servo motor at
terminal 8.
Block due to absence of flame signal at the end of the 1st
safety period.
From this moment onwards any absence of a flame signal will cause a
block.
Blockdue to absence of flame signal at the end of the 2nd
safety period (flame signal of main burner).
Blockdue to absence of flame signal or air pressure during
operation.
Where a block stoppage occurs at any moment between switch on and
pre-ignition without registering any symbol, the cause is normally an
unscheduled flame signal.
a-b
Start-up programme
b-b' For time variants:move the programmer on to the automatic stop
after the burner starts up (b' = position of the programmer during normal
burner operation).
b(b')-aPost-ventilation programme after a regulation stop.At the start-up
position "a" the programmer stops automatically.
.
Safety time duration for mono-tube burners
..
Safety time duration for twin-tube burners
The apparatus can be reset immediately after a block. After resetting (and
after the elimination of any problem causing the stoppage or after a power
failure) the programmer returns to its start-up position. In this event only
the terminals 7, 9, 10 and 11 are live in accordance with the monitoring
programme. Only after this the device programs a new startup.
Operation
The wiring system and also the control system of the programmer "P"
have already been given in this manual. The response signals required
for the active parts and the flame monitor circuit are shown by a hatching.
In the absence of these response signals the mechanism interrupts the
start-up programme; the exact time of the interruption can be identified
from the visual indicator and will cause a block if the safety code requires
it.
A
consent to start-up by means of the thermostat or pressostat "R"
A-B start-up
program
B-C normal burner operation
C
regulation stop caused by "R"
C-D programmer returns to start-up position A.
During the regulation stop only terminals 11 and 12 are live and the dam-
per, through the limit contact "Z" of its servo-motor is in the CLOSED posi-
tion.The flame detector circuit F is activated (terminals 22 and 23 or 23/4)
for the detector test and the paracitic light test.
Where the burners do not have dampers (or have an independent 00
damper control mechanism) there must be a bridge between terminals 6
and 8, otherwise the mechanism will not start up the burner.
For a burner to start up the following conditions must be met:
z
Mechanism not blocked/reset.
z
Damper closed.Limit contact switchZ must be in the CLOSED position
and allow current to flow between terminals 11 and 8.
z
Any contacts checking that the fuel valve (bv...) is closed, or other con-
tacts with similar functions, must be closed between terminal 12 and
the air pressostat LP.
z
The contact for the air pressostat LP must be in the off position (LP
test) so as to feed terminal 4.
z
The gas pressostat contacts GP and the safety thermostat and pres-
sostat contacts W must also be closed.
Start-up program
A Start-up
(R closes the start-up control ring between terminals 4 and 5)
The programmer starts up.At the same time the ventilator motor is fed
through terminal 6 ( only for pre-ventilation) and, after t7, the ventilator
motor or the combustion gas exhaust fan is fed through terminal 7 (pre-
ventilation and post-ventilation).
At the end of t16, the command opening the damper passes through ter-
minal 9; during the damper opening time the programmer does not move
since terminal 8, through which the programmer is fed, is dead.
Only once the damper is fully open and the limit contact switch A has
switched on, feeding terminal 8, does the programme proceed.
t1
Pre-ventilation time with damper fully open (nominal air flow).
Shortly after the beginning of the pre-ventilation time, the air pressostat
should switch off the current between terminals 4 and 13;otherwisethe
apparatus would block (air pressure monitor).
At the same time the terminal 14 should be live since current feeding the
ignition transformer and the fuel valves passes through this circuit.
During pre-ventilation time the flame detector circuit is checked and in the
event of an operational defect the monitor brings about a block.
At the end of the pre-ventilation time the monitor automatically moves the
damper servo-motor, through terminal 10, to the flame ignition position
which is governed by the auxiliary contact "M".
During this period the programmer stops until terminal 8, is again activate-
dthrough contact "M".
After a few seconds the little programmer motor is directly fed by the
active part of the apparatus.
After this point terminal 8 plays no further part in the burner ignition pro-
cess.
Mono-tube burner
t3
Pre-ignition time waiting the response from the fuel valve at termi-
nal 18.
t2
Safety time (start up flame strenght); at the end of the safety time a
flame signal should appear at terminal 22 of the amplifier and it should
stay on until a regulation stop; if this does not happen the mechanism will
block.
t4
Interval; at the end of t4, terminal 19 is live.
t5
Interval At the end of t5 terminal 20 is live.At the same time the
monitor outlets from 9 and 11 and terminal 8 into the active part of the
apparatus are kept galvanically separatedso as to protect the monitor
itself from recovery voltage through the capacity regulator circuit.
Twin-tube burners (**)
t3
Preignition time until the all clear to the pilot burner valve at
terminal 17.
t2
First safety time (pilot flame strenght); at the end of the safety time
a flame signal should appear at terminal 22 of the amplifier and it should
stay on, until a regulation stop; if it does not, the apparatus will block.
t4
Interval until the consent to the fuel valve at terminal 19, for the first
flame of the main burner.
APPENDIX
P
1
2
Summary of Contents for HTP512A
Page 47: ...C I B UNIGAS M039219CA 47 Wiring diagram 21 002 3 ...
Page 48: ...C I B UNIGAS M039219CA 48 ...
Page 49: ...C I B UNIGAS M039219CA 49 ...
Page 50: ...C I B UNIGAS M039219CA 50 WIRING DIAGRAM Cod 11 336 2 ...
Page 51: ...C I B UNIGAS M039219CA 51 ...
Page 52: ...C I B UNIGAS M039219CA 52 ...
Page 53: ...C I B UNIGAS M039219CA 53 WIRING DIAGRAM Cod 11 339 2 ...
Page 54: ...C I B UNIGAS M039219CA 54 ...
Page 55: ...C I B UNIGAS M039219CA 55 ...
Page 56: ...C I B UNIGAS M039219CA 56 ...