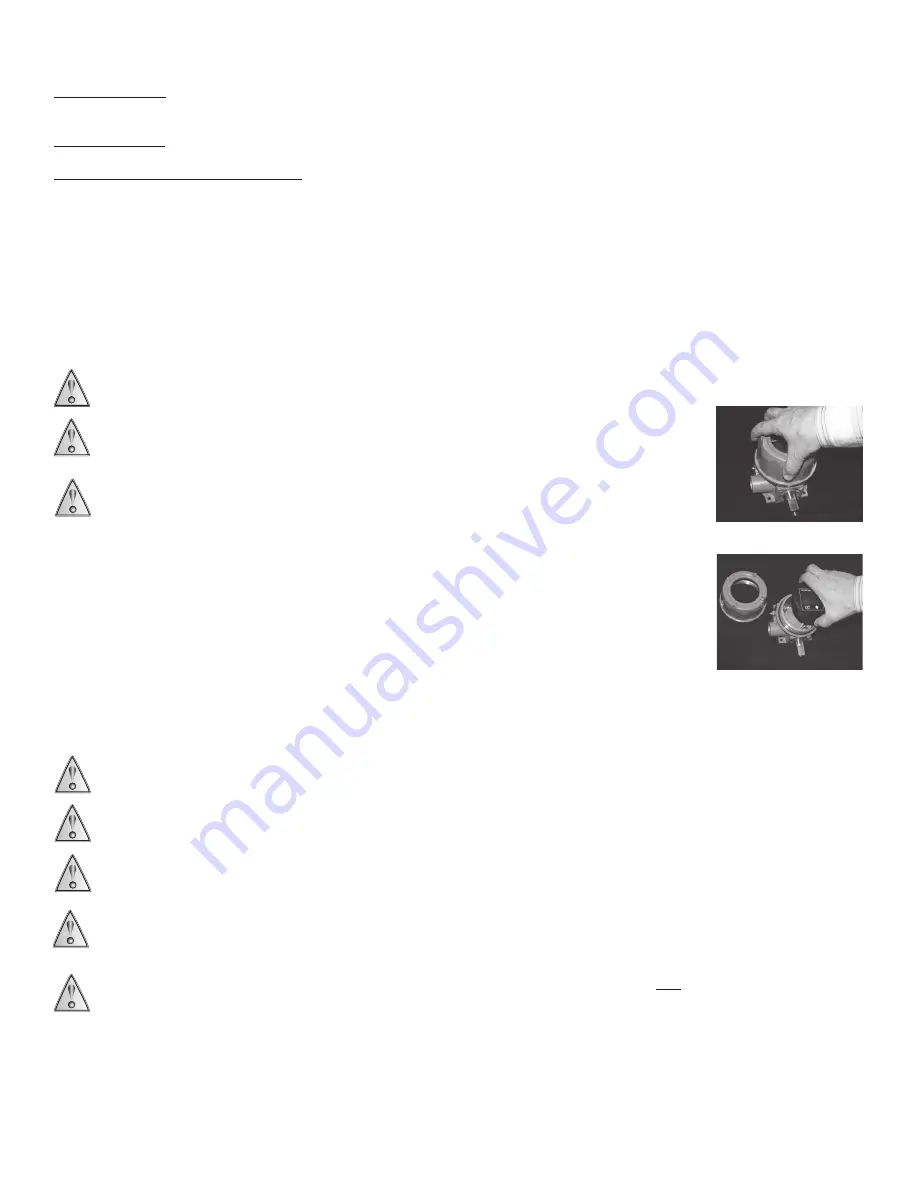
IM_1XSW-02
www.ueonline.com
5
thread sealant, is required to maintain enclosure type 4X/IP66.
For Remote Sensing: Route the extension wire to avoid contact with live components or close proximity to electrical noise sources. Avoid kinks, or
excessive flexing. Tighten the ferrule fitting, if applicable.
For Surface Sensing: Secure the sensor housing to the pipe or vessel using an adhesive or strapping method suitable for the application.
