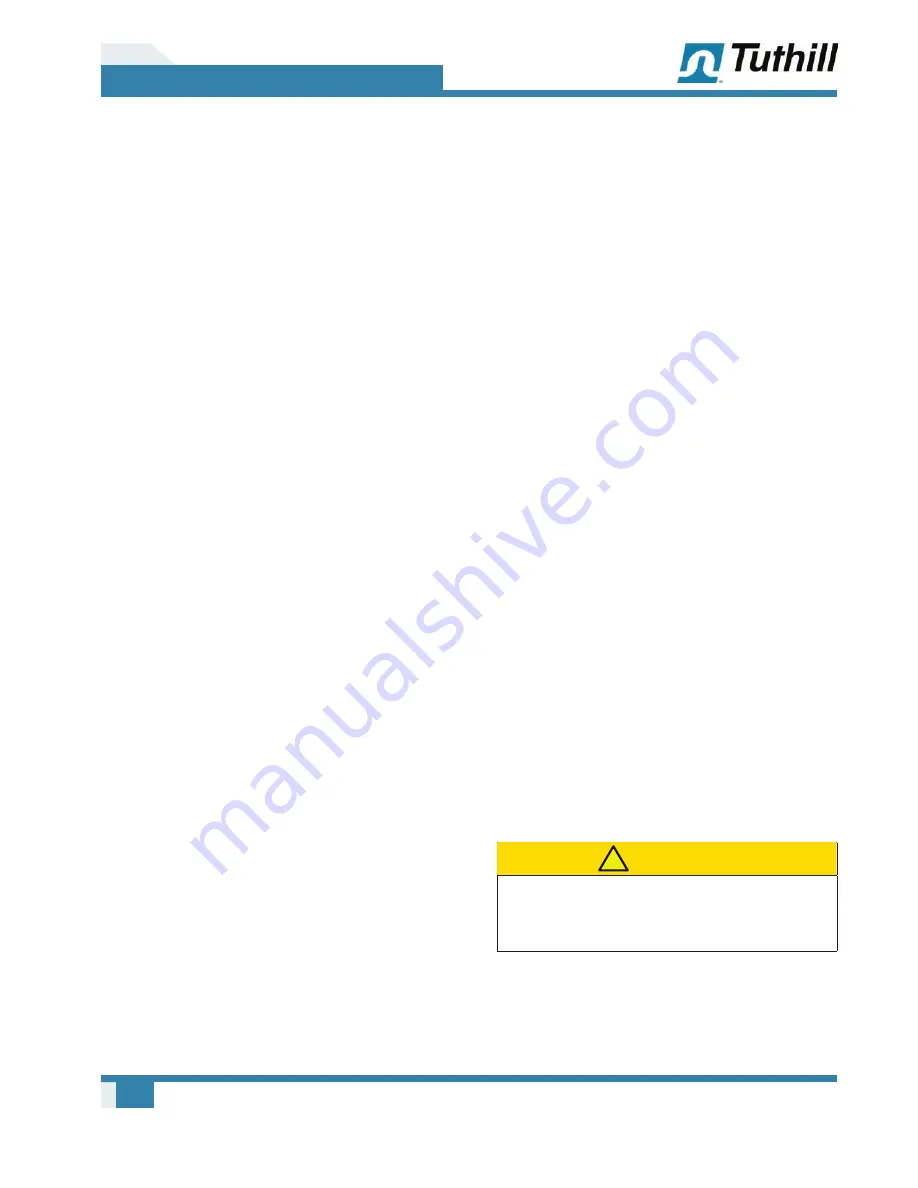
20
09
Troubleshooting
Operator’s Manual
1808
022016 ENG
PUMP LEAKS
If the pump is suspected of leaking after
eliminating oil contamination as the cause of poor
performance, use a plastic sealing compound such
as Apie on to seal suspected areas. Apply the
compound while the pump is running and monitor
the gauge for sudden pressure drop as the leaks
are sealed temporarily. Carefully check around
the head for cylinder joints, securing bolts, plugs,
or any penetration into the pumping area. Loctite
is available from Tuthill acuum lower to
permanently seal the leaks once they have been
found. If leaks are still indicated, check the shaft
seal for defects such as cracked carbon ring,
hardened rubber components, or scratches on the
face of the seat, and change the seal if it shows
signs of being defective.
Process Leaks
f the blank-off test shows that the vacuum pump is
functioning properly but that the process equipment
is faulty, applying the following procedure to further
isolate the trouble:
1.
Attach a vacuum gauge on the process side of
the isolation valve.
2.
Clear the process chamber of all material,
which could give off vapors that would change
the reading.
3.
Run the pump to obtain the lowest possible
pressure, and close the isolation valve.
4.
Observe the pressure and if pressure is
greater than required or does not hold to a
reasonable rise rate, fi nd and seal the leaks.
f a leak detector is not available, proceed as
directed in
L eak C h ec k ing Tec h niq ues on
page 20
and permanently repair the leaks
found.
Leak Checking Techniques
f a leak detector is available, probe all areas
of penetration into the pumping chamber while
monitoring the gauge for pressure changes. If a
leak detector is not available, use the following
method to locate leaks:
1.
over suspected leaks with a low vapor
pressure sealing compound.
2.
Detect large leaks by pressuri ing the pump
and painting with a soap solution. ubbles will
indicate leaks. hen pressuri ing the pump,
keep the pressure low (1 to 2 PSIG) for easy
detection of bubbles.
3.
To locate small leaks, it may be necessary to
use a fast-acting thermocouple or thermistor
gauge in conjunction with a probing media
such as acetone, alcohol, freon, or helium.
Position the vacuum gauge head downstream
from the suspected leak area, and reduce the
pressure until the gauge registers. Apply the
probing media using a brush or squirt gun
and watch the gauge for sudden pressure
rise or fall as the media comes in contact with
the leak area. Seal the area temporarily with
Ductseal, octite
, or lyptal, and continue
probing until the desired pressure is obtained.
Permanently repair the leak areas with Loctite
.
4.
If leak checking fails to disclose the leaks,
disassemble and remake all demountable
joints and connections using new gaskets
and sealing compound such as octite
.
Re-check pressure using blank-off plate after
addition of each segment of the vacuum
manifolding.
CAUTION
!
Compound applied too thick may be
sq ueeze d into the pump where it could cause
damage.
Summary of Contents for KINNEY KD Series
Page 39: ......