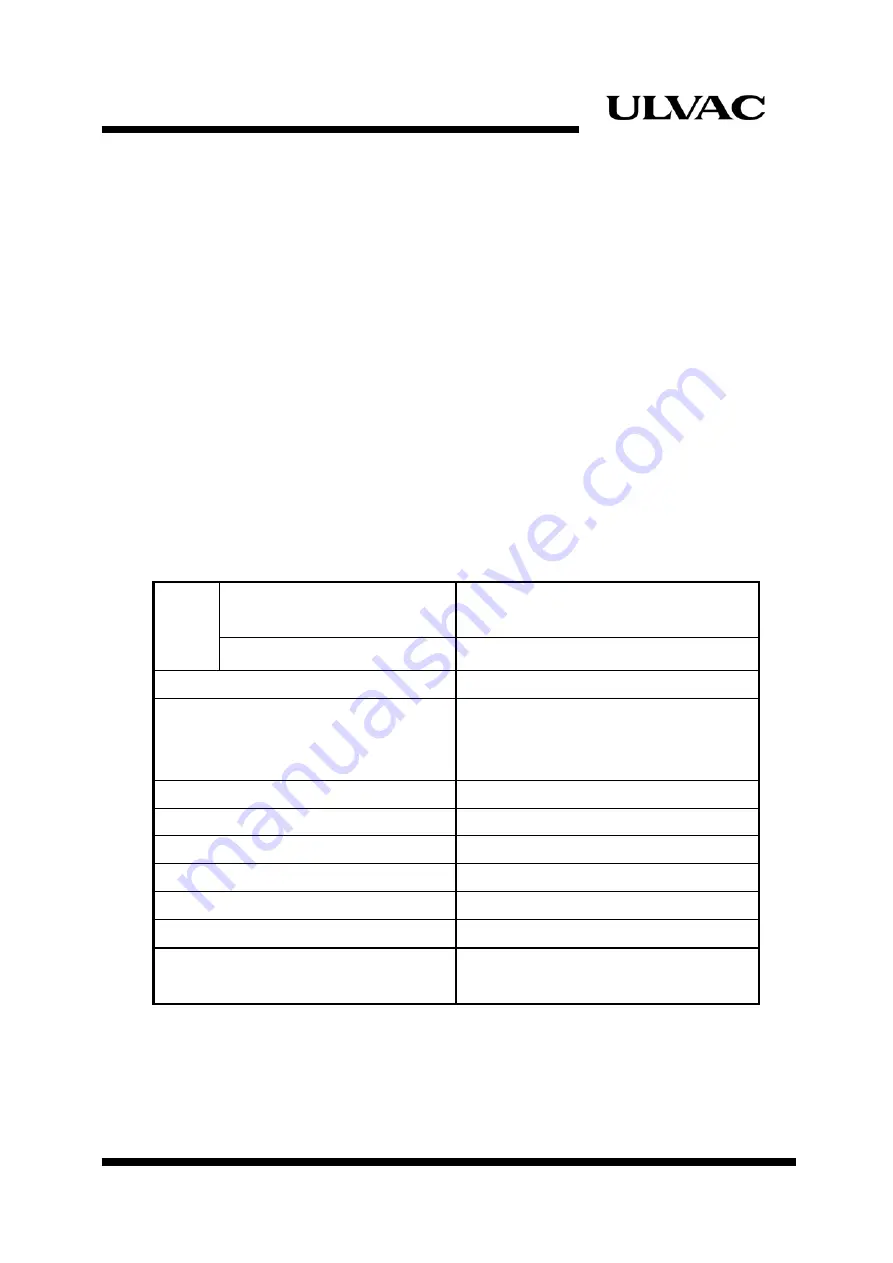
Compressor Unit Instruction Manual
ULVAC CRYOGENICS INCORPORATED
1-1
1. COMPRESSOR UNIT DESCRIPTION
1.1
General
The compressor unit supplies and circulates helium continuously in the cryopump system
for operation of the refrigerator unit (coldhead).
The C15T compressor unit consists of: 1) compressor motor, 2) cooling system, 3) oil
separation system and 4) adsorber.
See Table 1-1 for the standard compressor specifications.
1.2
Specifications
Table 1-1
Compressor Unit Standard Specifications
◆
Model :
C15T
Power
Source
Voltage x Phase x Frequency
190 - 220VAC x 3
Φ
x 50Hz
200 - 230VAC x 3
Φ
x 60Hz
Power (in normal operation)
(*1)
3.3kW / 4.1kW(50Hz/60Hz)
Cooling Type
Water cooled
Cooling Water Requirement
(See Fig.3-2)
Temperature : 5 - 32°C
Flow Rate : 2 - 6L/min
Pressure Drop : 0.04 - 0.17MPa
Ambient Temperature
10 - 38°C
Compressor Winding Resistance
1.63
Ω
,
Adsorber Replacement Cycle
30,000 hours
Current (normal operation)
13A (200V, 60Hz)
Weight
100kg
Cooling Water Inlet/Outlet
Rc3/8 female
Helium Gas SUPPLY/RETURN
Connector
1/2B self-sealing coupling
(*1) T
he power consumption shows the figure when flexible hose of 3m is used and
helium charge pressure is 1.60MPaG. The power consumption is higher by 10%
for 5 minutes from the startup.
Summary of Contents for C15T
Page 2: ......
Page 8: ...F 6 ULVAC CRYOGENICS INCORPORATED This page intentionally left blank...
Page 14: ...S 4 ULVAC CRYOGENICS INCORPORATED This page intentionally left blank...
Page 16: ...IW 2 ULVAC CRYOGENICS INCORPORATED This page intentionally left blank...
Page 34: ...Operation 4 2 ULVAC CRYOGENICS INCORPORATED This page intentionally left blank...
Page 38: ...Disconnection and Storage 5 4 ULVAC CRYOGENICS INCORPORATED This page intentionally left blank...
Page 46: ...Maintenance 6 8 ULVAC CRYOGENICS INCORPORATED This page intentionally left blank...
Page 50: ...Troubleshooting A 4 ULVAC CRYOGENICS INCORPORATED This page intentionally left blank...
Page 54: ...Circuit Diagram B 4 ULVAC CRYOGENICS INCORPORATED This page intentionally left blank...
Page 57: ...Flexible Hose C 2 ULVAC CRYOGENICS INCORPORATED This page intentionally left blank...
Page 61: ...CS 2 ULVAC CRYOGENICS INCORPORATED This page intentionally left blank...
Page 63: ...Revisions R 2 ULVAC CRYOGENICS INCORPORATED This page intentionally left blank...