For Immersion Sensing (models C, H, R & L): Use of a thermowell is highly recommended to aid in maintenance, testing and preservation of the
system integrity. Insert the sensor housing (0.25” diameter) into the well ensuring that the sensor’s sheath bottoms out and the well is completely
immersed in the media (2.5” min.) Screw the sensor’s nipple into the thermowell, with thread sealant, by placing a wrench on the union nut. Tighten
the union connector.
For best temperature measurements, the sensor housing must be in full contact with the surface or media being measured. Heat transfer compound
may be used to aid in fully transferring the media temperature to the sensor housing. Locate where the temperature is most representative of the
system. Minimum insertion depth is 2-1/2”. Sensor dimensional drawings are shown on page 20.
PART II - WIRING
Removing the One Series Enclosure Cover and Display Module
TO PREVENT ELECTROSTATIC DISCHARGE WIPE DOWN COVER AND ENCLOSURE OF ANY DUST BUILD-UP BEFORE REMOVING COVER.
DISCONNECT ALL SUPPLY CIRCUITS BEFORE WIRING DEVICE. WIRE DEVICE IN ACCORDANCE WITH LOCAL AND
NATIONAL ELECTRICAL CODES. MAXIMUM RECOMMENDED WIRE SIZE AND TIGHTENING TORQUE FOR FIELD
WIRING TERMINAL BLOCKS ARE SHOWN WITHIN TABLE 3(PAGE 8).
TO PREVENT SEIZURE OF ENCLOSURE COVER, DO NOT REMOVE LUBRICANT. THREADS SHOULD ALSO BE FREE OF DIRT
AND OTHER CONTAMINANTS.
Remove the enclosure cover by turning it counter-clockwise for 7 revolutions (Figure 2). Carefully remove the display
module by grasping the outer edge and pulling it away from the base enclosure (Figure 3), being careful not to
strain any of the wired connections. Allow the display module to hang from the wired connections to access the base
enclosure and terminal blocks for wiring. Do not remove the display module wire assemblies. Insert the field wiring
through the conduit opening(s) of the base enclosure. Make the connections as shown within the wiring diagrams
beginning (Figures 4-8, page 6-7).
The primary chassis and equipment grounding terminal
is
provided inside the base enclosure.
Cleaning the display and keypad surface should be performed with a damp cloth only. Do not attempt to wash down
the One Series with the cover removed.
WIRING FOR FLAMEPROOF & NON-INCENDIVE INSTALLATIONS
Tools Required:
Small flat-head screwdriver; wire strippers
TO PREVENT IGNITION, DISCONNECT POWER BEFORE REMOVING ENCLOSURE COVER. KEEP COVER TIGHT WHILE IN OPERATION. DO NOT
DISCONNECT EQUIPMENT UNLESS POWER HAS BEEN SWITCHED OFF OR THE AREA IS KNOWN TO BE NON-HAZARDOUS.
DO NOT REPLACE COMPONENTS UNLESS POWER HAS BEEN SWITCHED OFF OR THE AREA IS KNOWN TO BE NON-HAZARDOUS.
THE DEVICES SHALL BE PROPERLY GROUNDED IN THE END USE APPLICATION USING THE GROUND SCREWS PROVIDED WITH THE ENCLOSURE.
FIELD WIRING MUST BE RATED 105°C MINIMUM. FOR AMBIENT TEMPERATURES BELOW -10
°
C, USE SUITABLE FIELD WIRING.
MODELS 1XSWLL AND 1XSWHL DERIVE THEIR POWER DIRECTLY FROM A PLC/DCS DISCRETE INPUT OR OTHER LOW-CURRENT DC LOADS
(Figures 4-5, page 6). THE SWITCHED OUTPUT MAXIMUM LOAD RATING IS 0.1A.
THE DEVICE MUST NOT BE CONNECTED DIRECTLY TO
A POWER SUPPLY WITHOUT AN APPROPRIATE CURRENT LIMITING LOAD SUCH AS THAT PROVIDED BY A PLC/DCS DISCRETE
INPUT.
OVERLOADING THE SWITCH MAY CAUSE FAILURE (SEE TABLE 2).
Figure 2
Figure 3