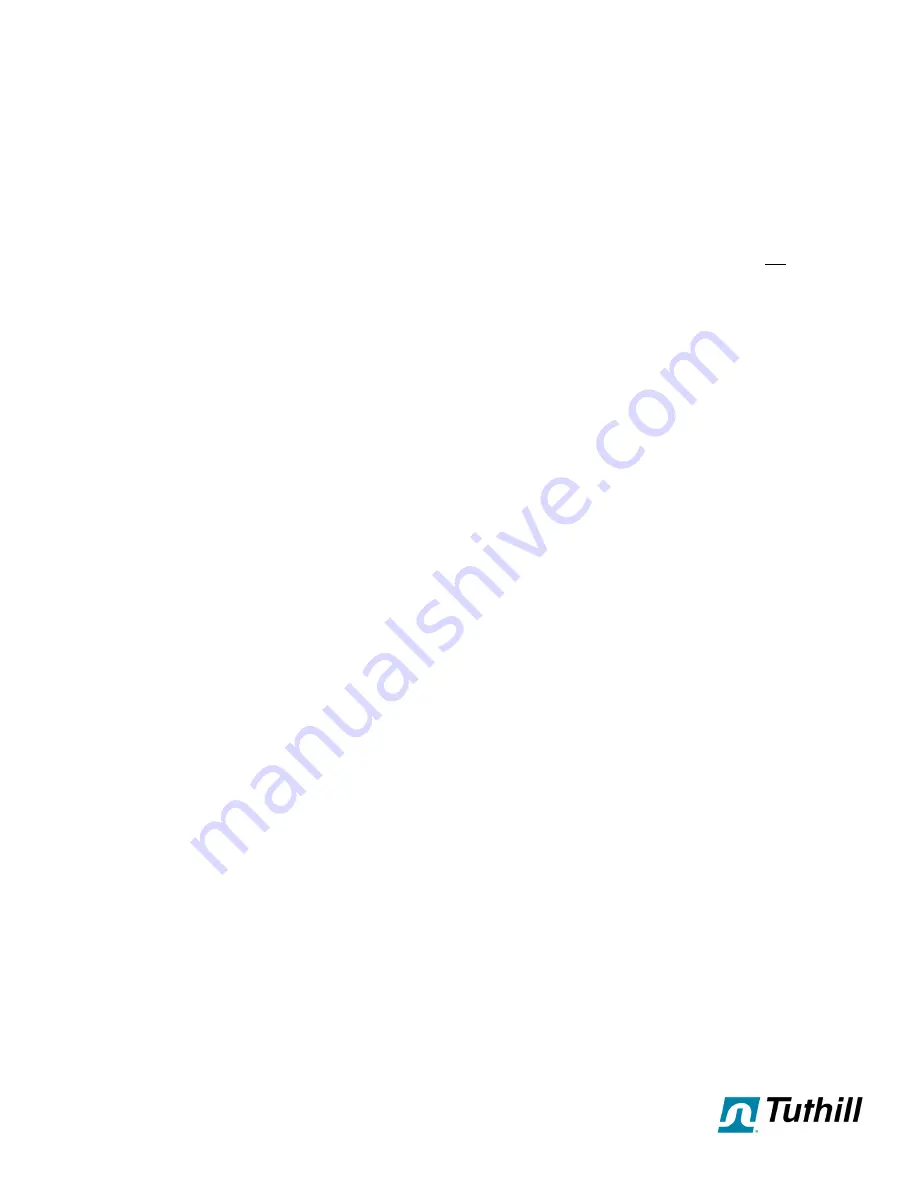
4
The flow meter must be installed in the system free of pipe stress. Pipe stress can deform the flow meter chamber,
resulting in loss of accuracy. TN Series meters should be secured to a mounting support. Never use the piping as the
sole source of support.
Apply pipe compound to the male threads.
Do NOT use PTFE sealing tape.
Flush the system
prior to installation of the flow meter.
Start-Up & Operation
SLOWLY
fill the system with liquid, to avoid operation on air or vapors. Do
NOT
pump at full capacity until
all
air has
been purged. We recommend that:
▪
Throttle the valve on flow meter inlet side, and allow the system to fill slowly by gravity.
▪
Open the outlet valve. Start the pump, and then slowly open the inlet valve. In this manner slowly fill the flow
meter before fully operating the inlet and outlet valves.
The flow meter is not designed to operate on air, but the design and materials of construction allow for operation on vapor
for short periods of time, without damage to flow meter internals. Overspeeding and operation with 'water hammer'
conditions are likely to cause damage to the flow meter.
Flow Meter Calibration
● Fill-Rite Meters are calibrated prior to shipment. TN Series meters are calibrated for viscosity of a specific liquid, but
we recommend flow meters be recalibrated after installation. Please see procedure outlined below.
● There are no fixed rules for frequency of re-calibration. Flow meter wear is a function of flow rate vs. model size, total
volume metered, liquid lubricity and liquid viscosity. An annual re-calibration is often suggested, but from 6 to 36
months could be correct.
● Maintain records of re-calibration data. By tracking degree of change in each re-calibration, you can monitor when the
flow meter should be serviced with a new measuring chamber (when degree of change increases significantly).
● When re-calibrating, we recommend testing the flow meter on the normal fluid of operation. If system flow rate is
constant, you can test at this flow rate only. If system flow rate fluctuates, you should test at high, intermediate and
low flow rates.
Mechanical Register:
1. You can test against a prover, a master meter or a scale. To test against a scale, select a calibration vessel with
capacity equal to at least 60 seconds of flow.
Short run tests are not acceptable for re-calibration purposes.
2. Run 3 tests at each flow rate, and use the average value to calculate flow meter error (see below).
The calibration screw has approx. 6% range (+/-3%). If meter error exceeds 3%, a gear change is necessary.
● If the register is showing
too little
, turn the calibration screw to the
right.
● If the register is showing
too much
, turn the calibration screw to the
left
.
3. Run 1-2 more tests to confirm that the flow meter is now in calibration.
4. Record % correction in flow meter file, and return the flow meter to service.
Calculating meter error:
Test 3 times, so any test with operator error will stand out. Reject such results, and use the average of the remaining
results for calculation purposes.
Shutdown Instructions
If the meter is to be shut down for an extended period of time, it is recommended that the measuring chamber of the
meter be thoroughly flushed out to prevent the settling out of un-dissolved chemicals or the accumulation of corrosive
deposits.
Maintenance
Installation (cont’d)
Preventative Maintenance
Preventative maintenance consists of periodic inspection and cleaning procedures. The procedures should be
performed at regular intervals and any defects discovered should be corrected before further
operation of the flow meter.
mdi - Manufacturers Distributor Inc. | Phone: (813) 241 - 4900 | Fax: (813) 571 - 0422 | www.FillRitePumpSales.com | [email protected]