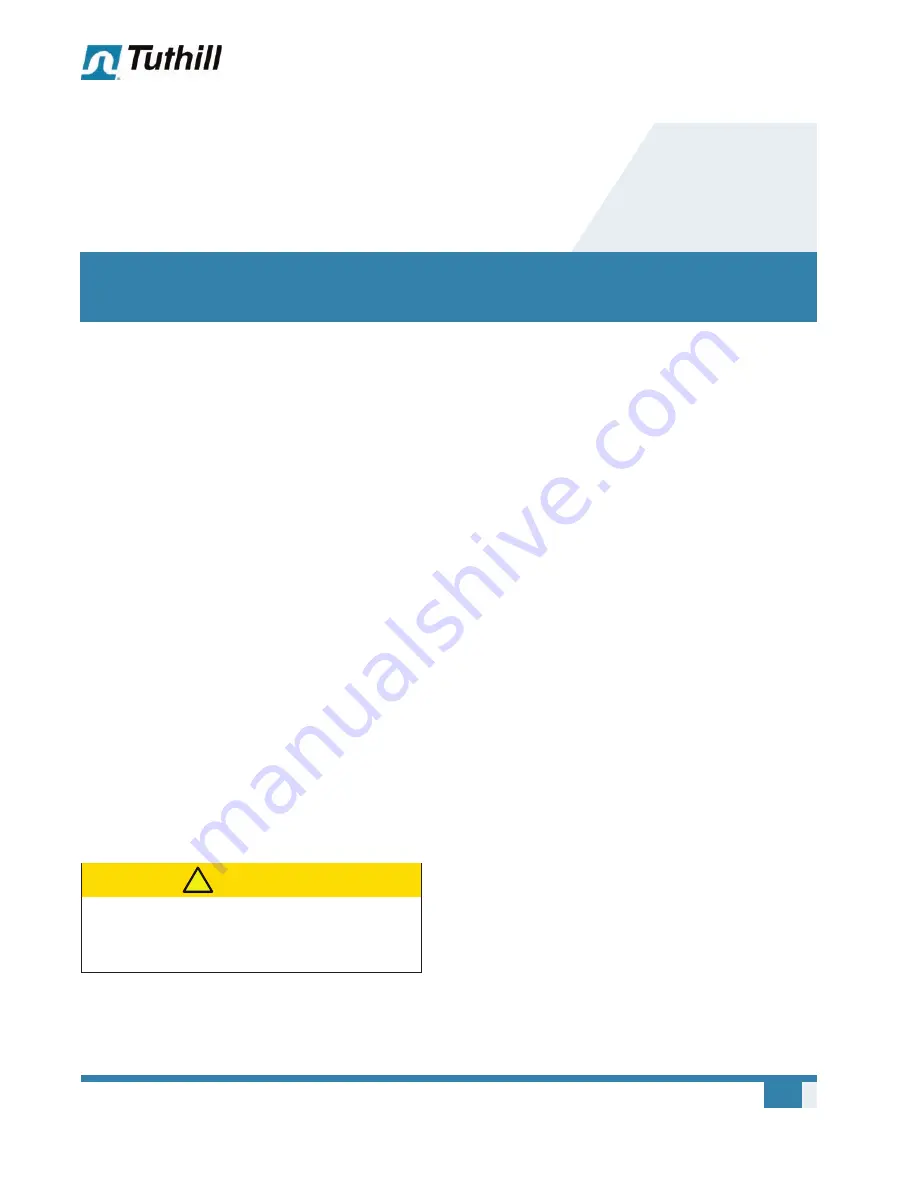
Operator’s Manual
1808
022016 ENG
1
CONGRATULATIONS
on the purchase of a new
KINNEY
®
KD
Single-Stage, Duplex Rotary Piston
Vacuum Pump from Tuthill Vacuum & Blower
Systems. Please examine the pump for shipping
damage, and if any damage is found, report it
immediately to the carrier. If the pump is to be
installed at a later date, make sure it is stored in a
clean, dry location and rotated regularly. Make sure
covers are kept on all openings. If pump is stored
outdoors, be sure to protect it from weather and
corrosion.
This manual applies to Kinney Vacuum models
KD-30 and KD-50. Be thoroughly familiar with
these instructions before attempting to install,
operate, or repair this unit. Consult Tuthill Vacuum
& Blower Systems when problems arise that
cannot be resolved after reading this manual.
Always include pump nameplate information when
ordering parts or components.
KINNEY KD
vacuum pumps are built to exacting
standards and, if properly installed and maintained,
will provide many years of reliable service. Read
and follow every step of these instructions when
installing and maintaining the pump.
CAUTION
!
Read manual before operation or bodily harm
may result. Attention should be given to the
safety related sections of this manual.
OTE:
N
Record the pump model and serial
numbers of the machine in the
OPERATING DATA FORM on the inside
back cover of this manual. Use this
identifi cation on any replacement part
orders, or if service or application
assistance is required.
APPLICABLE DOCUMENTATION
The applicable documents associated with this
manual are:
• EN 1012-1:1996 - Compressors and vacuum
pumps - Safety Requirements - Part 2: Vacuum
Pumps
SCOPE OF MANUAL
The scope of this manual includes the following
components as offered by Tuthill Vacuum & Blower
Systems: Rotary Piston Pump.
INTRODUCTION
01
Summary of Contents for KINNEY KD Series
Page 39: ......