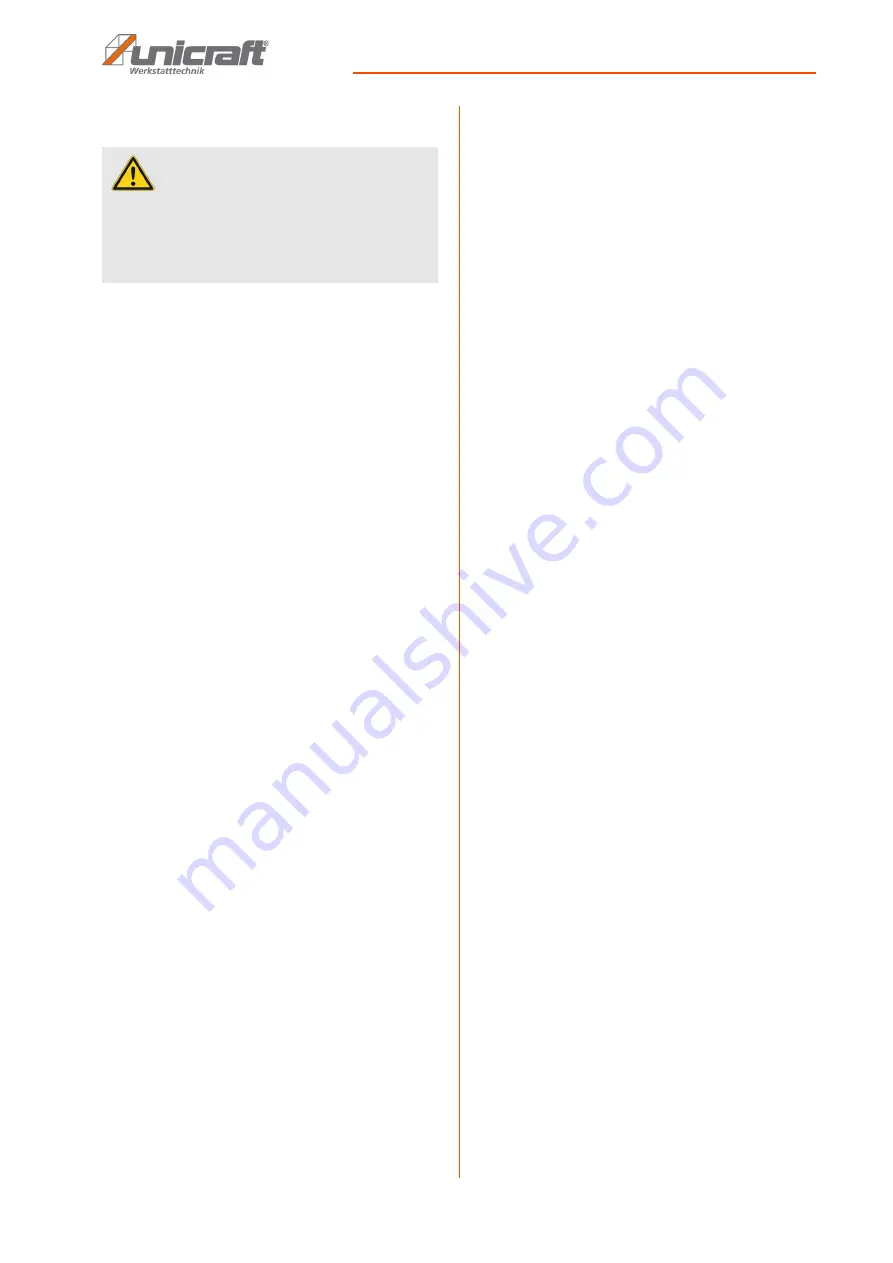
Safety
HT-Series | Version 1.01
7
2.7 Safety regulations
- The valid accident prevention regulations are to be
followed. If the lift table is intended for use by em-
ployees, it must be complied with in addition to the
relevant labor law regulations, eg. For example,
the accident prevention regulation General Regu-
lations (VBG 1).
- Before using the lift table, make sure that it is tech-
nically correct. Pay special attention to the wheels,
lifting and lowering device. Never use a damaged
lilift table. Make any repairs only by professionals.
- Never load the table with greater load or force than
the maximum load capacity.
- Pay attention to uniform load distribution!
- Never lift a load when the lift table is on an
unsuitable surface!
- Do not bring body parts (hands, fuses) under the
table when a load is lifted!
- Never try to move a load lifted from the lift table on
the table. A lifted load must never be exposed to
shock or shock loads.
- Never lift a load that can slip, or whose parts are
not firmly connected, with the lift table.
- Make sure that the operator of the lift table is al-
ways outside the range of a load that may slip or
fall off the table.
- Never leave a load lifted by the lift table unatten-
ded.
- Make sure that the ground on which the lift table
stands or where it is to be moved is sufficiently
loadable. If not, the lift table must be placed on
sufficiently solid wood or preferably metal planks
and moved there. Such a measure must be chec-
ked by an expert before lifting and moving a load.
- When using the lift table, it must be ensured that
the user can operate the lift table with the load
without any problems.
- We point out that in case of improper use no liabi-
lity for possible consequential damages can be
assumed.This also applies to the use of the lift ta-
ble that are not suitable for use, as well as any un-
authorized alteration to di esen, in particular for
the replacement of original parts with parts of
other origin.
2.8 Safety instructions for operating personnel
No operational mode which could compromise the
safety of the lift table lift platform may be undertaken.
The operator must also ensure that no unauthorised per-
sons work on the machine (e.g. also by actuating de-
vices to prevent unauthorised use).
The operator is responsible for checking the machine at
least once a day (before use) for externally visible da-
mage and defects, and for immediately reporting any
changes (including operating behaviour) that impair
safety.
The operator must ensure that the machine is always
operated in perfect condition.
If necessary, the operating personnel must be required
to wear protective clothing etc..
Safety devices must not be disassembled or put out of
operation (even here, specific reference must be made
to imminent hazards, e.g. imminent severe crushing,
loss of sight, danger to life).
If it is necessary to de-install safety devices during set-
up, repair and maintenance, the safety devices must be
re-installed immediately after completion of the main-
tenance or repair work.
ATTENTION!
Only use the lift table if you have familiarised
yourself with it or have been instructed on it. Read
the safety instructions on the lift table and in the
instructions for use carefully. The instructions must
be kept with the product for inspection.
Summary of Contents for HT 300 S
Page 26: ...www unicraft de ...