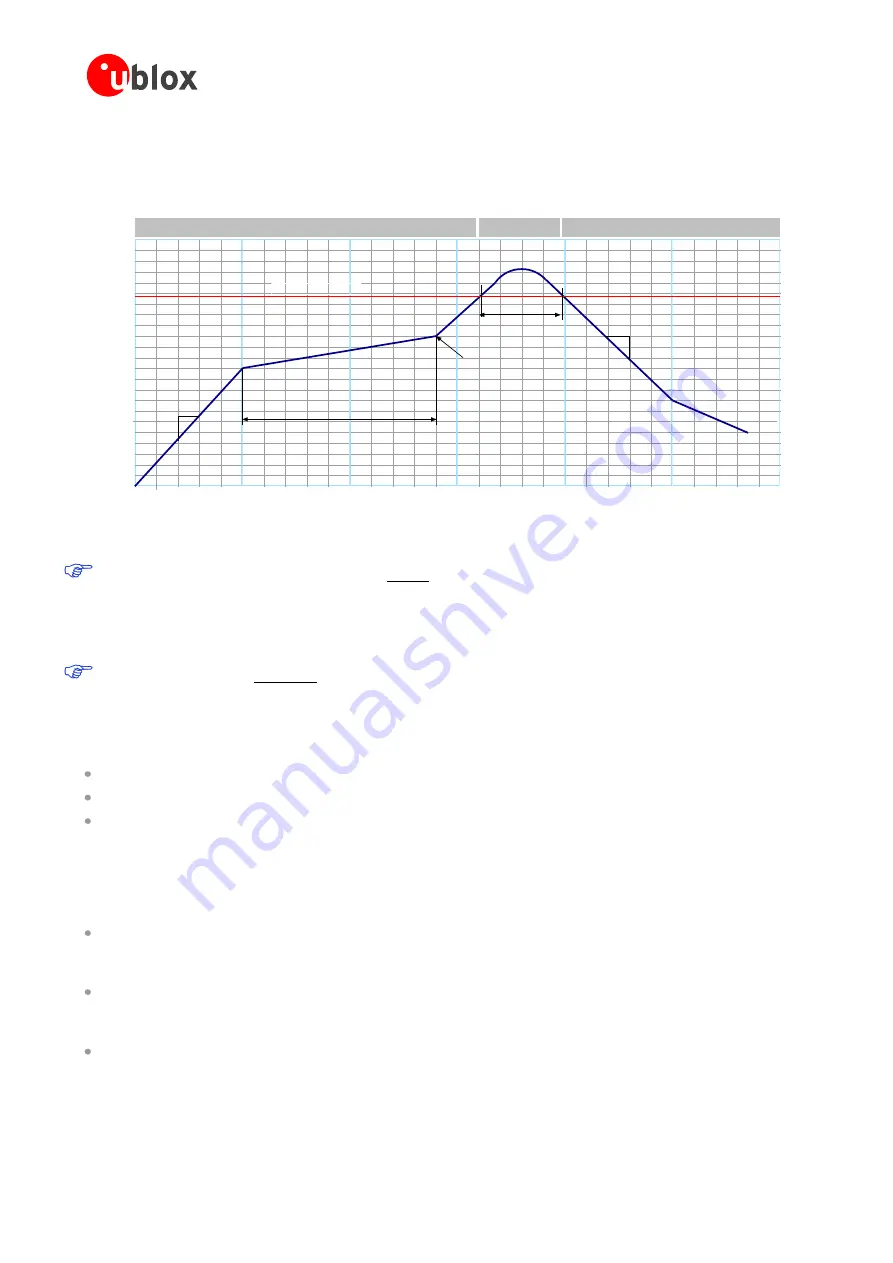
LEA-5, NEO-5, TIM-5H - Hardware Integration Manual
GPS.G5-MS5-09027-A2
Released
Handling and soldering
Page 53 of 68
The final soldering temperature chosen at the factory depends on additional external factors like choice of
soldering paste, size, thickness and properties of the base board, etc. Exceeding the maximum soldering
temperature in the recommended soldering profile may permanently damage the module.
Preheat
0
50
100
150
200
250
300
50
100
150
200
250
Heating
Cooling
50
100
150
200
250
max 1- 4 °C/s
max 60 - 120 s
Peak Temp.
230 - 250 °C
Liquidus Temperature
216 - 221
[°C]
Elapsed Time [s]
max 20 - 40 s
Typical Leadfree
Soldering Profile
End Temp.
150 - 200 °C
max 3 °C/s
[°C]
Figure 45: Recommended soldering profile
When soldering u-blox 5 modules in a leaded process, check the following temperatures:
o
PB- Technology Soaktime:
40-80sec
o
Time above Liquidus:
40-90 sec
o
Peak temperature:
225-235 °C
u-blox 5 modules
must not
be soldered with a damp heat process.
3.3.3
Optical inspection
After soldering the u-blox 5 module, consider an optical inspection step to check whether:
The module is properly aligned and centered over the pads
All pads are properly soldered
No excess solder has created contacts to neighboring pads, or possibly to pad stacks and vias nearby.
3.3.4
Cleaning
In general, cleaning the populated modules is strongly discouraged. Residues underneath the modules cannot be
easily removed with a washing process.
Cleaning with water will lead to capillary effects where water is absorbed in the gap between the baseboard
and the module. The combination of residues of soldering flux and encapsulated water leads to short
circuits or resistor-like interconnections between neighboring pads.
Cleaning with alcohol or other organic solvents can result in soldering flux residues flooding into the two
housings, areas that are not accessible for post-wash inspections. The solvent will also damage the sticker
and the ink-jet printed text.
Ultrasonic cleaning will permanently damage the module, in particular the quartz oscillators.
The best approach is to use a "n“ clean" ”oldering paste and eliminate the cleaning step after the soldering.