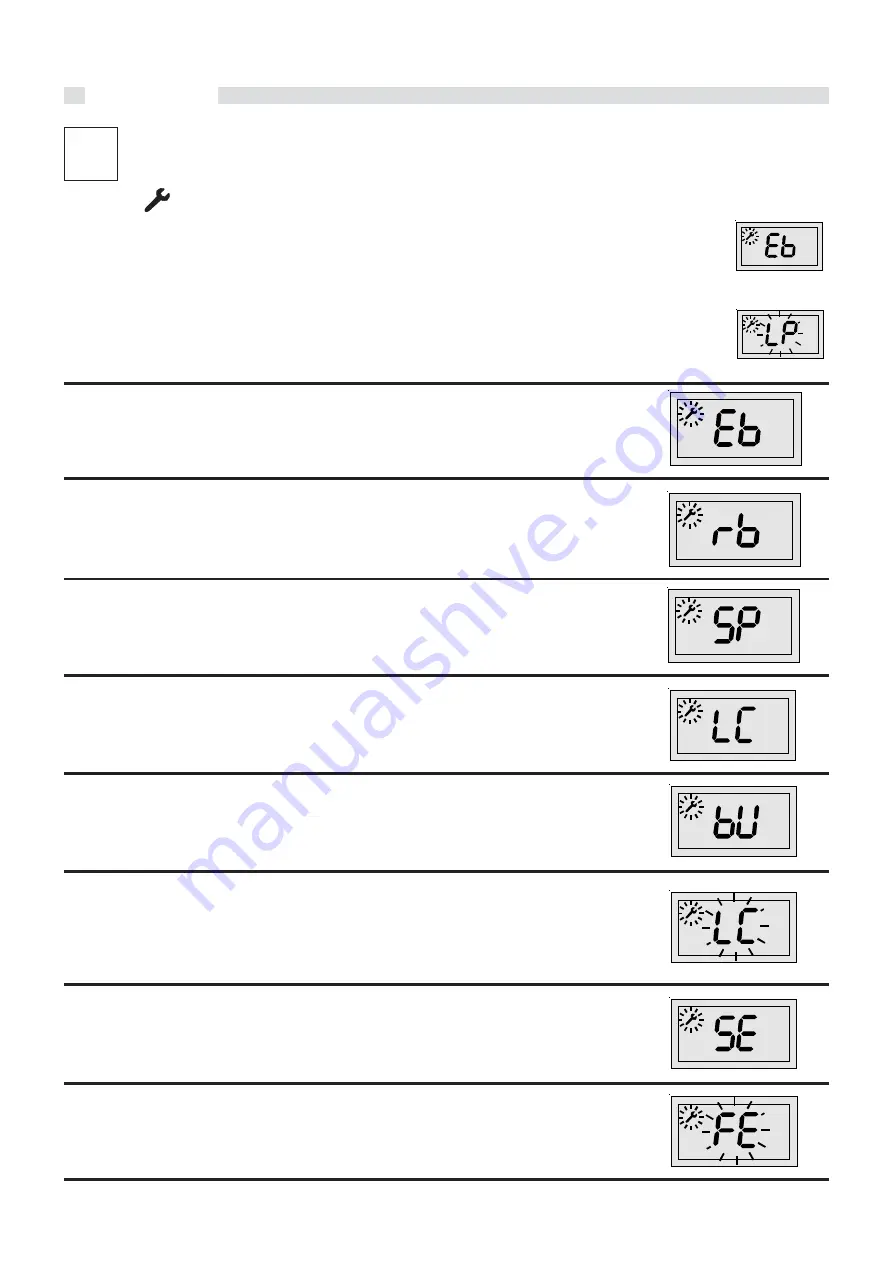
40
Codes fault
5
The symbol flashes on the display when the boiler detects a fault.
1) In case of a fault which does not causes the stop of boiler operation, to show the error code it is necessary
to press the reset push button. If the boiler is in stand-by the error code appears in the display also without
pressing the reset push button.
2) In case of an error code which causes the stop of boiler operation, the error code is shown directly on the
display in flashing mode.
Each error is characterized by a priority level: if two errors are detected at the same time, the error code with
higher priority is shown.Here below the list of the known errors.
Outer temperature sensor (priority 0)
Description:
Outer temperaturesensor interrupted
Possible solutions:
Inspect the harness; if necessary replace the outer sensor
.
Heating return temperature sensor (priority 1)
Description:
Return temperature sensor interrupted
Possible solutions:
Inspect the harness; if necessary replace the return temperature sensor
.
Working parameters (priority 2)
Description:
Working parameters corrupted
Possible solutions:
Re-introduce the correct working parameters.
Insufficient circulation (priority 3)
Description:
Insufficient circulation in the primary circuit
Possible solutions:
Inspect the operation of the pump and its speed adjustment
Mistension supply to the burner (priority 4)
Description:
It depends on the electrical supply (Frequency and Voltage out of the standard limits)
Possible solutions:
Wait for the values entering within the limits
Heating flow and return temperature sensors (priority 5)
Description:
Water circulation through primary circuit
very
weak
Possible solutions:
Inspect the operation of the pump and its speed setting; remove possible obstructions of the
C.H. system; clean the possible fouled D.H.W. heat exchanger.
Heating flow and return temperature sensors (priority 6)
Description:
Heating flow and return temperature sensors inverted
Possible solutions:
Inspect the harness
Fan (priority 7)
Description:
Alteration of the fan speed
Possible solutions:
Inspect the operation of the fan and its harness.
°C
°C
°C
°C
°C
°C
°C
°C
°C
°C
FAULT CODES