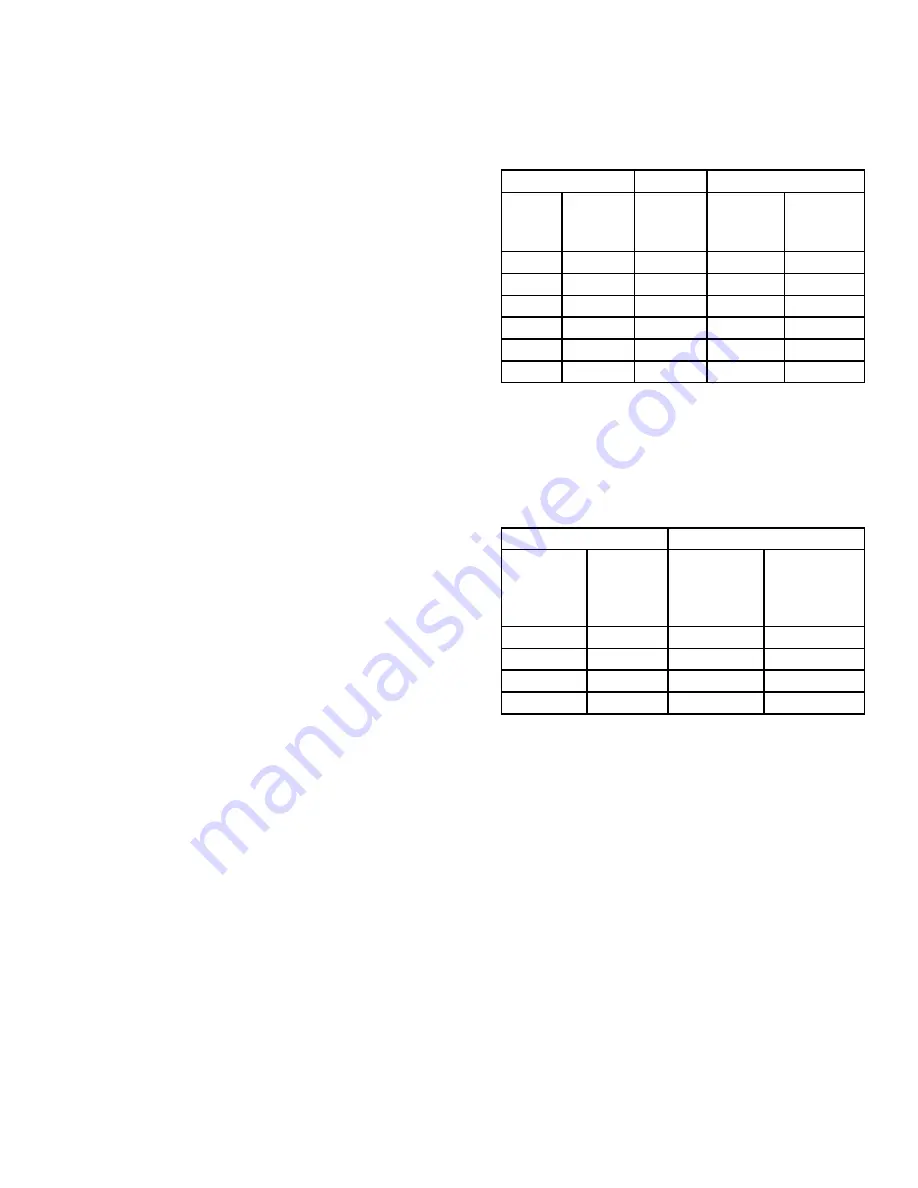
29
VIII. OPERATION (continued)
system circulator. The Priority Time has a factory
setting of “On” and is field adjustable between “On”
and “Off” Refer to Table 8.
7. domestic hot Water (dhW) Terminal Function (
dh_
)
The control allows configuration of the DHW
Circulator output functionality to help the Series 2
integrate into each installation more effectively. The
dhW Circulator output can be connected to a
domestic hot water circulator or a second heating
zone circulator. These applications are selected as
follows:
a. When
dh_
is set equal to domestic hot Water
demand (
h
)
When there is an Indirect Water heater (IWh)
the control provides “dhW” input terminals for
the IWh Aquastat and “dhW Circulator” output
terminals for the dhW Circulator.
When there is a dhW call for heat, the System
Circulator is “forced off”, the dhW Circulator
terminal is energized and the circulator pre-purge
time delay control logic is bypassed to allow the
boiler to fire without delay. When DHW demand
ends the System Circulator “force off” is
removed, the circulator can respond normally,
and the DHW Circulator is de-energized. The
dhW call for heat is detected by a voltage on to
the "dhW" terminal. When the Priority Time
parameter is set to “
off
” the System Circulator
is not forced off for a dhW call for heat. Refer
to Table 8.
b. When
dh_
is set equal to Second heating Zone
(
tt2
)
When there is no IWh the “dhW Circulator”
output may be configured to control a second
heating zone. This is particularly helpful when
the home uses only two heating zones. The
control replaces the need for a two circulator
zone panel. When DHW Terminal Function
(
dh_
) is set to “
tt2
" the control’s two circulator
outputs are used to control two independent
heating zones. Refer to Table 9. A “TT” input
causes a call for heat and energizes the “System
Circulator” output to service heating zone 1 and
a second zone's thermostat wired to the “DHW”
input causes a call for heat and energizes heating
zone 2 circulator wired to the "DHW Circulator"
output.
When there is a Second heating Zone (call for
heat) the boiler is started and the dhW
Circulator terminal is energized. When Second
Heating Zone terminal is de-energized the call
for heat is ended and the dhW Circulator is
de-energized. A Second Heating Zone is detected
by sensing a voltage on the dhW terminal.
Table 8: DHW Terminal Function (
dh_
)
Selection = Domestic Hot Water Demand,
(Parameter dh_ = dh)
Call for Heat
Circulator Status
T-T
Input
DHW
Input
Priority
Time
(
Pt_
)
System
Circulator
Output
DHW
Circulator
Output
on
off
On
on
off
on
on
On
off
on
off
on
On
off
on
on
off
OFF
on
off
on
on
OFF
on
on
off
on
OFF
off
on
Table 9: DHW Terminal Function (
dh_
)
Selection = Second Heating Zone,
(Parameter dh_ = tt2)
Call for Heat
Circulator Status
T-T
Input
DHW
Input
System
Circulator
Output
(Zone 1)
DHW
Circulator
Output
(Zone 2)
off
off
off
off
on
off
on
off
on
on
on
on
off
on
off
on
Summary of Contents for B series 2
Page 19: ...19 Figure 13 Connection Wiring Diagram Intelligent Hydronic Control VI Electrical continued...
Page 20: ...20 Figure 14 Ladder Wiring Diagram Intelligent Hydronic Control VI Electrical continued...
Page 40: ...40 Section Assembly and Canopy Group XI Repair Parts continued...
Page 44: ...44 Manifold and Main Burners 1 Inch Main Burners XI Repair Parts continued...
Page 50: ...50 XI Repair Parts continued Jacket Assembly...
Page 52: ...52 Water Trim XI Repair Parts continued...
Page 59: ...59...
Page 60: ...60 U S Boiler Company Inc P O Box 3020 Lancaster PA 17604 1 888 432 8887 www usboiler net...