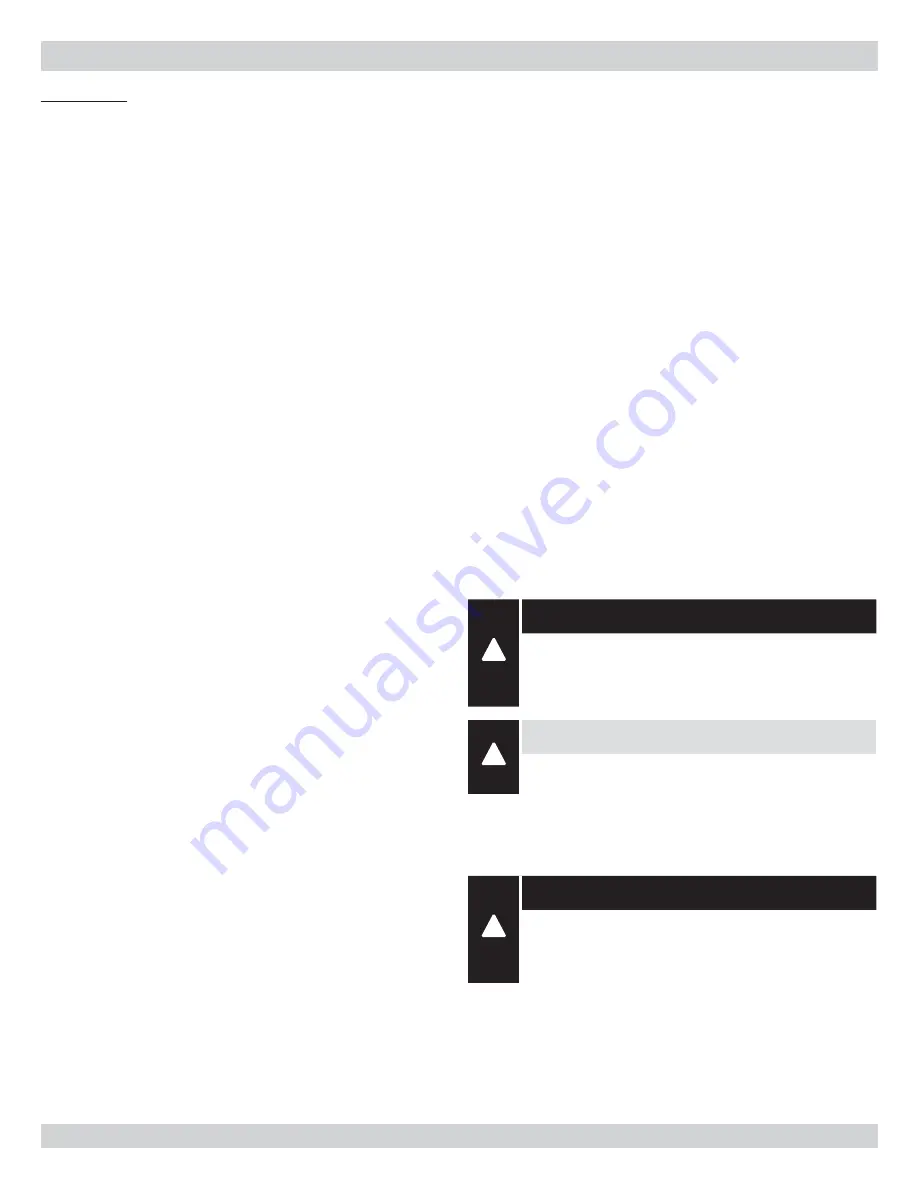
49
ANNUALLY:
To assure trouble free operation, it is recommended that the flue
passages, combustion chamber area (target wall, fire door insulation)
burner adjustment, operation of the controls, and boiler seals (fire
door gasket or silicone seal, cast iron sectional seals, flue collec-
tor) be checked once each year by a competent Service Technician.
Before the start of each heating season (or whenever the system has
been shut down for extended periods of time) recheck the whole sys-
tem for water, oil, and vent piping leaks. Replace or patch any leaks
or seals that are faulty.
VeNT PiPe:
Visually inspect the entire venting system once a month for any
signs of leakage, deterioration, or soot build up. If the vent pipe
shows any signs of leaking or deterioration, replace it immediately.
If it shows any signs of soot build up, clean the vent pipe and have
the burner settings and combustion checked by a competent profes-
sional.
reLieF VALVe:
This valve should open automatically when the system pressure
exceeds the pressure rating (usually 30 psi) of the relief valve. Should
the valve ever fail to open under this condition, shut down the
system. Drain the system until system pressure is reduced below
the relief valve pressure rating. Then contact a competent Service
Technician to replace the valve and inspect the heating system and
determine the cause, as this problem may indicate an equipment
malfunction. The relief valve should be tested bimonthly during the
heating season. Prior to testing, make certain a discharge pipe is
properly connected to the valve outlet and arranged so as to contain
and safely dispose of boiler discharge. Hold the trip lever fully open
for at least five seconds in order to flush free any sediment that may
lodge on the valve seat. Then permit the valve to snap shut. Refer to
the valve manufacturer’s instructions packaged with the valve for
more details.
CONVeNTiONAL eXPANSiON TANK:
As noted in the “EQUIPMENT AND ACCESSORIES” section.
DiAPHrAgM eXPANSiON TANK:
As noted in the “EQUIPMENT AND ACCESSORIES” section.
WATer SYSTeM:
If the system is to remain out of service during freezing weather,
always drain it completely (water left in the system will freeze and
crack the pipes and/or boiler).
MAiNTeNANCe
OiL BUrNer MAiNTeNANCe:
For the Beckett AFG, the following preventative maintenance items
should be performed annually, preferably prior to the heating season.
1.
Fuel Filter
This should be replaced so as to prevent contaminated
fuel from reaching the nozzle. A partially blocked fuel filter can
cause premature failure of the fuel pump.
2.
Fuel Pump Unit
Replace pump screen and clean pump unit to main-
tain fuel delivery to the nozzle.
3.
Ignition Electrodes
Clean and adjust as per manufacturer’s rec-
ommendations, so as to maintain reliable ignition of oil.
4.
Nozzle
Replace so as to maintain safe and reliable combustion
efficiency. Always replace with the exact nozzle as required in the
charts in the back of this manual.
5.
Fan and Blower Housing
These must be kept clean, free of dirt,
lint and oil so as to maintain the proper amount of air the fuel requires
to burn.
6.
Check the burner settings and adjust as needed.
NOTE:
If any component parts must be replaced, always use parts
recommended by the burner manufacturer.
MAiNTeNANCe OF OPTiONAL LOW WATer CUT OFF
!
DANGER
Assure that the boiler is at zero pressure before removing the re-
lief valve or any probe. Open the safety valve to relieve all internal
pressure prior to proceeding. Safety valve discharge piping must
be piped such that the potential for burns is eliminated.
!
WARNING
Probe type low water cut-off devices require annual inspection
and maintenance.
Although these devices are solid state in their operation, the probe is
exposed to possible contamination in the boiler water and subject to
fouling.
!
DANGER
Do not install valve between boiler and controls manifold. This
would isolate safety and controls from the boiler. A shut off
valve may be installed after the manifold to facilitate LWCO
probe removal.
It is important to physically remove the probe from the LWCO tap-
ping annually and inspect that probe for accumulation of scale or