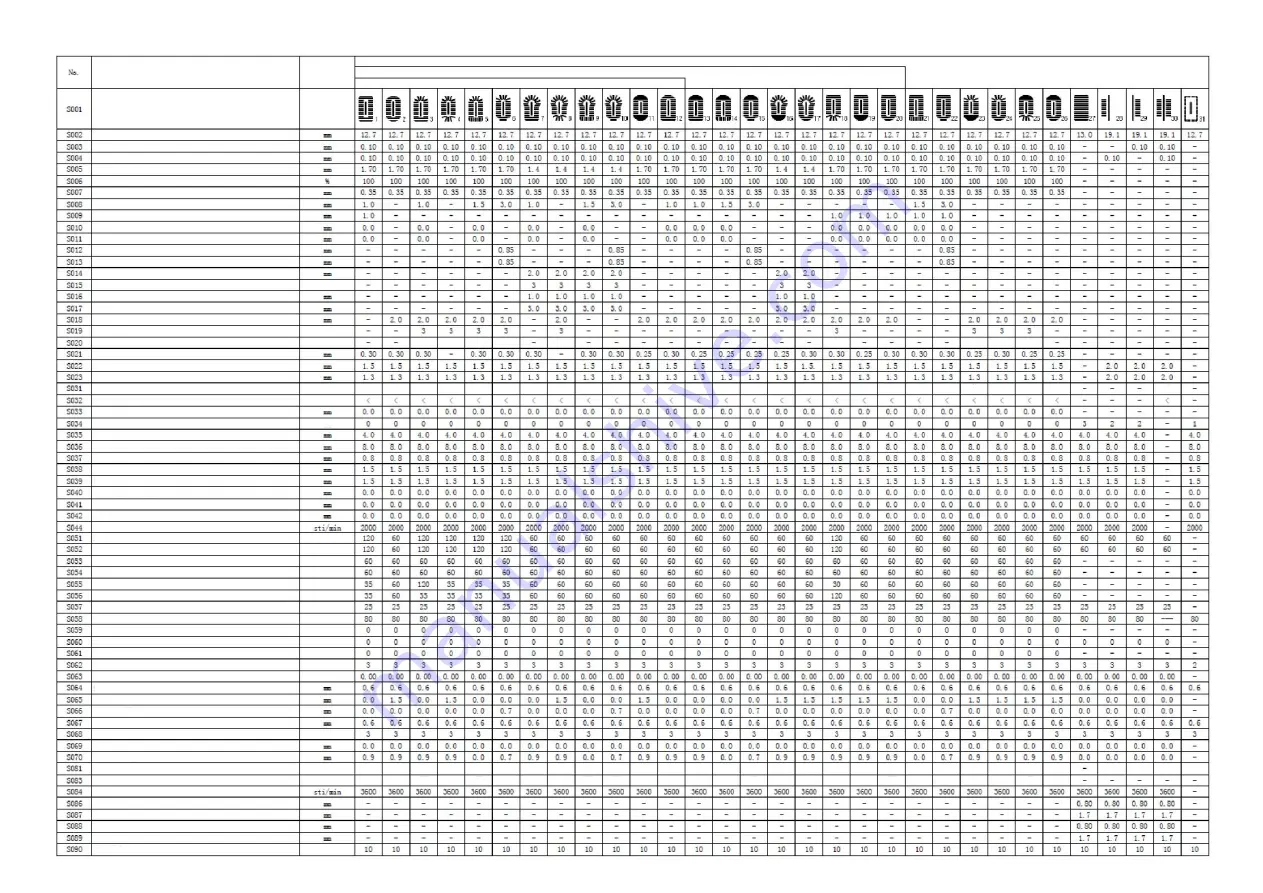
- 81 -
X. Table of Initial Value Data for Each Shape
Item
Unit
Shape selection level 3 (31 shapes)
Shape selection level 2 (20 shapes)
Shape selection level 1 (12 shapes)
Sewing shape
Cloth cutting length
Right knife groove width
Left knife groove width
Left overedging width
Ratio of right and left shapes (compared with that of left sides)
Pitch at parallel section
2
nd
bar-tacking length
1
st
bar-tacking length
Right bar-tacking width compensation
Left bar-tacking width compensation
Left taper bar-tacking offset
Right taper bar-tacking offset
Eyelet length
Number of stitches of eyelet shape
Stitch
Eyelet width
Eyelet length
Round-type shape length
Number of stitches of radial shape
Stitch
Reinforcement of radial shape (yes/no)
No
No
No
No
No
No
No
No
No
Pitch at bar-tacking section
1
st
clearance
2
nd
clearance
Single/double stitching
Single Single Single Single Single Single Single Single Single Single Single Single Single Single Single Single Single Single Single Single Single Single Single Single Single Single
Single
Double stitching cross selection
Double stitching width compensation
Number of basting times
TIMES
Basting speed
Rolling length of basting
Rolling pitch of basting
Rolling width of basting
Lengthwise compensation of needle entry of basting
Crosswise compensation of needle entry of basting
Compensation of left side position of basting
Compensation of right side position of basting
Setting basting speed
Left parallel section tension
Right parallel section tension
Left parallel section tension (1
st
cycle of double stitching)
Right parallel section tension (1
st
cycle of double stitching)
1
st
bar-tacking section tension
2
nd
bar-tacking section tension
Setting of needle thread tension at the start of sewing
Basting thread tension setting
ACT timing adjustment at the start of 1
st
bar-tacking
Stitch
ACT timing adjustment at the start of right overedging
Stitch
ACT timing adjustment at the start of 2
nd
bar-tacking
Stitch
Number of stitches for bar-tacking at the start of sewing
Stitch
Sewing pitch for bar-tacking at the start of sewing
Width at the start of sewing
Lengthwise compensation of bar-tacking at the start of sewing
Crosswise compensation of bar-tacking at the start of sewing
Bar-tacking width at the end of sewing
Number of stitches of bar-tacking at the end of sewing
Stitch
Lengthwise compensation of bar-tacking at the end of sewing
Crosswise compensation of bar-tacking at the end of sewing
Knife motion (yes/no)
Yes
Yes
Yes
Yes
Yes
Yes
Yes
Yes
Yes
Yes
Yes
Yes
Yes
Yes
Yes
Yes
Yes
Yes
Yes
Yes
Yes
Yes
Yes
Yes
Yes
Yes
Yes
Yes
Yes
Yes
Knife motion at 1
st
cycle of double stitching (yes/no)
No
No
No
No
No
No
No
No
No
No
No
No
No
No
No
No
No
No
No
No
No
No
No
No
No
No
Maximum speed limitation
Forward pitch
Forward width
Returning pitch
Returning width
Presser foot pressure
Summary of Contents for GT1790A
Page 1: ...GT1790A COMPUTER CONTROLLED HIGH SPEED LOCKSTITCH BUTTONHOLING MACHINE INSTRUCTION BOOK...
Page 5: ...2 2 List of standard sewing shapes...
Page 6: ...3 3 Structure...
Page 15: ...12...
Page 21: ...18...
Page 23: ...20 V Operation of the Sewing Machine 1 Description operation panel switch...