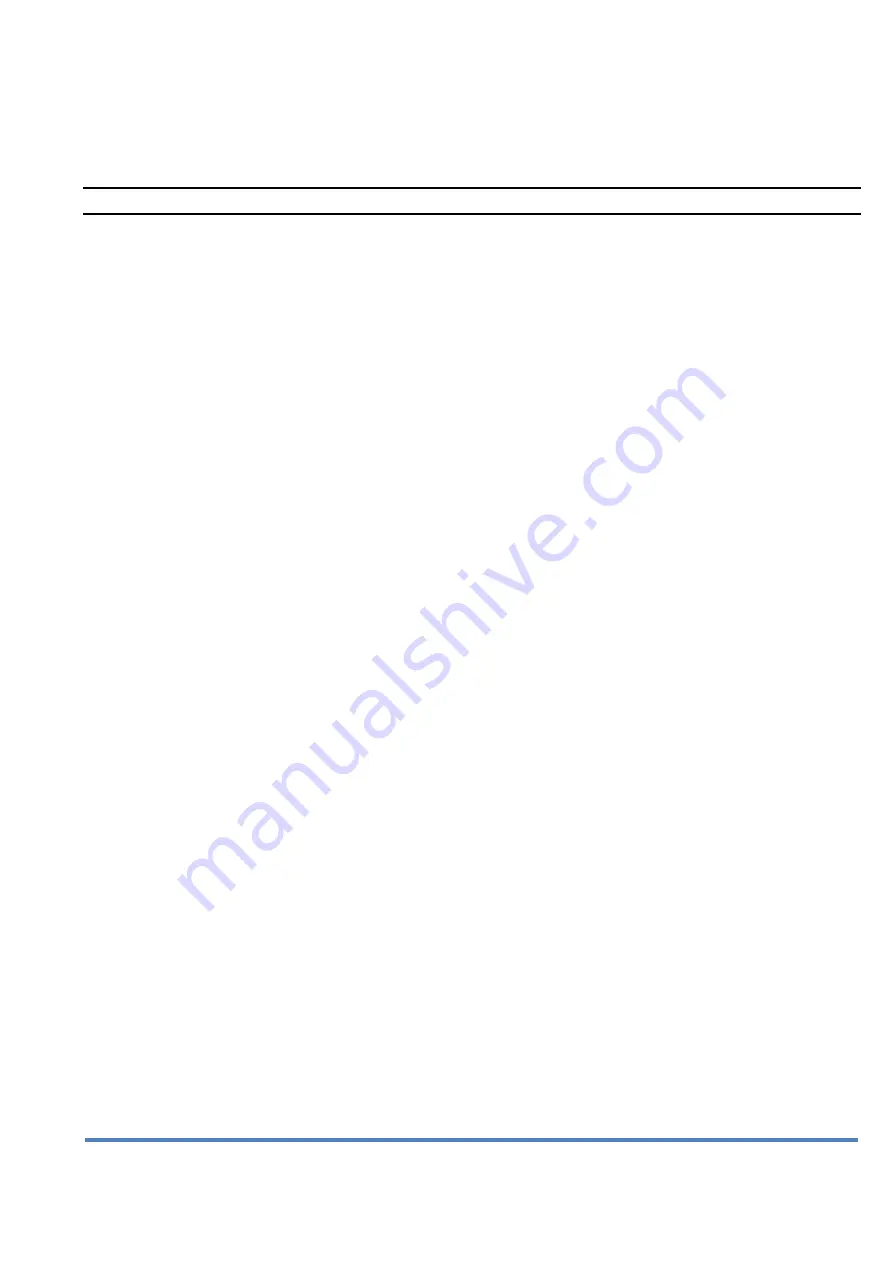
Uni-trol Co. Ltd. , ul.Estrady 56, 01-932 Warsaw, Poland
Ph./Fax + 4822 817 9422 e-mail: [email protected]
11
pressure at the overflow valve is set at 160 bar. The monoblock
two-chamber hydraulic divider
enables to change the direction of the servo-
motor pistons movement. The straightening piston’s
control chamber is switched by means of the hand lever, while the adap
ter piston’s chamber – by
means of the electromagnets (switched on by the control panel).
The capacity of the oil tank on the hydraulic pump is about 8 liters. The oil level is checked on the
oil indicator
– figure 3.
The hydraulic system’s scheme is presented in the figure 7.
11.0 WHEEL RIM STRAIGHTENING MACHINE OPERATION
The machine is supplied with the hydraulic system to mount wheel rims. Clamping is carried by
the hydraulic servo-motor set in the central position by means of a suitable adapter - figure 4.
There are three mechanical pressures supplied:
- a four-bolt mechanical pressure and a five-bolt mechanical pressure with regulated
setting of bolts from dimension 98 mm to dimension 140 mm.
- a universal mechanical pressure (three-, four-, and five-bolt with regulated setting of
bolts from dimension140 mm to dimension 210 mm (dimensions 98-210 mm for the
three-bolt system)
11.1 GENERAL PROTECTION INSTRUCTIONS
Before operation of the wheel rim straightening machine, read attentively the following
instructions:
- Some rims require the use non-standard of centering rings or working tools. In order
to provide correct operation and safety, non-standard spare parts must be re-
supplied by the manufacturer (or the distributor) on the cu
stomer’s order against
payment.
- The machine is used to correct wheel rims. If after the shape correction the rim
needs to be balanced, it must be done on the proper machine (balancing machine).
- The machine is not adapted to operations involving washing. The use in humid
conditions is not recommended.
- The machine must not be used by unauthorized personnel.
- The machine must be used only according to its purpose.
- Make sure the rims and the standard equipment tools, used during correction, meet
the instructions of the manufacturer.
- Before operation, check the indicator of the oil level of the hydraulic pump.
- Make sure the motor is turning in the right direction.
- If the machine is not working properly, turn it off and call for the technical service.
-
In case of sudden accidents and/or during the machine’s inspection, press the
“emergency stop” (ENERGIA STOP) button.
- Do not modify the safety devices.
- Fix all parts of the machine carefully in order to avoid any hazards, and wear
protective goggles.
- Proceed slowly during operation with the straightening piston; Rapid use of piston
with big force may cause a durable damage of the rim. You must wear the
protective goggles during this operation.
- Always check a proper clamping the rim in the adapter.
- Always monitor the normal level of the pressure. If it exceeds, turn the machine off.
-
Always control the direction of the motor’s movement. Rotation in the wrong
direction may damage the motor and the machine.
-
Do not overload the machine’s hand control lever.