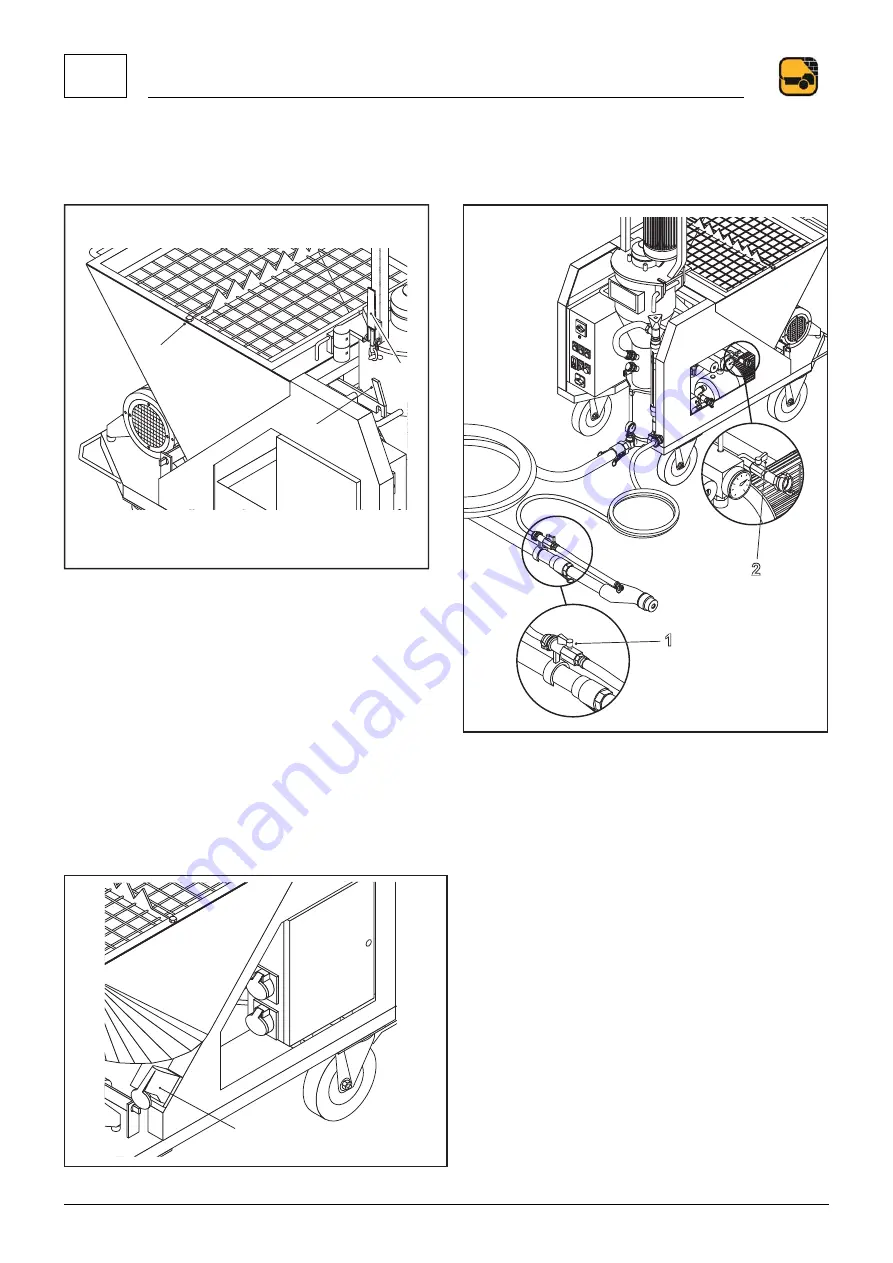
7
USE AND OPERATION
26/46
561379 - IS16/02 - EN
7.3
CHECKS BEFORE SWITCH-ON
Carry out the following checks:
- Check that the protection grid on the hopper is properly secured with the screw shown in the figure (FIG.16-REF.1).
1
2
3
3
1
1
2
2
FIG.16 FIG.17
- Check that the mixing unit is properly locked (FIG.16-REF.2) and the gear motor’s support closing hook (FIG.16-REF.3) is
firmly closed.
- Check that the air cock (FIG.17-REF.1) of the gun is open and the water service cock (FIG.17-REF.2) is closed.
- Check that the dispenser switch, the main disconnecting switch and the water pump switch are at zero.
- Connect the power cable to the socket (FIG.19-REF.1) on the machine’s frame.
1
FIG.19
Summary of Contents for GIOTTO MONO
Page 1: ...Serial number Year USE AND MAINTENANCE MANUAL GIOTTO MONO IS16 02 561379 EN ORIGINAL ...
Page 2: ...THIS MANUAL IS PROPERTY OF TURBOSOL ANY TOTAL OR PARTIAL REPRODUCTION IS STRICTLY FORBIDDEN ...
Page 6: ...1 CE DECLARATION 6 46 561379 IS16 02 EN ...
Page 14: ...4 TRANSPORT AND HANDLING 14 46 561379 IS16 02 EN ...
Page 19: ...INSTALLATION 5 561379 IS16 02 EN 19 46 1 2 FIG 11 ...
Page 20: ...5 INSTALLATION 20 46 561379 IS16 02 EN ...
Page 36: ...7 USE AND OPERATION 36 46 561379 IS16 02 EN ...
Page 38: ...8 MAINTENANCE 38 46 561379 IS16 02 EN ...
Page 40: ...9 DEMOLITION 40 46 561379 IS16 02 EN ...
Page 44: ...10 TROUBLESHOOTING 44 46 561379 IS16 02 EN ...
Page 46: ...11 OPERATOR RESPONSIBILITY 46 46 561379 IS16 02 EN ...