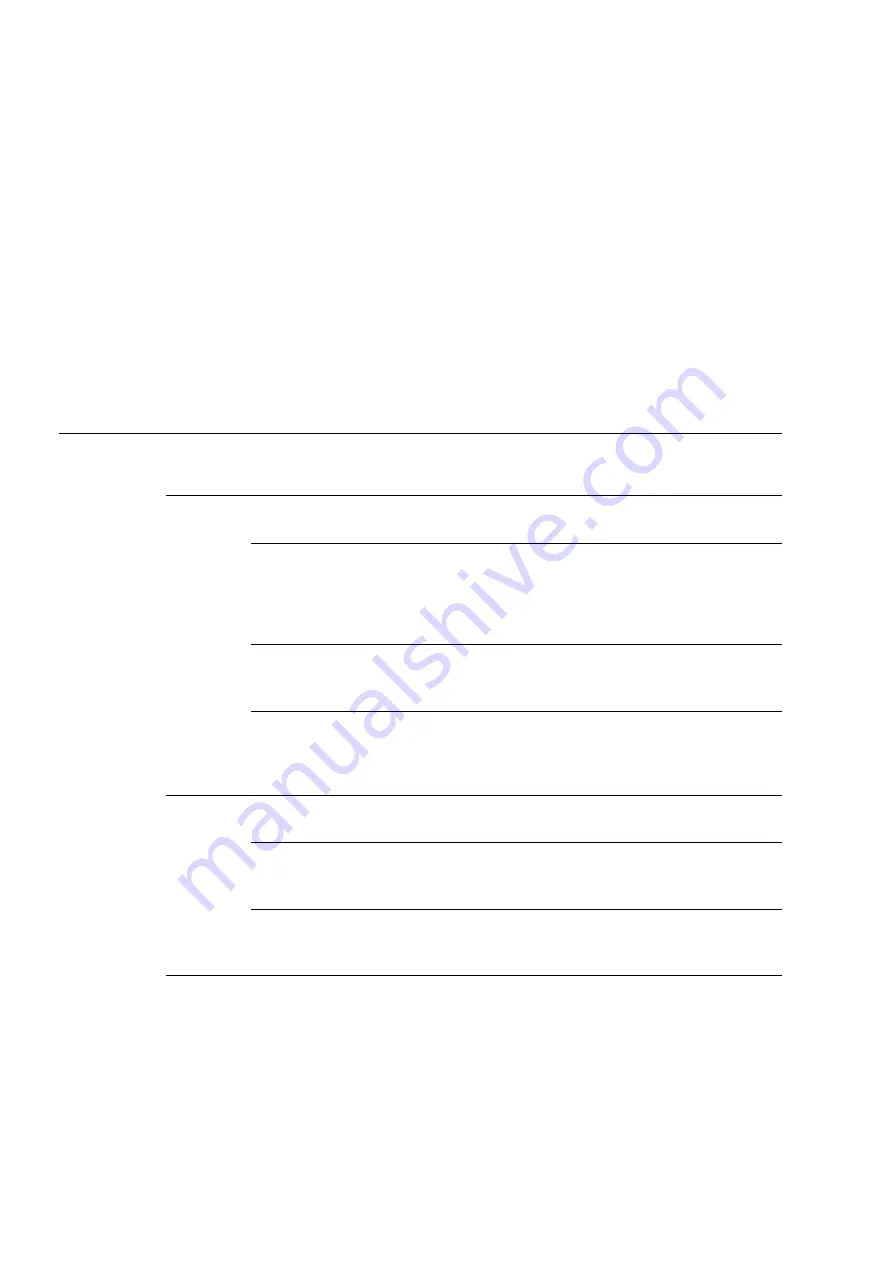
Technical features
D301171 - IO-Link master 1108
3-10
Status displays and diagnostic messages
Status displays via LEDs
The module provides the following LEDs for status display:
PROFIBUS-DP
(not labled, beneath the cover for the address switches):
2 LEDs (left RED, right GREEN) for status monitoring of the PROFIBUS-communication.
RUN
and
ERR
:
Display of the operating state and hard- or firmware errors.
U
B
and
U
L
:
Monitoring of operation and load voltage.
Channel LEDs
–
0
,
2
,
4
,
6
: status display for the IO-Link ports (PIN 4 of the M12-connectors)
–
1
,
3
,
5
,
7
: status display for the digital inputs (PIN 2 of the M12-connectors)
Table 8:
LEDs descrip-
tion
LED
Status
Meaning
Remedy
DP
(2 LEDs)
Green
, ON
Red
, OFF
Device is in Data Exchange
Green
, ON
Red
, ON
Baud rate has been detected,
device is waiting for parame-
ters (WAIT_PRM) or for a
configuration (WAIT_CFG).
– False parameterization and/
or configuration of the device
– The device possibly has to
be configured in the hard-
ware-configuration, first.
Green
, 4 Hz
Red
, 4 Hz
Hardware-error: no control of
any other LED
– The device has to be
changed. Please contact
your TURCK contact person.
Green
, OFF
Red
, ON
No PROFIBUS found, no
baud rate detected
– Check the physical proper-
ties of PROFIBUS (connec-
tion, terminating resistance
etc.)
ERR
OFF
No extended diagnostics
active
-
Red
,
flashing
0,5 Hz
Extended diagnostics active
– Flashes in case of a channel
error together with the
respective channel LEDs
Red
,
flashing
,
4 Hz
Hardware error
– The device has to be
changed. Please contact
your TURCK contact person.