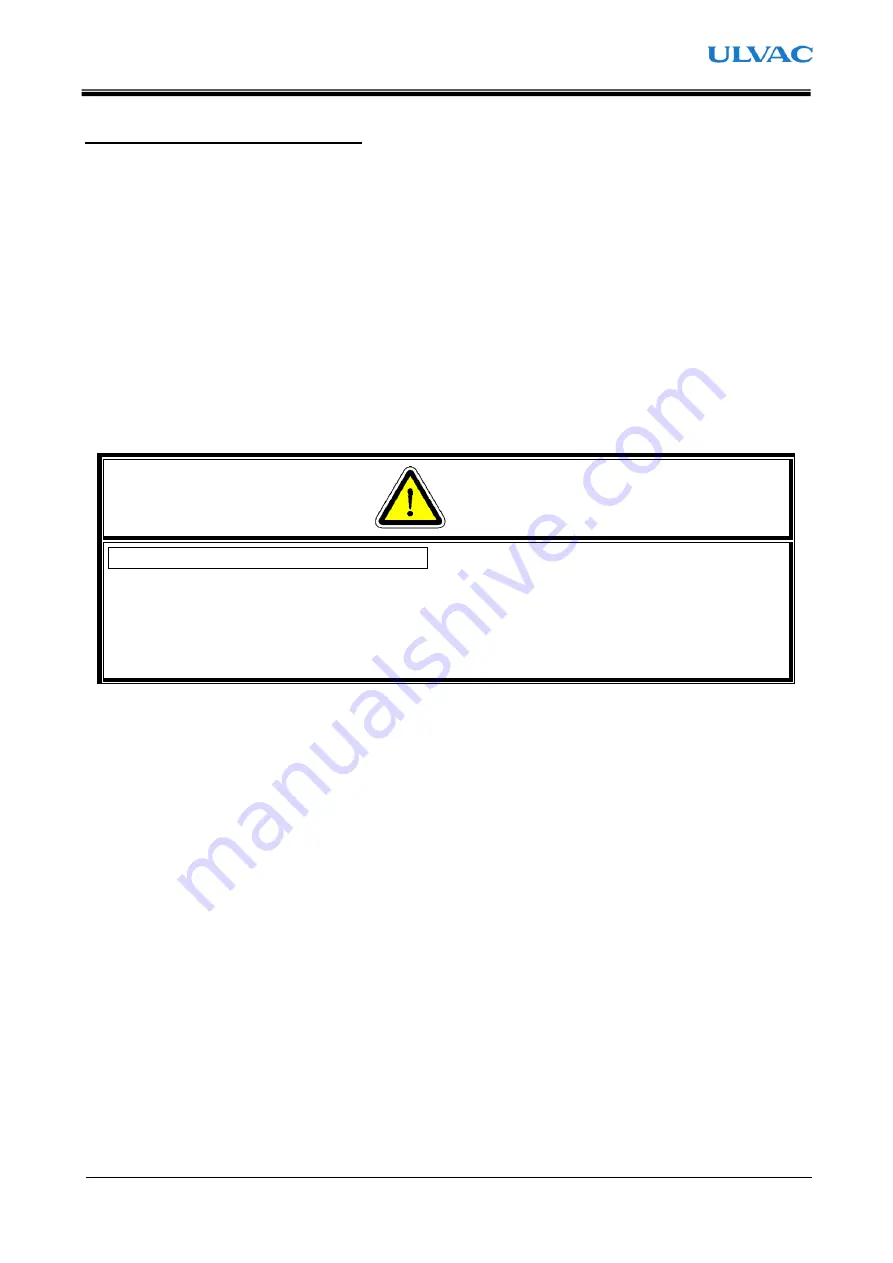
Before use
02
Confirmation in unpacking
When unpack the pump from the shipping case, please check the following items.
(1) Whether the pump accords with required pump.
(2) Whether the accessories and prescribed items are accompanies.
<Standard accessories>
Instruction Manual --------------------------------------------------------------------------------1 copy
Inlet-exhaust pipe protection cap (attached to Inlet-exhaust pipe) -------------------2 pcs.
(3) Whether damaged positions are found.
(4) Whether loosen external screws or inlet-exhaust pipe. Whether coming off positions are
found.
In case there is trouble by any chance, please contact vendor or ULVAC Sales Department.
To customers who purchased "DAU-20"
Never grab or bend the tube on the side part of the pump.
When I take out a pump
from a packing box.
It might break the tube and/or deteriorate the pump performance.
Be sure to grip the handle to pull out.
ATTENTION