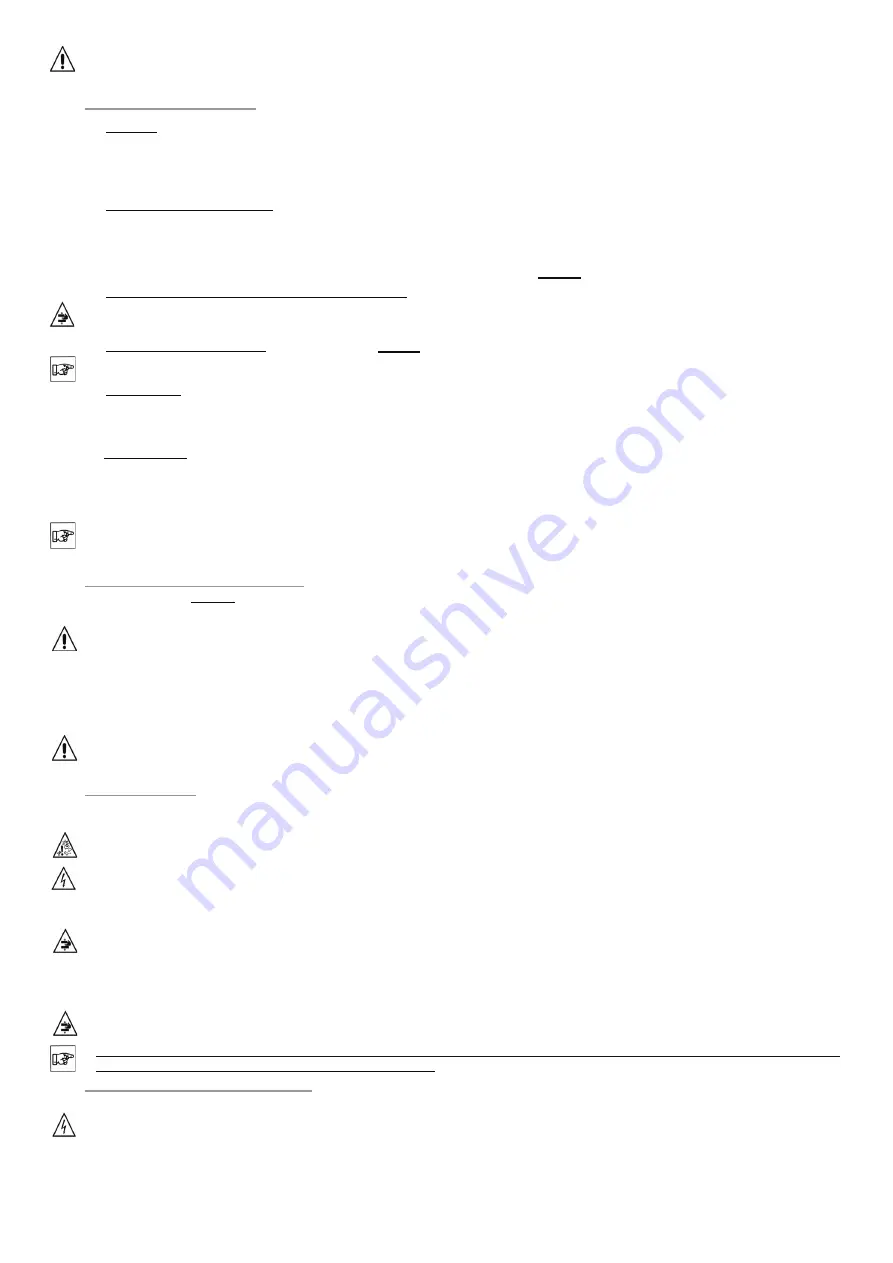
Doc. 82082-Z Rev. 04/07/07
4 / 8
Dis. 17088/l
Warning:
applications using the AVL model require an access plate or port to allow for a swift release of the actuator from the
mounting bracket in the event of a power failure or other emergency need to gain access to the engine room or area
confined by the use of the hatch actuator.
NOTES ON THE ACTUATOR
1. Actuator:
- Outside diameter: 48 mm
- Length (X) in closed position: (377 + stroke) [mm] (14.7/8” + stroke)
- n° 2 mounting brackets and pins.
- the rear bracket allows a 125° oscillation range of the actuator.
