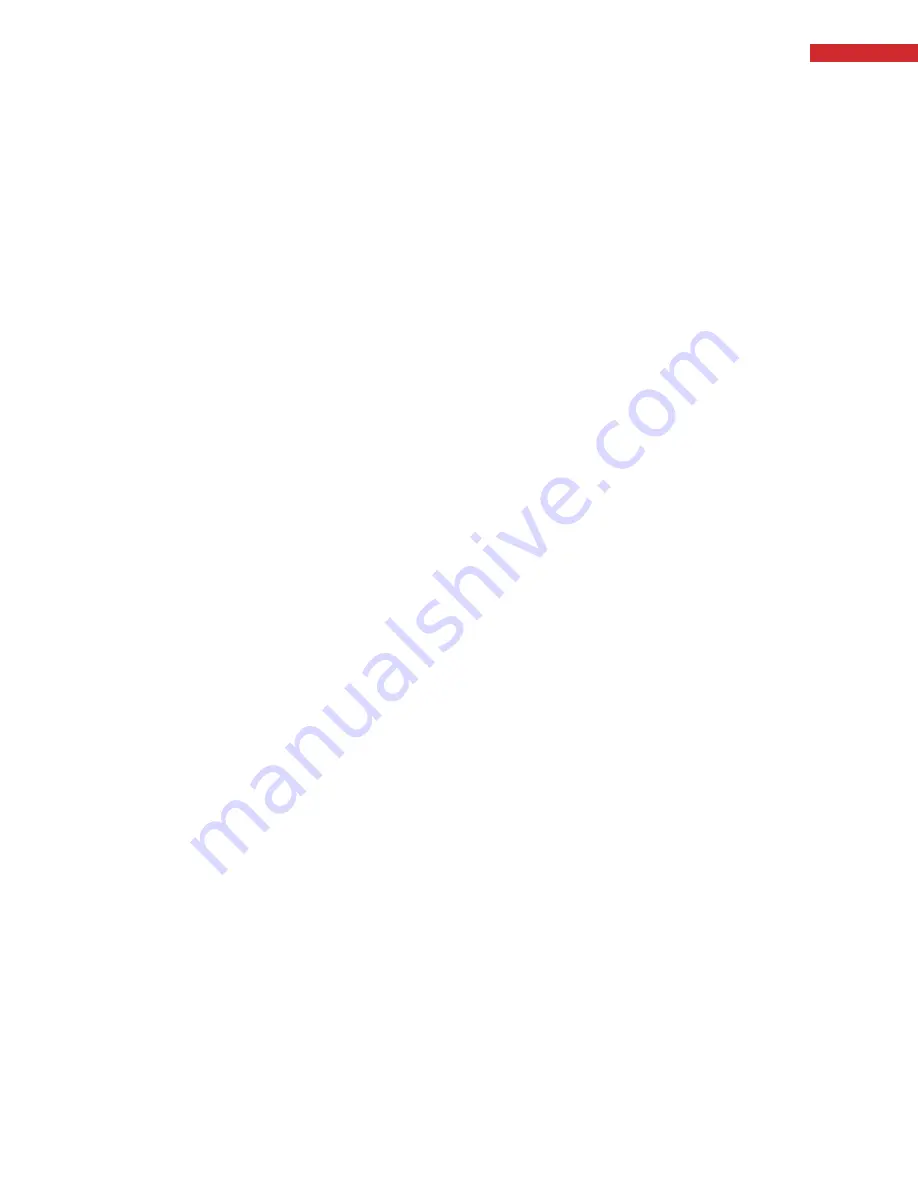
15
Model 2400 High-Pressure Filling System User Guide
Index
Assembly
Utilities, 8
Assembly and Setup, 8
Compressed Air Requirements, 8
Description of System Components, 6
Dimensions, 14
Help, 4
Operation, 9
Optional Equipment,
13
Parts Included, 9
Product Overview, 5
Replacing the Material Reservoir, 12
Safety, 4
Personal Protective Equipment, 5
Preventing Injection Injury, 5
Using Safe Operating Pressures, 4
Spare Parts and Accessories,
13
Specifications, 13
Support, 4
System Features, 5
Unpacking, 8
Utilities, 8
Warranty, 14