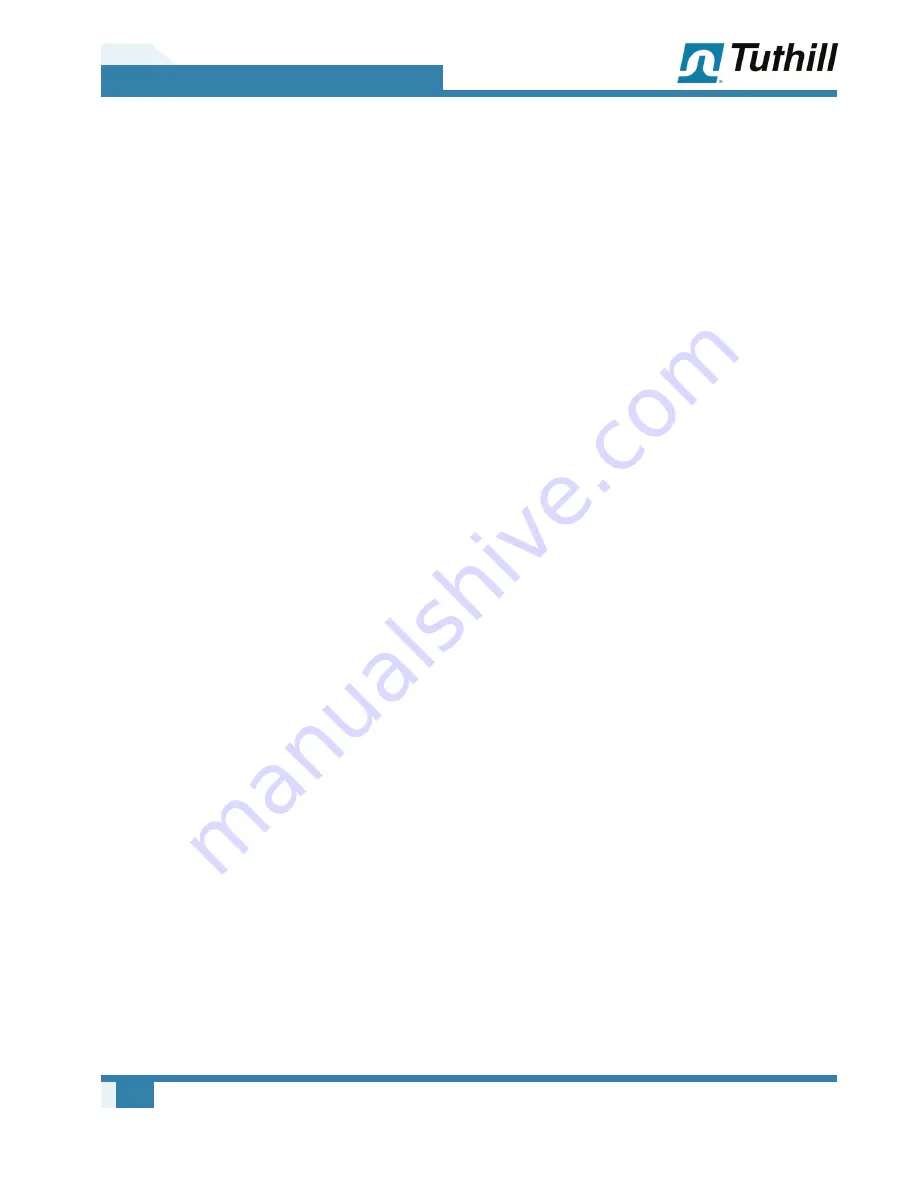
18
05
Purges
Manual 1861 Rev C p/n 001861 0000
STEAM FLUSHING
If there is a substantial amount of the residual
process material build-up within the pump, clean
out the pump interior. Steam flushing is one way
to clean the residual process material build-up
from the pump interior. When there is enough
residual process material build-up, make sure
that the pump is not forced to rotate by the motor.
Especially for the processes that have a high
potential for build-up and are aggressive in nature,
such as processes with oligomer, monomer,
polymer, resin, etc., regularly clean out the pump
interior by steam flushing.
Steam pressure: Approximately 14.22 psig
(1 kg/cm
2
g)
1. System Isolation: Disconnect all electrical and
control power, and place lockout tags on the
motor control center (MCC) and/or control
panel to ensure nobody accidentally starts the
pump during the steam flushing. The process
isolation valve should be closed. The discharge
valve (if equipped) and silencer drain valve
should be open.
2. Inject steam for 10 to 20 minutes through the
pump’s process inlet (suction) nozzle or one of
the nozzles at the side of the pump’s process
inlet (suction) nozzle.
OTE:
N
The steam injection time can be varied
based on the types and amounts of
residual process material built up within
the pump.
3. Rotate the pump shaft by hand to check
whether the pump rotates smoothly.
OTE:
N
During this time, be careful not to start the
motor and to observe all lockout/tagout
procedures.
4. If the pump rotates smoothly by hand rotation,
stop the steam injection and start the pump
motor with the process isolation valve closed.
5. If the pump does not rotate smoothly by hand
rotation, repeat steps 2 and 3 until the pump
rotates smoothly by hand. Depending on the
severity of the residual process material build-
up, it may be necessary to repeat steps 2 and
3 several times.