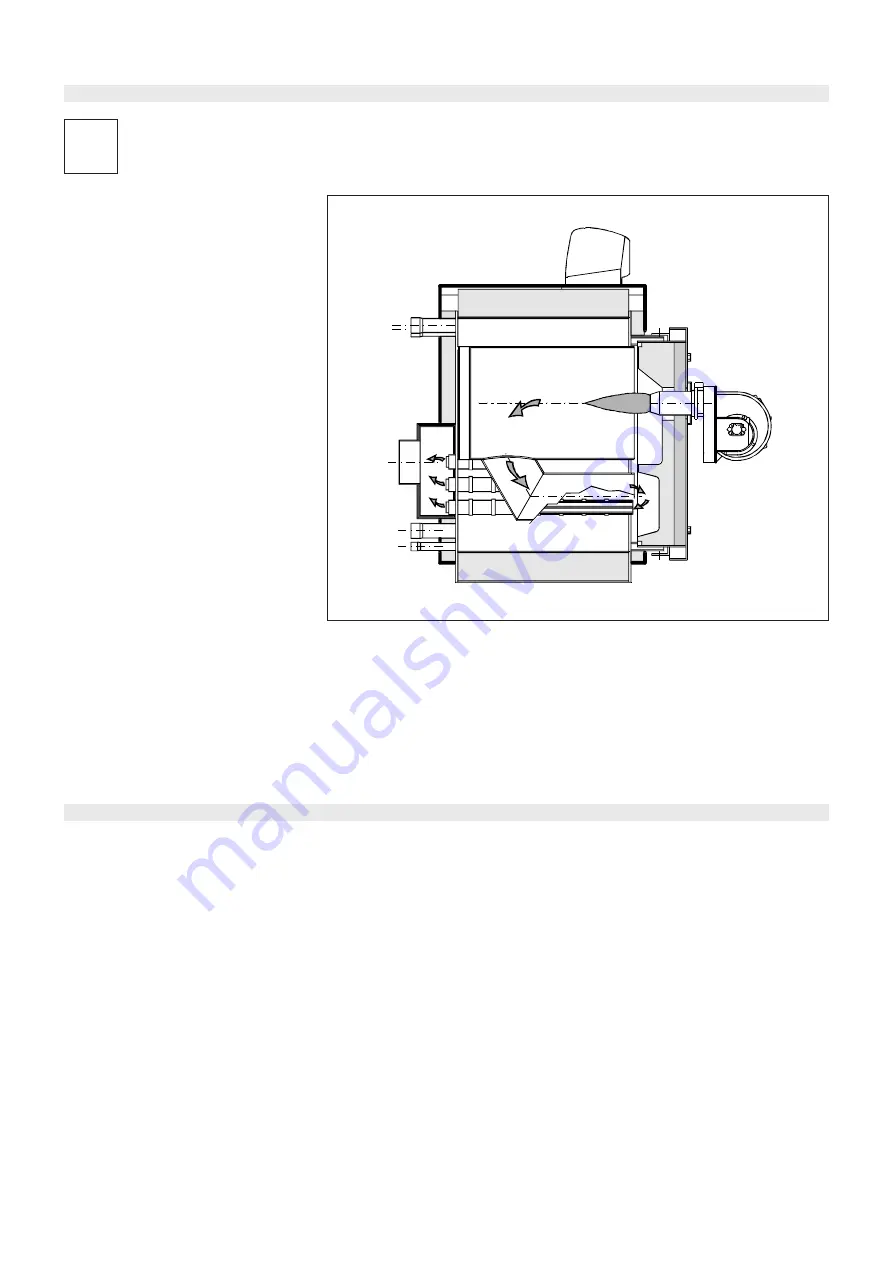
5
1
CONSTRUCTIONAL-DIMENSIONAL
TECHNICAL CHARACTERISTICS
1.1 - CONSTRUCTION OF
THE TRISECAL 3P
BOILERS
The TRISECAL 3P (short name: TS 3P) range
of boilers are /made of an external oval shell,
to whose inside are placed: in the highest
part the cylindrical furnace completely wet,
in which the first smoke pass takes place; in
the lowest part the flame reversion pipe, used
as second smoke pass and, beside to it, the
tube bundle, used as third smoke pass.
A special manifold, positioned in
correspondence of the flow ane return pipes,
optimises the water circulation and reduces
the stratification phenomenon, facilitating a
more homogeneous distribution of the water
temperatures inside the boiler body.
The guided route of the combustion gases
allows the maximum exploitation of the thermal
exchange surfaces and the uniform balance
of the material stress.
The tube bundle is positioned in the lowest
and coldest part of the boiler, because made
of special and patented pipes with controlled
heat exchange, which are able to impede the
condensate formation.
The special geometry of the TS/3P boilers
(reversed flame furnace) and the innovative
exchange surfaces (pipes at controlled heat
exchange) allow to use these boilers as sliding
temperature and Low NOx boilers.
The construction completely satisfies the
requirements of the EN 303 - part 1.
The sheet metal parts of the pressure vessel
are manufactured of certified carbon steel,
type S235JRG2, according to EN 10025, with
melting certificate 3.1.B, according EN
10024; where as the pipes are of steel
ST 37.0 according to DIN 1626.
fig. 1
The welders and the WPS (Welding Procedures
Specifications) have been approved according
to EN 287 and EN 288 by TÜV (DE). These
boilers and production facilities have been
also approved by - ISCIR (RO), UDT (PL) and
GOSGORTEKHNAZDOR (RU).
The boilers are equipped with a reversible
hinged door, which can be opened, for this
reason, from L.H. or R.H. side.
The outer shell is insulated with a glass wool
1.2 - WORKING PRINCIPLE
The NOx formation process is strongly
affected by:
-
the flame temperature;
-
the time during which the combustion
gases stay in a high temperature zone.
-
oxygen partial pressure and its
concentration.
The provisions to be adopted for the NOx
reduction are then:
-
reduction of combustion temperature;
-
reduction of the specific thermal input;
-
permanence time reduction of the gases
in the combustion chamber;
-
reduction of oxygen concentration.
UNICAL, to reduce the NOx formation on the
TS 3P range of boilers, has adopted the
following construction solutions:
-
three pass
the furnace is of direct flame type and not
of reversal type any more; the burner
flame results more compact and shorter,
thus reducing the permanence time at
high temperature;
the direct pass allows a quicker flame
cooling down by the water cooled furnace
surfaces;
-
specific thermal input reduction
the combustion chamber volume has been
increased if compared with standard
boilers of the same capacity.
With the adoption of the modern Low NOx
burners a further reduction of the NOx
emissions can be obtained with:
-
reburning
a part of the combustion gases is taken
and sent again to the combustion chamber
with the combustion air.
In this way the partial oxygen pressure is
reduced and the flame temperature is
reduced too.
-
reduction of the partial oxygen pressure
thanks to an air excess reduction.
During the operation of the burner within the
output range of the boiler, the combustion
chamber is always under positive pressure.
For the value of this pressure see tables on
pages 6 to 9 under the column "Smoke side
pressure losses".
The chimney has to be calculated in such a
way that at its base there is no positive
pressure.
matress, thick 80 mm (100 mm for models
TS/3P 450 & TS/3P 600), protected by a textile
in mineral fiber.
The upper part of the outer shell is equipped
with uplift hook(s).