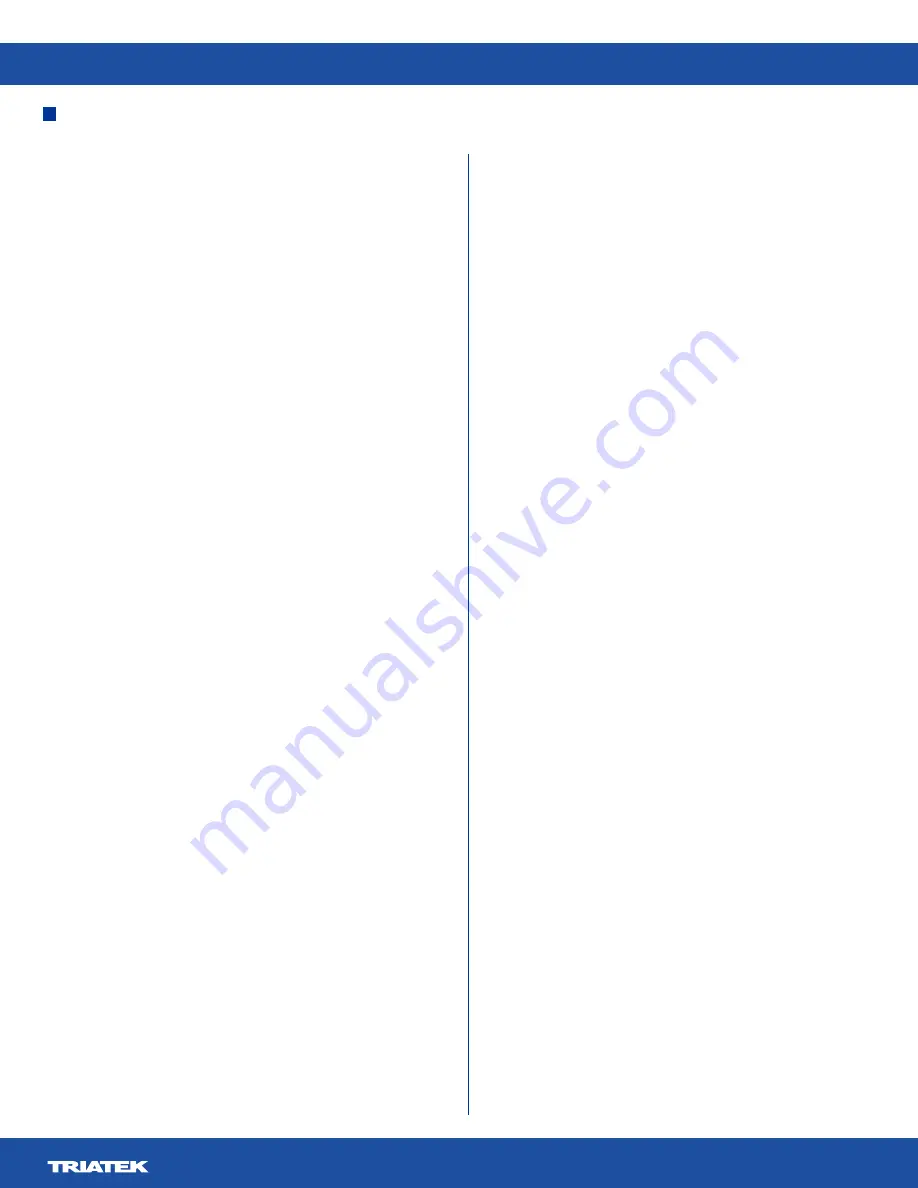
UVM-1000
LIT-12013155
4
Introduction
Triatek’s Universal Valve Module (UVM) is designed to allow for
interoperability between Triatek Venturi valves and third party
controllers.
Each Triatek valve is individually calibrated and has its own
unique position to cubic feet per minute (cfm) curve. The UVM
enables you to create a linearization curve in each controller for
each associated valve. It also allows you to span, scale, and
linearize the feedback sensor to obtain useful information from it.
Overview of Operation
A diagram of the basic functionality of the UVM is shown in
Figure 1
.
The UVM takes a 0 -10 V signal from the third party equipment,
and depending on the scaling setting, interprets this as a 0 –
xxxx cfm request signal. The UVM is pre-programmed with the
associated valve’s linearization curve, and will move the valve’s
actuator to the correct position for the requested cfm.
Each valve is fitted with an electronic position sensor on the lever
arm at the point of entry into the valve body (see
Figure 1
). The
electronic position sensor is used to provide actual valve position
information to the controllers. This signal is non-linear, and has a
random 0 and 100% position voltages.
It converts the sensor signal to a position on the valve and then
translates that to a cfm value. The cfm value is in turn output
from the UVM as a 0 – 10 V signal at the same scaling as the
cfm request signal.
The 0 -10 V signal is processed by the valve’s calibration
settings as set by the factory. The user has the ability to access
and adjust this curve if so desired. The subsequent signal is
then converted to an equivalent cfm request value. This value
is dependent on settings provided by the factory as applicable
for the associated valve size. The user can modify this signal if
desired.
The factory default settings relative to valve size are:
8 in. valve 10 V = 800 cfm
10 in. valve 10 V = 1100 cfm
12 in. valve 10 V = 1600 cfm
14 in. valve 10 V = 2300 cfm
The equivalent cfm request value is applied to the calibration
curve as entered by the factory for the associated valve and a
corresponding valve position value is generated.
This position value is applied to the actuator output voltage
calibration section and output to the actuator. The consequent
result is that the actuator will move to the required position so
that the valve passes the requested cfm.
As the valve moves to position, the position feedback sensor
moves as well. The signal from this sensor is processed by a
sensor voltage to position calibration section. The output of this
section provides an accurate position value. The position value is
applied to the position to cfm mapping table and a corresponding
cfm value is output.
This cfm value is then passed through cfm to voltage scaling
factor and converted to a voltage value. This value is then
passed through the factory set output calibration section and
made available to the voltage output for use by the third party
equipment as the actual valve cfm.
In certain circumstances the feedback signal may not match the
requested cfm signal. If 0 cfm is requested (0V input), and the
valve is a partially closed valve, the valve has a minimum cfm
that it can attain. This value is not 0 and for a 12 in valve would
be around 90cfm. In this case the feedback signal would be the
equivalent of 90 cfm or 0.56V for a 10V = 1600 setting.
If a UVM for an 8 in. valve is set with an arbitrary scaling of 10V
= 1100 cfm (or 110 cfm / volt), and a request signal of 9 V (or 990
cfm) is input to the unit, then the actuator will end up driving to
100%, as the maximum the valve can do is 700 cfm. The voltage
feedback output signal will only be around 6.4 V as the actual
valve cfm would be around 700.
Introduction / Overview of Operation