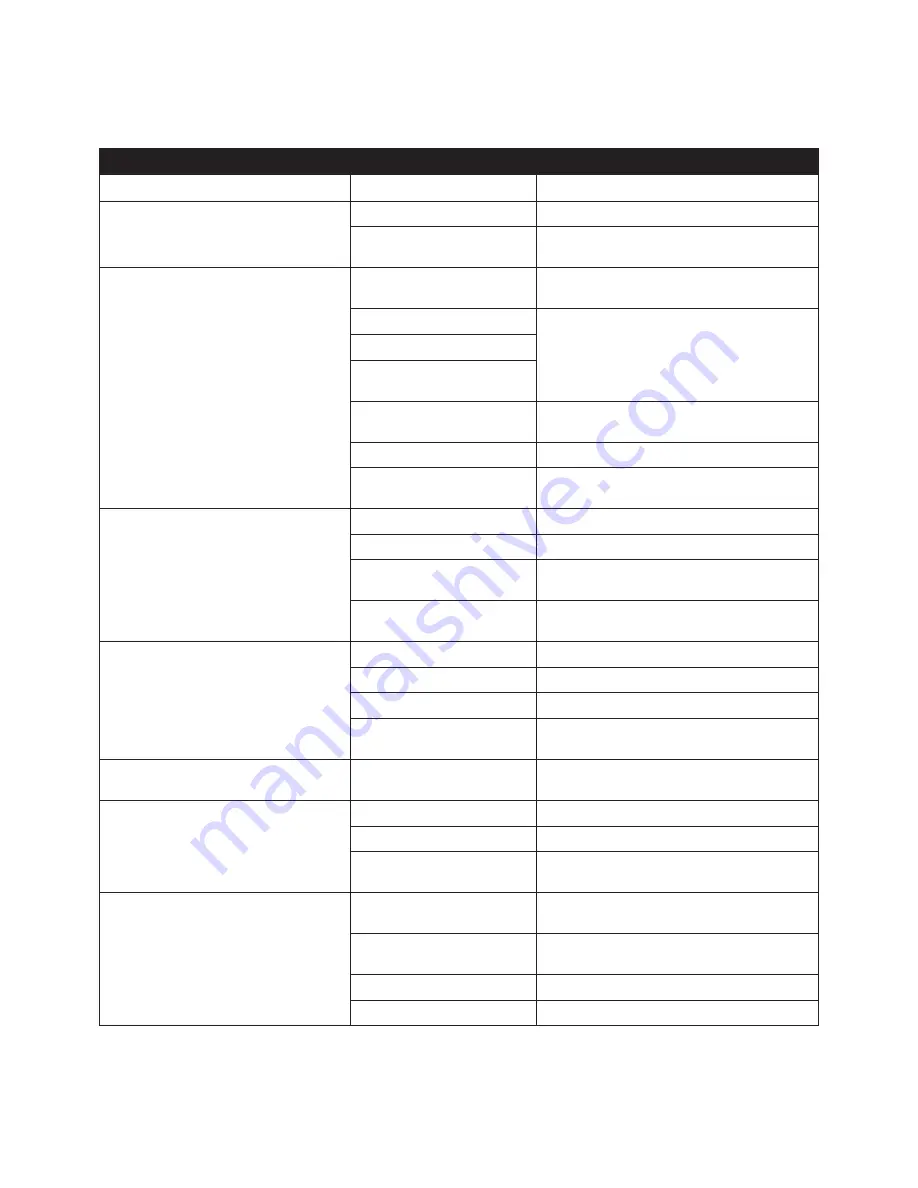
TYROLIT
Hydrostress AG
Page 21
Ring saw HRH500
Faults
8
Faults
Fault
Possible cause
Solution
Ring saw does not start
Drive unit switched off
X
Switch on drive unit.
Emergency STOP on drive unit
pressed
X
Re-set emergency STOP.
Cutting ring does not rotate
Cutting ring not located cor-
rectly on the profiled drive roller
X
Mount the cutting ring correctly.
Incorrect hose connection
X
Check hydraulic system.
Hydraulic motor fault
Oil delivery not connected
properly
Main drive unit motor not
switched on
X
Switch on main motor.
Drive rollers dirty
X
Clean drive rollers.
Roller pre-tension device not
engaged
X
Check roller pre-tension device.
Cutting ring revolves too slowly
Drive rollers worn
X
Change drive rollers.
Roller bearing defective
X
Change roller bearing.
Inadequate oil flow and pres-
sure
X
Check drive unit.
Roller pre-tension device not
engaged
X
Check roller pre-tension device.
Cutting ring disengages
Roller distance too large
X
Check roller pre-tension device.
Drive rollers worn
X
Change drive rollers.
Cutting ring damaged
X
Change cutting ring.
Roller pre-tension device not
engaged
X
Check roller pre-tension device.
Cutting ring twisted
Cutting ring inadequately
cooled
X
Check water cooling.
X
Change cutting ring.
Diamond segments broken off
Cutting ring twisted
X
Change cutting ring.
Hard resistance in work piece
X
Change cutting ring.
Brazing or welding of segments
not professional standard
X
Change cutting ring.
Motor seal split
Ring saw runs backwards
X
Check hydraulic connections and drive unit oil
circuit.
Pressure too high
X
Check setting at drive unit. If necessary, install
a pressure reducing valve and a flow divider.
Defective seal
X
Replace seal.
Oil return incorrectly connected
X
Check connector.