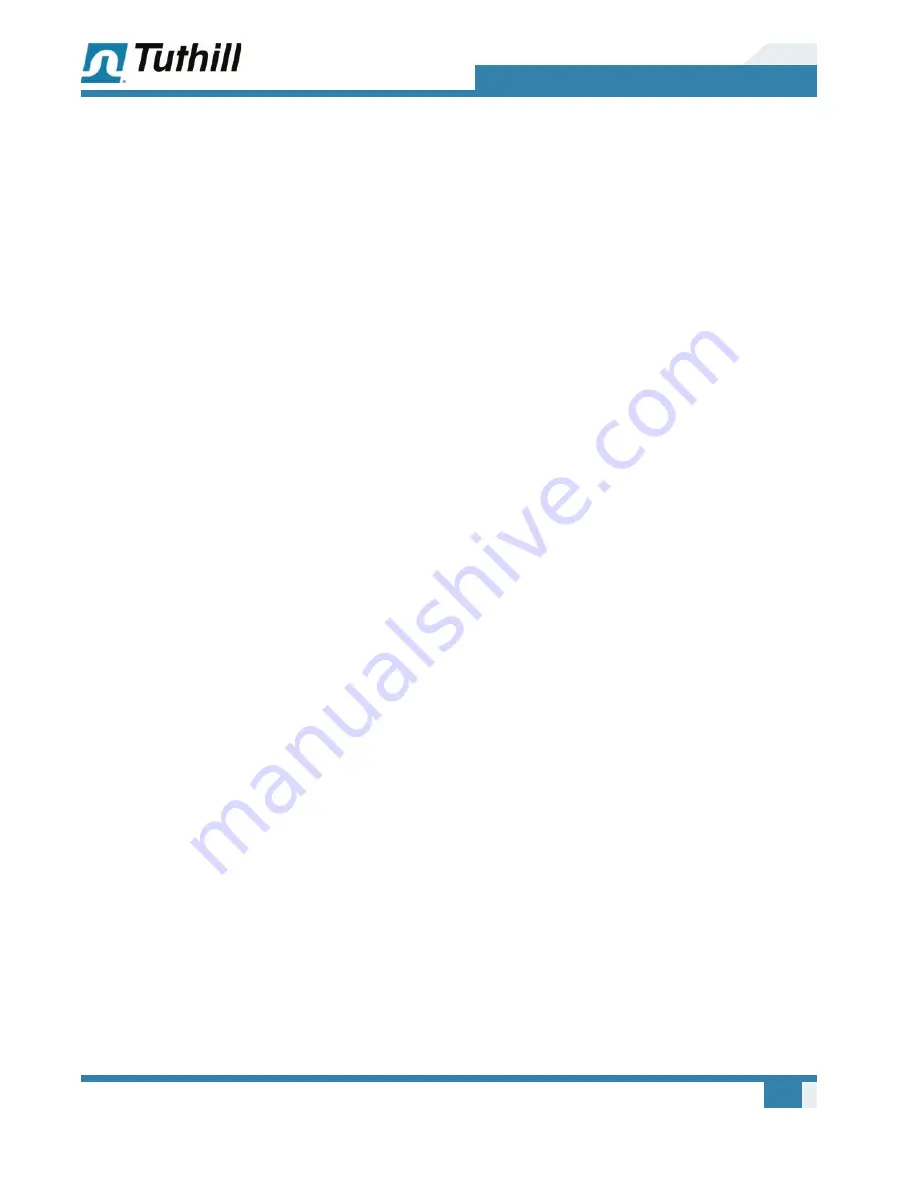
Operator’s Manual
1808
022016 ENG
13
06
Operation
The oil level will change with the pumping
pressure. When the pump is fi rst started, the oil will
rise. As the inlet pressure is reduced, the oil level
will drop and should stabilize midway on the sight
gauge when the pump pressure approximates
blank-off.
STOPPING
1.
If a vacuum valve is provided between the
pump and the process equipment, place this
valve in the CLOSED position.
2.
Turn off the power to the pump motor, and
vent
the pump to atmosphere. The gas ballast
valve
can be used for this purpose if a vent
valve has
not been provided. Venting the pump
prevents
fl ooding, which makes starting the
pump diffi
cult
.
Do not
use the gas ballast valve for
venting connected
(process) volumes. Use the
gas ballast valve
only for venting the pump
casing and a short
length of manifold.
GAS BALLAST
Gas ballast is an operating mechanism that is used
to prevent the condensation of vapor in a vacuum
pump. Vapor present in the gas being pumped can
condense during the vacuum pump compression
cycle and mix with the oil. As the oil is circulated
through the pump, the condensate is carried
with the oil and allowed to re-evaporate, causing
poor pump performance and making frequent oil
changes necessary. By using gas ballast, most
vapors can be passed through a vacuum pump
without condensing and then discharged with
the pump exhaust. Unless the lowest possible
pressure is necessary, operate the pump with gas
ballast.
In addition to preventing vapor condensation,
the use of gas ballast also reduces discharge
valve noise to a low level. It is generally possible
to eliminate valve noise with a small gas ballast
fl ow that does not seriously increase the ultimate
pressure. If the resulting pressure is tolerable, this
method of operation is preferred since it also helps
to keep the oil clean. The setting of the gas ballast
valve is best determined by trial and error because
the amount of condensable vapor as well as the
system operating conditions vary with different
processes. The motor power consumption and
the ultimate pressure will rise in proportion to the
increase in gas ballast fl ow.
Gas ballast can be used in the following two ways:
1.
Continuous gas ballast can be regulated
to fl ow into the pump while processing. To
regulate the gas ballast valve, while dead
ended, slowly open the valve until the pressure
is slightly below that needed for process work.
Operate the pump at this setting to keep oil
contamination to a minimum.
2.
Intermittent gas ballast can be used when
pressure requirements do not permit the use
of continuous gas ballast. Running the pump
overnight with full gas ballast is recommended
for cleaning the oil of contamination. The
condition of the oil can be estimated by
observing the pump blank-off pressure with
the gas ballast valve closed. Run the pump
with the gas ballast valve open for a timed
period (15 to 20 minutes) and observe the
blank-off pressure change. When there is no
further change in pressure, the oil is clean.
This pressure change vs. time can be used to
estimate the required time to clean the oil.
Summary of Contents for KINNEY KD Series
Page 39: ......