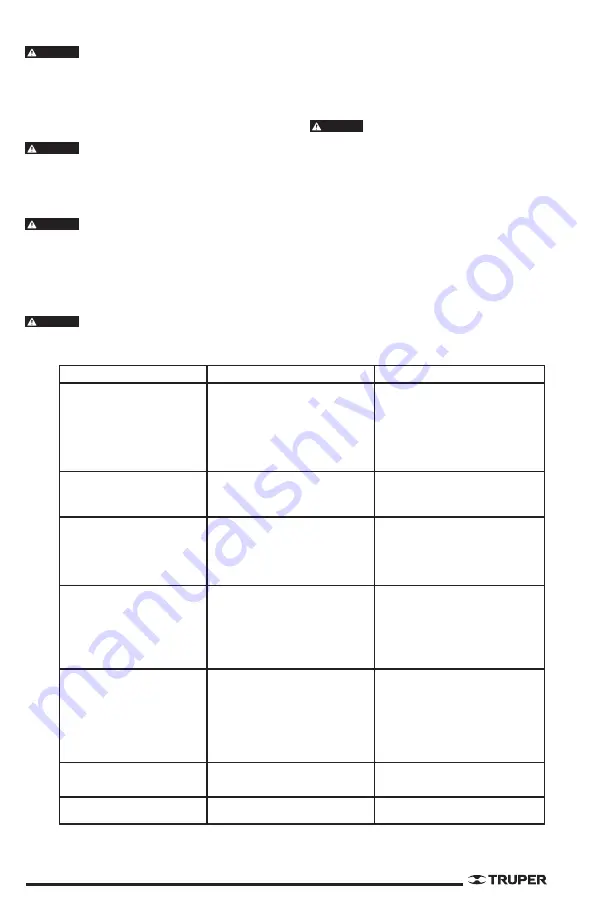
MAINTENANCE AND INSPECTION
Disconnect the unit and release all pressure from the
system before installing, moving or making any maintenance or
service jobs.
Regularly inspect the compressor. Look for visible damage and follow
the maintenance procedure every time you use the unit.
1. Pull the safety valve ring to make it go back to its initial position.
The safety valve shall be replaced in a TASC* if it
cannot be moved or it leaks air after the ring has been released.
2. Turn off the compressor and release pressure from the system.
3. Clean all dust and mud from the motor and air-lines. Move
vertically the cooling blades while the compressor is off.
Set the unit as far away as possible from the spraying
area. The hose will help preventing excessive spraying in the event the
filter gets clogged.
LUBRICATION:
No oil and no lubrication are required for this
compressor.
THERMAL OVERLOAD PROTECTION
This compressor is built with an automatic thermal
overload protector.
It will turn off the motor if there is overload.
If the overload protector turns off the motor too frequently check the
following:
1. Voltage drop.
2. Clogged air filter.
3. Not enough ventilation.
The motor shuts off when the switch is activated. To re-establish the
motor follow the following steps:
1. Press the switch to ensure that the compressor is off.
2. Let the compressor cool down for at least 5 minutes.
3. Press the thermal switch located on the side of the crankcase.
4. Lift the switch to start the compressor.
STORAGE
1. Store the compressor in a dry place while not in use.
2. Disconnect the hose and let both ends open and facing down to
allow drying.
5
WARNING
WARNING
WARNING
WARNING
WARNING
PROBLEM
POSSIBLE CAUSE
SOLUTION
The compressor is not working
1. No electicity
2. Blown fuse in the installation.
3. Switch is open.
4. Thermal overload is activated.
5. Faulty pressure button.
1. Is it connected? Check fuse / switch or
motor overload.
2. Replace blown fuse.
3. Restart and determine what caused the
problem
.
4. The motor will be on when it cools down.
5. Replace in a Truper Authorized Service
Center
.
The motor buzzes but is not running
or runs slowly
1. Check valve is damaged or low.
2. Poor contact, voltage drop.
3. Damaged motor.
1. Replace or repair in a TASC*.
2. Check connections, remove electric
extensions, check circuit using a voltmeter
.
3. Replace motor in a TASC*
The fuses blow
The circuit breaker is repeatedly
activated.
CAUTION!
NEVER USE AN
EXTENSION CABLE WITH THIS UNIT!
1. Wrong fuse size. Overloaded circuit.
2. Faulty or low check valve.
1. Verify you are using the right fuse. Use a
timedelay fuse. Disconnect other units
using the same circuit or operate the
compressor in an independent circuit.
2. Replace or repair in a TASC*
The thermal overload protection
repeatedly shuts down.
1. Voltage drop
2. Blocked air filter.
3. There is no adequate ventilation.
4. Verify if the valve is malfunctioning.
5. The compressor valves are not working.
1. Do not use extension. Check using a
voltmeter
.
2. Clean the filter (see Maintenance section)
3. Move the compressor to a well-ventilated
area.
4. Replace in a TASC*
5. Replace valve in a TASC*
Air outlet is lower than normal. Low
pressure relief.
Pressure in the tank drops when the
compressor stops.
1. Excessive use of air. The compressor is
too small
.
2. Filter inlet is clogged.
3. Air comes out from the pipes (inside the
machine out of the system
)
4. Broken inlet valves.
5. Worn piston ring.
1. Reduce the use of air or buy a larger unit
with more air capacity (CFM)
2. Clean or replace in a TASC*
3. Replace parts in a TASC* or adjust if
necessary.
4. Replace compressor valves in a TASC*
5. Replace piston and cylinder in a TASC*
Compressor stars in a continous
mode and the safety valve opens
when pressure is up.
1. Defective pressure button.
2. Defective safety valve.
1. Go to a TASC*
2. Go to a TASC*
Air leak in the relief valve.
Double-check the valve is not stuck in the
open position.
Remove or replace check valve in a TASC*
TROUBLESHOOTING
TASC*: TRUPER AUTHORIZED SEVICE CENTER