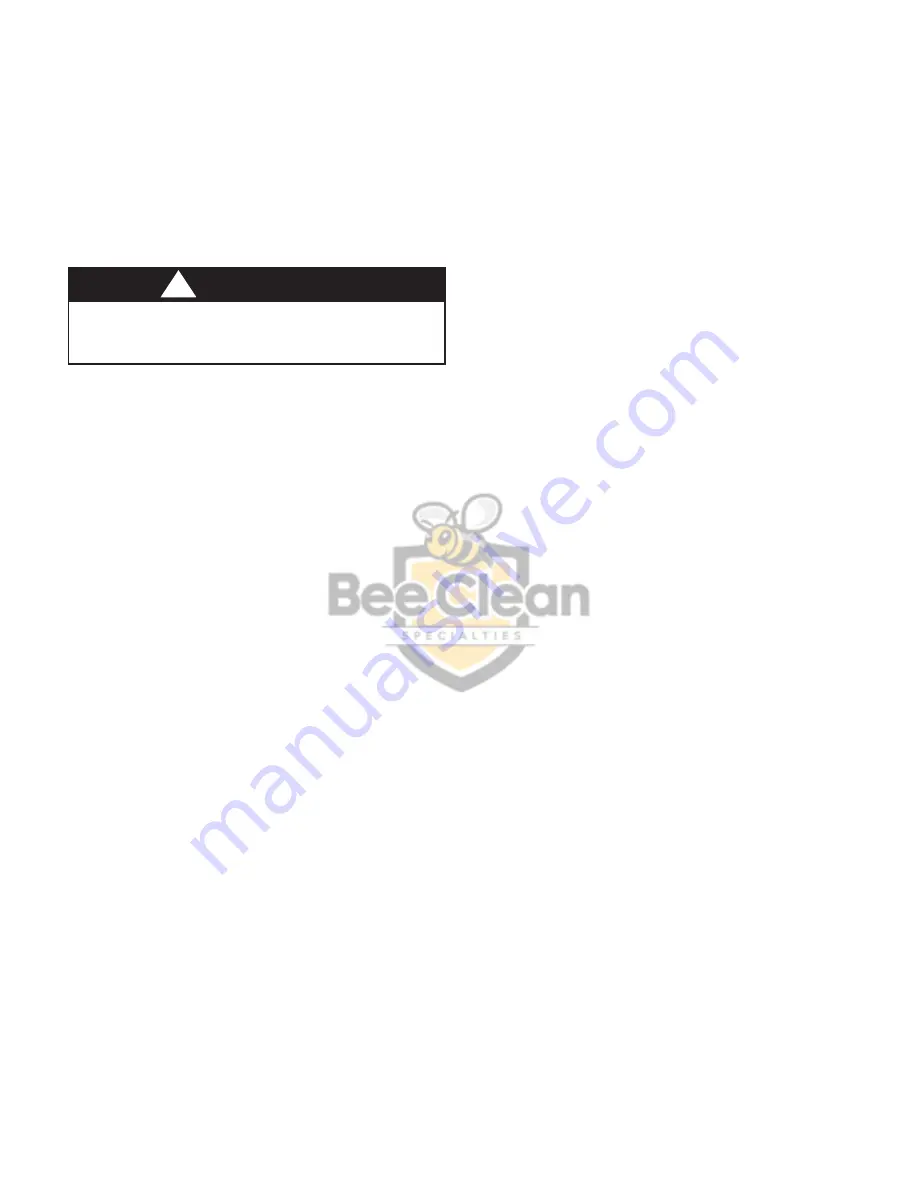
6
Model SH-PP Owner’s Manual
Detergents are available through United Air Specialists
for specific applications and contaminants.
Detergent Strength. Detergent concentration, or
“strength,” in a mixture with water varies with the
application from 1:1 to 5:1 to even 20:1 parts water to
parts detergent, refer to detergent manufacturer’s
directions. More or less detergent may eventually be
required for effective cleaning at reasonable detergent
cost. Typically, 20:1 is recommended as a starting point.
Experimentation is almost always necessary.
Water Temperature. Detergents can be up to twice as
effective in hot water, and hot water alone is very
effective in softening built-up residue. Water temperature
should be 140
°
F to 180
°
F, not to exceed 190
°
F.
Agitation/Impingement. These methods are virtually
the same, with impingement being the most extreme
form of agitation. Any liquid movement over built-up
residue will dissolve some of the contaminant, allowing
detergent to work on the next layer. A reduction in
cleaning time duration usually results.
Cleaning Cycle Duration. In most cleaning methods,
adequate time must be allowed for the detergent to
dissolve the contaminant thoroughly. Reaction time will
vary depending on detergent strength, temperature and
agitation. Guidelines for mixing, heating and expected
results are included on specification sheets for most
detergents.
Rinse Procedure. Cleaned components must be rinsed
off quickly and thoroughly to remove any remaining
contaminants. Even if the components appear to be
clean, some detergent residue may remain. This should
be removed because the residue may contribute to
voltage bleed-down when the components are placed in
service. Also, even though the detergent is “buffered”
(i.e., treated to prevent deterioration of the aluminum),
prolonged contact with the components could cause
minor corrosion. As with cleaning, hot water should be
used for rinsing.
Dry-Out Time. Collection components should be dry
before the system is placed back into operation. Start-
up of a wet system causes dead shorts and/or arcing
conditions. Wet ionizers, collector cells and mesh filters
should be placed in a warm room until they are dry.
Techniques such as hand wiping insulators and blowing
dry with compressed air will greatly shorten drying time.
Cleaned components may also be dried out by placing
them in the system and placing the system on-line, with
all power pack enclosure toggle switches in the off
position for approximately 30 minutes.
6.3
Manual Cleaning Methods
The manual cleaning method selected for a given
system will depend on the type of contaminant, rate of
deposit, facility limitations such as cleaning time
windows (process down time) and available utilities. Any
one of the following three acceptable cleaning methods
may be included in such a plan.
Hot Detergent Soak Tank. This method involves placing
components in an agitated solution of hot water and
detergent, and is the most effective method. With proper
detergent selection, this procedure will quickly remove
most contaminants collected in a precipitator.
Components should not be placed in highly
concentrated detergent solutions or allowed to soak for
extended periods (e.g., overnight), especially at
elevated temperatures. Extended soaking (e.g., days) in
solvent or detergent solution will degrade components
over time and should be avoided.
Automatic Parts Washers. Certain commercially-
available units combine and automate the features
necessary for effective cleaning, including water
heating, detergent injection, agitation, rinsing and
drying.
Portable Pressure Washer. A self-contained pressure
washer with a spray wand can be an effective cleaning
method, providing it is used with caution. Care must be
taken not to expose collection cell plates to close-up
and prolonged blasts of high temperature or high
pressure water. Cell plates deform under continuous
exposure to such conditions.
OTHER CLEANING CONSIDERATIONS
The previous methods address the cleaning of SMOG-
HOG
®
components only. The cabinetry should also be
periodically cleaned (e.g., during normal planned
maintenance downtimes) to be certain that the
contaminants do not buildup in the unit sumps, thereby
obstructing drains. Each time manual maintenance is
performed, the door feed-through insulators should be
thoroughly cleaned. Voltage output of the power packs
should also be checked when maintenance is
performed.
UAS and/or your local representative can provide
assistance in choosing the best method for cleaning
SMOG-HOG
®
components in your application.
!
C A U T I O N
Never mix acid and alkaline detergents for manual
cleaning. Detergent mixing could cause rapid heat
release, gel formation or other undesirable condition.