2. Actuator voltage supply cable:
- the actuator is supplied with 1,5 m (5 ft) of four-core cable: 2 poles with a section of 1,5 mm² (for voltage supply REF.2) and 2
poles with a section of 0,5 mm² (for scheme of connection REF. 8).
Warning
: in case the 2 poles of the voltage supply cable (REF.2 ) need to be extended, do not substitute the existing harness.
Make a junction using a cable having the same features as shown in
table A
.
3. 3 position change-over centre off momentary 2 sides: (not supplied).
Warning
: use a momentary switch only! Do not use a switch that allows the operator to lower or raise the hatch actuator
without constantly depressing the switch.
4. Battery voltage supply cable (not supplied): see
table A
.
Warning
: the length of the voltage supply cables (2 + 4 referred to fig. 4 and 5) must not exceed 15 m (50 ft).
5. Delayed fuse (not supplied):
for the installation of single actuator is suggested to protect the wiring harness with a 10A delayed fuse for the 24V actuator
and 15A for the 12V; for dual installation it is suggested to protect the wiring harness with a 15A delayed fuse for the 24V or 30A
for 12V
6-7. Voltage supply (battery or power supply) and :
- For 12V single actuator: 12 VDC –10% +30% 10A minimum.
- For 24V single actuator: 24V DC –10% +30% 5A minimum.
- For 12V dual actuator: 12 VDC –10% +30% 20A minimum.
- For 24V dual actuator: 24V DC –10% +30% 10A minimum.
Warning
: the relays contacts in fig. 4-5 must withstand 20A DC continuous current (not supplied).
The wire cross-section for the command electrical junction described in fig. 4 and 5 (REF. 7) must be 1,5 mm
2
(not
supplied).
INSTALLATION (table B and fig. 2-3)
"!
The equation in
table B
identifies the maximum strength (in Newton) required to raise the hatch lifter, given the features of the
hatch and the position of the fixing brackets:
Warning:
maximun load (Fmax) for actuator with the non-locking ram is: 1200 N (265 lbs) under thrust (2400 N, 530 lbs, for dual
installations).
Maximun load (Fmax) for actuator with the locking ram is: 1200 N (265 lbs) under thrust and 650 N (143 lbs.) under
traction (2400 N, 530 lbs, under thrust and 1300 N, 286 lbs, under traction, for dual installations).
"!
Attach the connector and the rear joint respectively to the moving element (hatch) and to a fixed point of reaction (for example the
engine room wall).
"!
Attach the Electromechanical hatch lifter to the brackets with the pins supplied.
Warning:
to guarantee the total closing of the hatch increase the X length for about 10 mm (fig. 2-3).
Make sure the two fixing brackets are lined up to avoid transversal load.
Verify the oscillation range of the actuator is within the allowed values (max 125°).
SAFETY NOTICES
"!
The actuator shall be installed by qualified technicians.
"!
Prior to installation make sure that:
- the actuator performances comply with the estimated application
- hatch profiles and fittings are suitable to the stresses caused by the actuator
- the existing electric systems comply with the regulations in force
-
power supply features are those indicated in the actuator specifications
"!
When lowering the hatch actuator, particularly the AVL hatch actuator, make sure that there are no obstructions (power cords, etc.)
and that there is no one near the hatch that could be injured while the hatch is being closed.
"!
When assembling and disassembling the actuator, take proper precautions to avoid accidental closing of the window which might
cause injuries to people (impact-squashing-cutting-shearing).
"!
At least once a year check at sight for damages or wear in the supply cable.
"!
When installing the AVL hatch lifter it is important that the actuator is at the bottom of its stroke when the hatch is fully closed. If not,
the actuator will continue to pull with a force of 143 pounds (or 286 pounds for dual application), which may cause damage to the
boat.
"!
The AV and AVL hatch actuators are not intended for use on companionway doors or any other areas where persons may be
obstructed from a rapid evacuation from the vessel for any reason.
"!
Do not carry out any intervention on the actuator, do not remove or disassemble parts of the actuator; in case of malfunction or
damaged cable contact “UCS Ultraflex Control Systems srl”.
ELECTRICAL CONNECTION (fig. 4- 5)
"!
Connect the voltage supply following the diagrams on fig. 4-5.
Warning:
Check the accuracy and solidity of all electrical connections.
"!
Connect the power supply and check the operation.