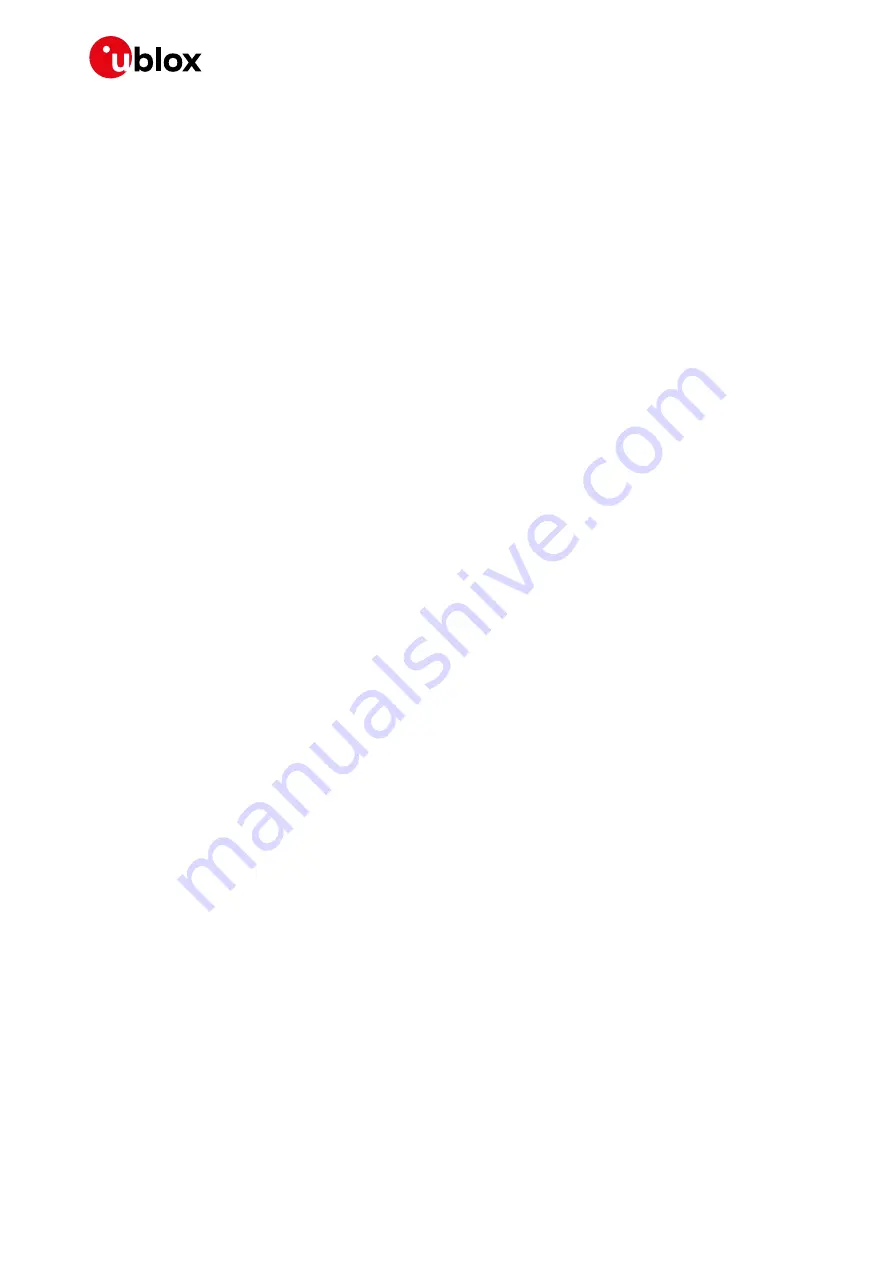
TOBY-L2 and MPCI-L2 series - System Integration Manual
UBX-13004618 - R28
Design-in
Page 80 of 164
2.2.1.9
Guidelines for VCC or 3.3Vaux supply layout design
Good connection of the module VCC or 3.3Vaux pins with DC supply source is required for correct RF
performance. Guidelines are summarized in the following list:
All the available VCC / 3.3Vaux pins must be connected to the DC source
VCC / 3.3Vaux connection must be as wide as possible and as short as possible
Any series component with Equivalent Series Resistance (ESR) greater than few milliohms must
be avoided
VCC / 3.3Vaux connection must be routed through a PCB area separated from RF lines / parts,
sensitive analog signals and sensitive functional units: it is good practice to interpose at least one
layer of PCB ground between the VCC / 3.3Vaux track and other signal routing
VCC / 3.3Vaux connection must be routed as far as possible from the antenna, in particular if
embedded in the application device
Coupling between VCC / 3.3Vaux and digital lines, especially USB, must be avoided.
The tank bypass capacitor with low ESR for current spikes smoothing described in section
should be placed close to the VCC / 3.3Vaux pins. If the main DC source is a switching DC-DC
converter, place the large capacitor close to the DC-DC output and minimize VCC / 3.3Vaux track
length. Otherwise consider using separate capacitors for DC-DC converter and module
The bypass capacitors in the pF range described in
close as possible to the VCC / 3.3Vaux pins. This is highly recommended if the application device
integrates an internal antenna
Since VCC / 3.3Vaux input provide the supply to RF Power Amplifiers, voltage ripple at high
frequency may result in unwanted spurious modulation of transmitter RF signal. This is more likely
to happen with switching DC-DC converters, in which case it is better to select the highest
operating frequency for the switcher and add a large L-C filter before connecting to the TOBY-L2
and MPCI-L2 series modules in the worst case
If VCC / 3.3Vaux is protected by transient voltage suppressor to ensure that the voltage maximum
ratings are not exceeded, place the protecting device along the path from the DC source toward
the module, preferably closer to the DC source, otherwise protection functionality may be affected
2.2.1.10
Guidelines for grounding layout design
Good connection of the module GND pins with application board solid ground layer is required for
correct RF performance. It significantly reduces EMC issues and provides a thermal heat sink for the
module.
Connect each GND pin with application board solid GND layer. It is strongly recommended that
each GND pad surrounding VCC pins have one or more dedicated via down to the application board
solid ground layer
The VCC supply current flows back to main DC source through GND as ground current: provide
adequate return path with suitable uninterrupted ground plane to main DC source
It is recommended to implement one layer of the application PCB as wide as possible ground plane
If the application board is a multilayer PCB, then all the board layers should be filled with GND plane
as much as possible and each GND area should be connected together with complete via stack
down to the main ground layer of the board. Use as many vias as possible to connect ground planes
Provide a dense line of vias at the edges of each GND area, specially along RF and high speed lines
If the whole application device is composed by more than one PCB, then it is required to provide a
good and solid ground connection between the GND areas of all the different PCBs
Good grounding of GND pads also ensures thermal heat sink. This is critical during connection,
when the real network commands the module to transmit at maximum power: proper grounding
helps prevent module overheating.