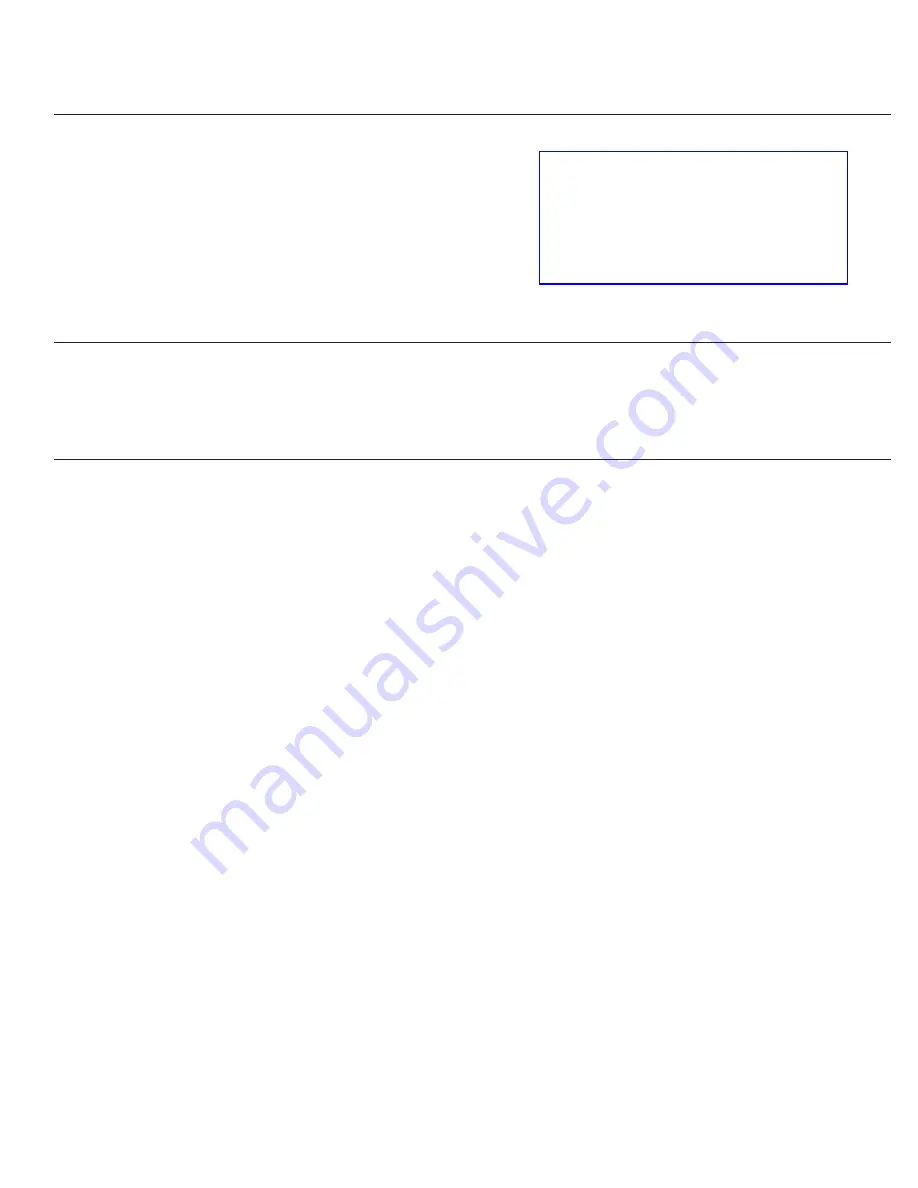
WINE AND BEVERAGE CABINET USE AND CARE MANUAL
25
Dispensing pressures differ according to:
• The type of draft dispensing system
• The length of draft dispensing line
• The actual product - some require
more, some require less
• The temperature of the product
• The pressurizing agent: air pressure,
CO
2
or special blended gases.
PRESSURE
Helpful Hints On Maintaining The Correct Pressure:
• Know which pressurizing agent to
use on which product and why.
• Monitor your regulators to ensure
applied pressure remains constant
• Keep equipment in good repair
do not agitate the kegs unnecessarily. If excessive agitation
occurs allow kegs to settle for 1 to 2 hours before tapping.
Prior to tapping the keg, ensure that all beer faucet in the serving
location are in the off position. Completely remove the dust cover
(identification cap) from the keg.
TAPPINg
DRAfT BEER PROBLEMS
To minimize draft beer problems, always follow the recommended
instructions for temperature and CO
2
pressures from your beer supplier.
flat Beer - Description: foamy head disappears
quickly. Beer lacks usual zestful brewery
fresh flavor.
•
CO
2
turned off when not in use.
•
Contaminated air source (associated with compressed air).
•
Greasy glasses.
•
Not enough pressure.
•
Pressure shut off during night.
•
Loose tap or vent connection.
•
Sluggish pressure regulator.
•
Obstruction in lines.
false Head - Description: Large soap-like
bubbles, head dissolves very quickly.
•
Dry glasses.
•
Improper pour.
•
Pressure required does not correspond to beer temperature.
•
Coils or direct draw beer lines warmer than beer in keg.
•
Small lines into large faucet shanks.
•
Beer drawn improperly.
Wild Beer - Description: Beer, when drawn, is all
foam and not enough liquid beer.
•
Beer drawn improperly.
•
Faucet in bad or worn condition.
•
Kinks, dents, twists or other obstructions in line.
•
Traps in beer lines.
•
Beer too warm in kegs or lines.
•
Too much pressure.
•
Creeping gauge causing too much pressure.
Cloudy Beer - Description: Beer in the glass
appears hazy. Not clear.
•
Dirty glass or faucet.
•
Beer over chilled.
•
Beer temperature variance in keg (Beer may have warmed up
at sometime).
•
Hot spots in beer lines.
•
Cutting beer through faucet.
•
Beer line in poor condition.
•
Dirty lines.
•
Beer that has been frozen.
Bad Taste
•
Dirty faucet.
•
Old or dirty beer lines.
•
Failure to flush beer lines with water after each empty keg.
•
Unsanitary conditions at bar.
•
Foul air or dirt in lines.
•
Oily air; greasy kitchen air.
•
Temperature of package too warm.
•
Dry glasses