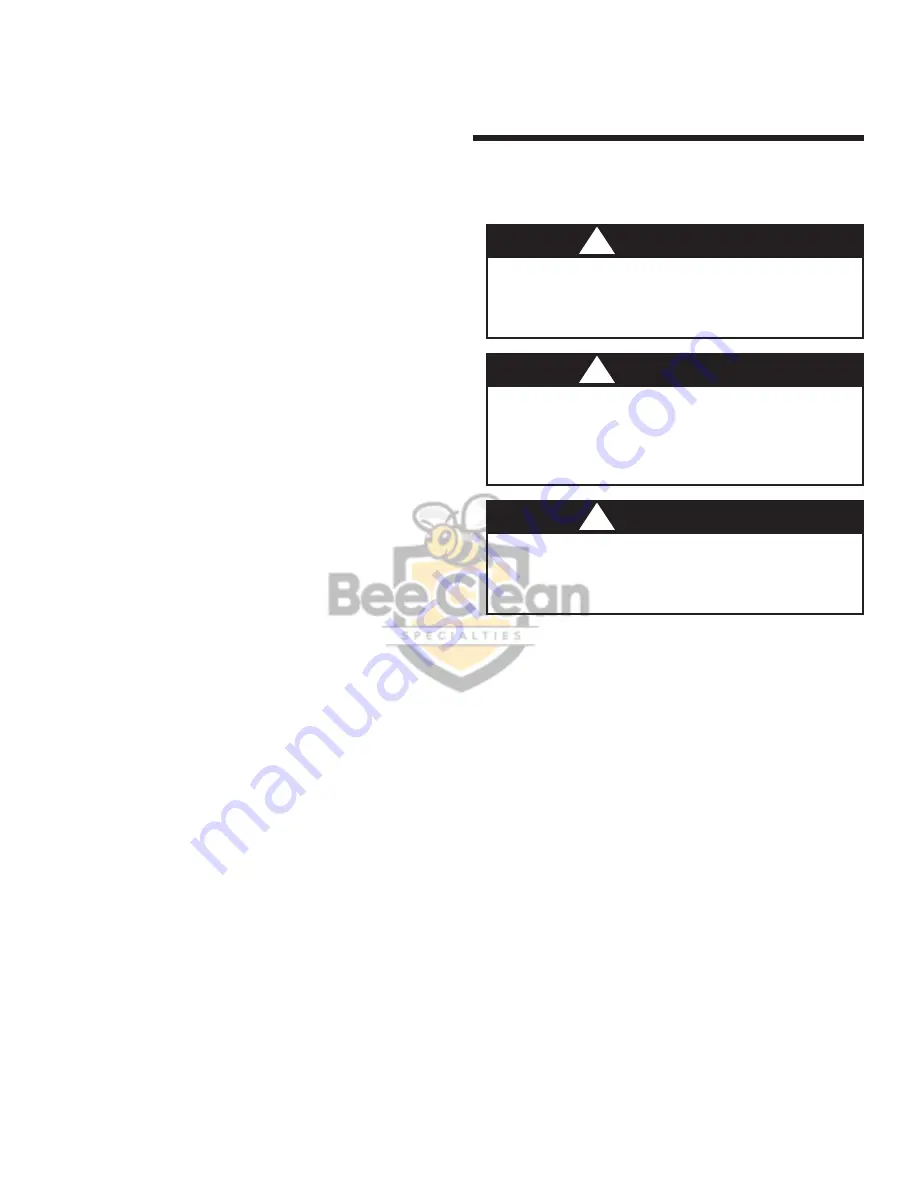
Model SH-PP Owner’s Manual
7
6.4
When Are Components Clean?
After manual cleaning, the ionizers, collector cells and
pre/afterfilters should have a clean, not necessarily
“new,” aluminum appearance. Slight discoloration will not
affect system efficiency. The following is a checklist for
acceptable components:
• Ionizer
1. Aluminum frame and plates are free of contaminant
buildup.
2. Standoff insulators are clean and white (no residual
coating). Cracked or carbon-tracked insulators have
been replaced.
3. Wires and springs are intact and taut, centered
between plates and free of coatings.
4. Contact springs and contact screws are properly
aligned (contact springs not deformed).
5. Bent or broken parts have been repaired or
replaced.
• Collection Cell
1. Aluminum frame is square, plates are parallel and
hot plates are centered between ground plates.
2. Residual particulate has been removed between
plates and at corner supports. Material bridging
across plates has been removed.
3. Triangular insulators are free of contaminant.
Cracked or carbon-tracked triangle insulators have
been replaced.
4. Contact springs and contact screws are properly
aligned (contact springs not deformed).
5. Bent or broken parts have been repaired or
replaced.
• Prefilters/Afterfilters
1. Aluminum media and frame are free of
contaminant.
2. Frame is square and media is intact.
3. Filters are installed with drain holes down and
arrow on their frames pointing in the direction of
airflow.
• Cabinet
1. Door feed-through insulators are clean and white.
2. Door gaskets are clean and intact.
3. Component tracks are free of contaminant (for
component grounding).
4. Module sumps and bottom drains are clear and
free-flowing.
5. Walls, ceiling and doors are free of heavy buildup.
6. Blower has been checked for heavy buildup,
cleaned if required.
7.
TROUBLESHOOTING
THE FOLLOWING SECTIONS ARE FOR THE USE OF
TRAINED PERSONNEL ONLY.
Before proceeding with troubleshooting, check for
proper electrical alignment of contact springs and
contact screws, refer to Figure 10. Improper electrical
alignment and deformed contact springs can cause
arcing, indicator lamp blinking or dead short condition,
indicator lamp not illuminated.
When a SMOG-HOG
®
Air Cleaning System is equipped
with component access doors to each side of the
system, the location arrangement of contact springs and
contact screws will be different from side to side. When
ionizers and collection cells are removed from one side
of the unit, those same ionizers and collections cells
should be installed to that side but not necessarily the
same component access door. If ionizer and collection
cells are switched from side to side, improper electrical
alignment will occur decreasing system efficiency.
7.1
Tools Required
• High voltage probe, 0 to 15 KV, to check high voltage
at power pack and to the ionizer and the collector
cells.
• Volt-ohmmeter, to check 115 VAC input voltage and
continuity.
• Screwdriver, 8" or longer, with insulated handle.
!
C A U T I O N
Hazardous live and moving parts are exposed during
the following procedures. Switch off/isolate the
electrical supply to the SMOG-HOG
®
Air Cleaning
System before servicing.
!
C A U T I O N
Risk of electrical shock. A residual DC voltage will
remain on high voltage components for a short time
after power is removed. Prior to handling, ground
components using an insulated screwdriver, refer to
Figures 2 and 3.
!
C A U T I O N
When the system is operating, 115 VAC is present in
the power pack enclosure at all times. Disconnect the
SH-PP from the power source and lock out before
servicing.