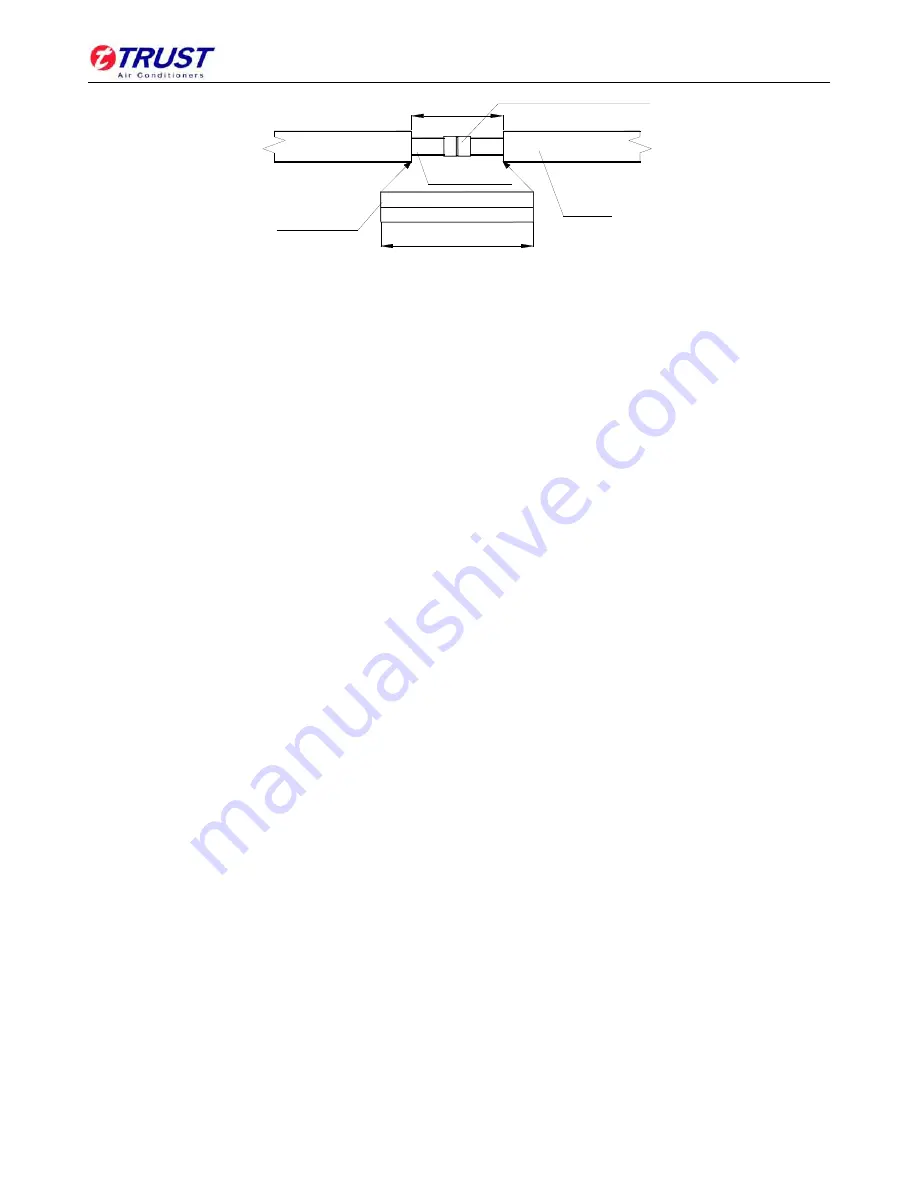
38
Copper
pipe
Insulation
material
400
300
straight
‐
through
joint
Insulation
material
7.2
Drain
Piping
Insulation
Use
rubber/plastic
insulating
tube
with
a
B1
fire
resistance
rating.
The
insulation
should
typically
be
in
excess
of
10mm
thick.
For
drain
piping
installed
inside
a
wall,
insulation
is
not
required.
Use
suitable
adhesive
to
seal
seams
and
joints
in
the
insulation
and
then
bind
with
cloth
reinforced
tape
of
width
not
less
than
50mm.
Ensure
tape
is
fixed
firmly
to
avoid
condensation.
Ensure
the
drain
piping
insulation
adjacent
to
the
indoor
unit
drainage
water
outlet
is
fixed
to
the
unit
itself
using
adhesive,
to
prevent
condensation
and
dripping.
7.3
Ducting
Insulation
Suitable
insulation
should
be
added
to
ducting
in
according
with
all
applicable
legislation.
Figure
3
‐
7.1:
Installation
of
joint
insulation
(unit:
mm)