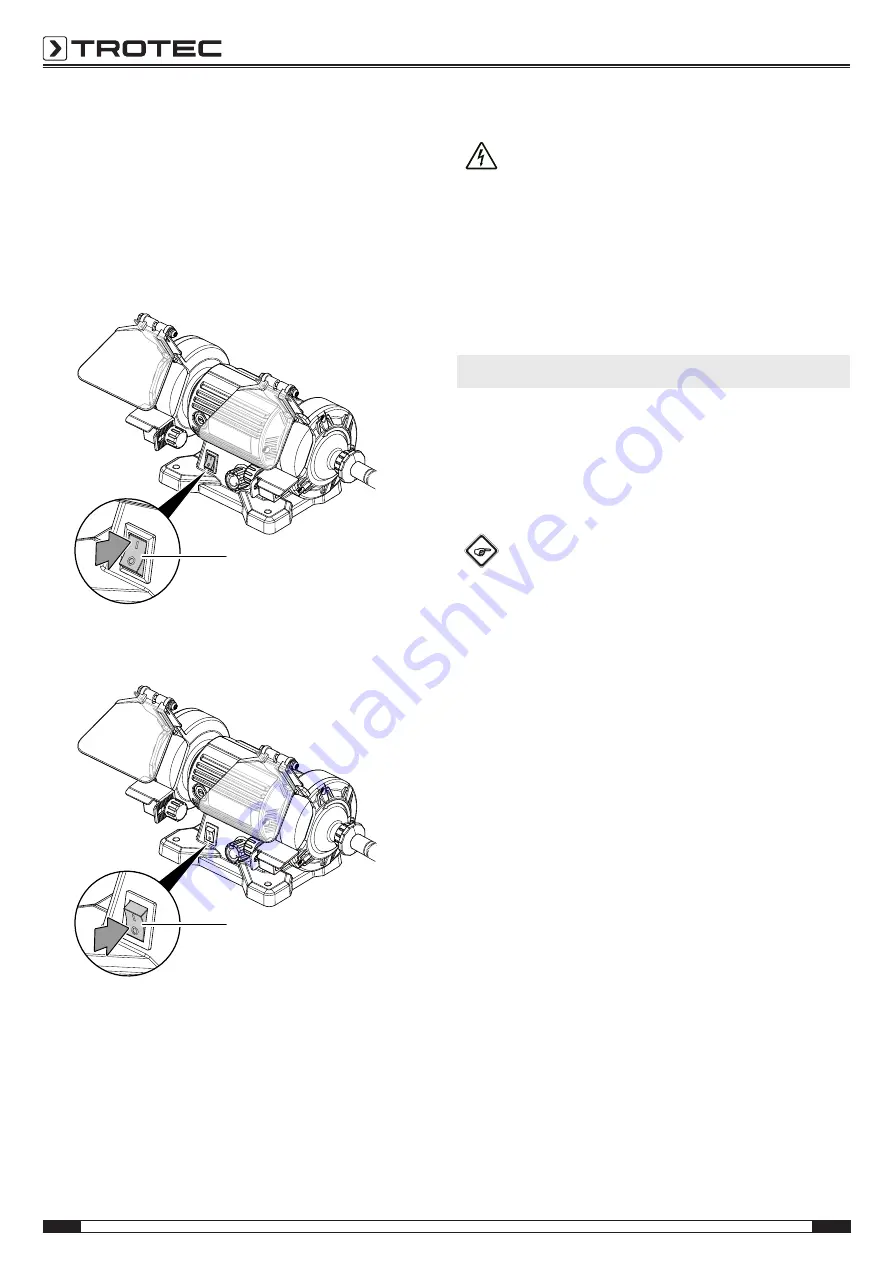
20
EN
bench grinding machine PBGS 10-120
Switching the device on and off
Wear your personal protective equipment when working with
the device.
1. Check whether the fixed tool and the speed set are
suitable for the intended application.
2. Check whether the workpiece is secured and the worktop
prepared correspondingly.
3. Switch the device on by setting the on/off switch (
37
) to
position
I
.
37
4. Switch the device off by setting the on/off switch (
37
) to
position
0
.
37
Shutdown
Warning of electrical voltage
Do not touch the mains plug with wet or damp hands.
•
Switch off the device.
•
Hold onto the mains plug while pulling the power cable out
of the mains socket.
•
If applicable, disassemble the flexible shaft.
•
Clean the device according to the Maintenance chapter.
•
Store the device according to the Transport and storage
chapter.
Errors and faults
The device has been checked for proper functioning several
times during production. If malfunctions occur nonetheless,
check the device according to the following list.
Troubleshooting tasks which require the housing to be opened
must only be carried out by an authorized specialist electrical
company or by Trotec.
Info
Wait for at least 10 minutes after maintenance and
repair work. Only then switch the device back on.
Light smoke or odour is emitted during the first use:
•
This is not a fault. These phenomena disappear after a
brief runtime.
The device does not start:
•
Check the power connection.
•
Check the power cable and mains plug for damage. If you
notice damages, do not try to take the device back into
operation.
If the supply cord is damaged, it must be replaced by the
manufacturer, its service agent or similarly qualified
persons in order to avoid a hazard.
•
Check the on-site fusing.
The device becomes hot:
•
Make sure not to exert too much pressure on the device
during grinding.
•
Check whether the tool is suitable for the tasks to be
carried out.
•
Keep the venting slots clear to prevent the motor from
overheating.