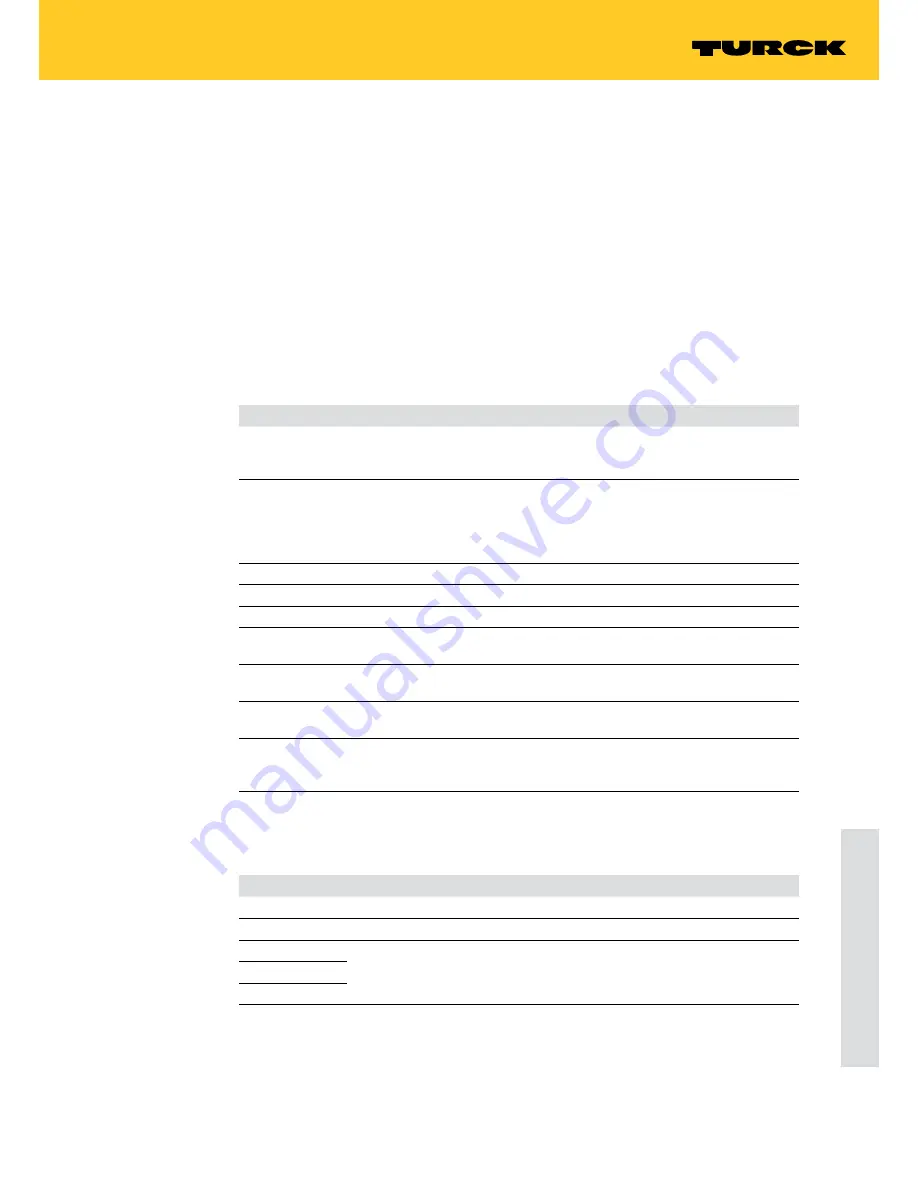
25
2016/08
upr
ox® S
ensors with IO
-Link I
nt
er
fac
e
9.1.1
IO-Link parameters
Different parameter settings for the particular application are made via the IO-Link interface.
For further information on the functions and IO-Link parameters see chapter 4.4.1 and the IO-
Link parameter manual of the device.
9.1.2
Parameter transfer with IO-Link call function block
Due to the range of functions available with the devices, the parameter subindexes described
in the IO-Link parameter manual cannot be addressed with an IO-Link call function block com-
pliant with the IO-Link specification. To transfer parameters the entire data string of the param-
eter index must be transferred in binary format from the controller to the device. The subindex
“0” referring to the entire string must be set in the IO-Link call function block. A separation of
subindexes is not possible.
9.1.3
Process data
Bit
Function
Meaning/bit information
0
Output 1
0: Output 1 not actuated
1: Output 1 switches (depending on the sensor function
and the output configuration)
1
Output 2
0: Output 2 not actuated
1: Output 2 switches (depending on the sensor function
and the output configuration)
1: Output 2 is not set as a temperature indicator (“One
switch point” sensor function)
2
Switch point 2
0
3-bit coding for the set switching distance (3rd bit)
3
Switch point 2
1
3-bit coding for the set switching distance (2nd bit)
4
Switch point 2
2
3-bit coding for the set switching distance (1st bit)
5
Start delay
1: Start delay switched on and activated after a voltage
reset (for “Rotational speed monitor” sensor function)
6
Undertemperature
1: Temperature indicator detects value below the set tem-
perature limits
7
Overtemperature
1: Temperature indicator detects value above the set tem-
perature limits
8…15
Application specific marking
A 32 byte memory is provided for application specific
marking. The first byte of the memory is transferred cycli-
cally to the controller.
If the sensor is actuated, bits 0…4 show the switching state according to the actual settings.
Example: “One switch point” sensor function, 100% switching distance, output 2 not set as a
temperature indicator.
Bit
State
Meaning
0
1
Output 1 switches
1
1
Output 2 is not set as a temperature indicator
2
1
3-bit coding for the set switching distance (100%), see chap. 4.4.1
3
0
4
0