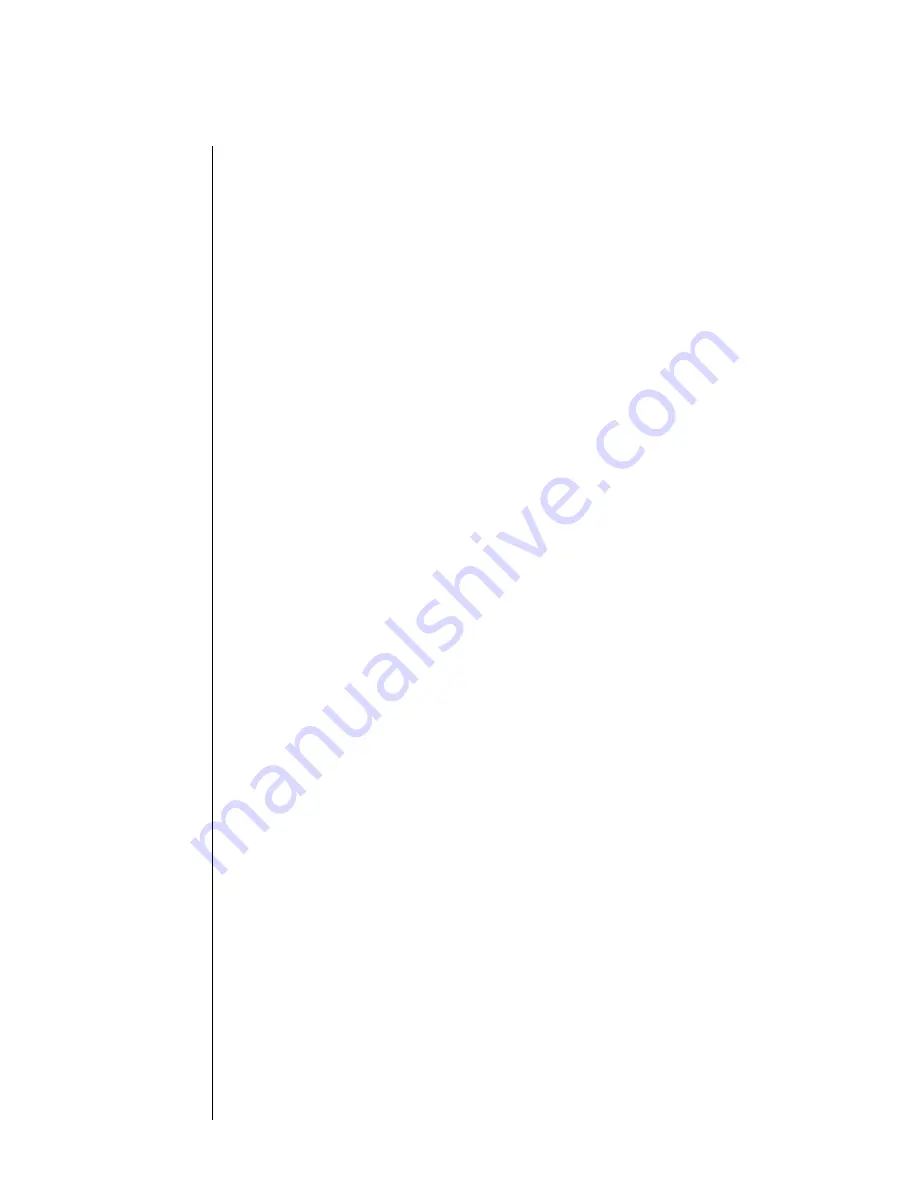
Page 21
The TAC Crimper has been extensively redesigned. The redesign results in additional
logic functions being added to prevent possible malfunctions, while at the same time
reducing the overall number of components. Additionally, an HMI display has been
incorporated to provide easier and a more intuitive interface to the TAC. Also, the HMI
display provides error messages, allowing for fast and accurate diagnosis and
correction.
All logic, control and operating functions of the TAC Crimper are performed
pneumatically, electrically or both.
The purpose of this Theory of Operation is to provide an overview of how the TAC
operates such that a general understanding of functions can be achieved. In the event
a TAC were to malfunction, familiarity with its operational sequences will greatly
expedite corrective action.
System design is such that many events are sequential and, unless the TAC is
positive a given event has properly occurred, subsequent events will not occur. This
design, in conjunction with high tolerance machined components, reduces significantly
the possibility of initiating crimps on incorrect contacts, or proceeding to crimp
additional contacts if proper crimp tolerances are not being achieved.
If the crimped contact/conductor is not removed after the crimping cycle is complete,
the TAC will pause. The TAC will remain in the "pause" position until the contact/
conductor is removed.
*Please refer to Figure 6-1 & 6-2 while reading this Theory of Operation.*
Air pressure is supplied to the TAC via the primary input and sleeve valve. The primary
air supply is used to control release of shoulder-less contacts at shoulder-less shuttle
mechanism. The operator-controlled Sleeve Valve (SV) supplies air to all valves, air
cylinders, air sensors and air activated switches.
Electrical power is suppled to the TAC control system via an internally mounted
transformer. Transformer and feeder-bowl power is supplied from standard 120V outlet
(European model 220V). Transformer power is switched on via switch S-5. Output
from the transformer (12V DC) is supplied to the PLC (control system) of the TAC.
The system air supply is filtered at (F-1) and overall system air pressure is regulated
by Regulator (R-1). (FOR LOCATION OF COMPONENTS, REFER TO FIGURES 6-1
& 6-2, in the Maintenance section). The air pressure at R-1 should be approximately
85 PSIG, and may be monitored with Pressure Gauge (G-1). Pressure to maintain the
slide cylinder (SC-1) in the up (ready-to-crimp) position is regulated by Regulator
(R-2). This pressure should be approximately 20 PSIG, and may be monitored with
Pressure Gauge (G-1) by depressing PB-1 switch. Regulators(R-3 and R-4) are
factory-adjusted to approximately 4 to 8 PSIG to provide low pressure pilot signals for
the slide and crimp complete sensors. No adjustments should be made unless
absolutely certain the adjustment is required. Indiscriminate changes to regulator or
switch settings should not be made. A clean air supply is imperative to proper system
operation. Filter F-1 should be drained or changed, as required.
I
NTRODUCTION
T
HEORY
OF
OPERATION
P
NEUMATIC
SUPPLY
Section 5
Summary of Contents for TAC 17X
Page 5: ...Page 5 Figure 1 1 TAC 17X Front View ...
Page 7: ...Page 7 Figure 1 2 Wire Insertion Through Funnel ...
Page 10: ...Page 10 Primary air input at rear of TAC Figure 2 1 Pneumatic Hook Ups ...
Page 16: ...Page 16 Crimp Inspection Points Improper Crimps Figure 3 3 Crimped Samples ...
Page 25: ...Page 25 Figure 6 1 TAC 17X Pneumatic Control Panel ...
Page 26: ...Page 26 Figure 6 2 TAC 17X Components Right View ...
Page 38: ...Page 38 ...
Page 39: ...Page 39 Carefully Remove Hose Clamp ...
Page 42: ...Page 42 ...
Page 47: ...Page 47 Figure 7 3 TAC 17X Pneumatic Diagram ...