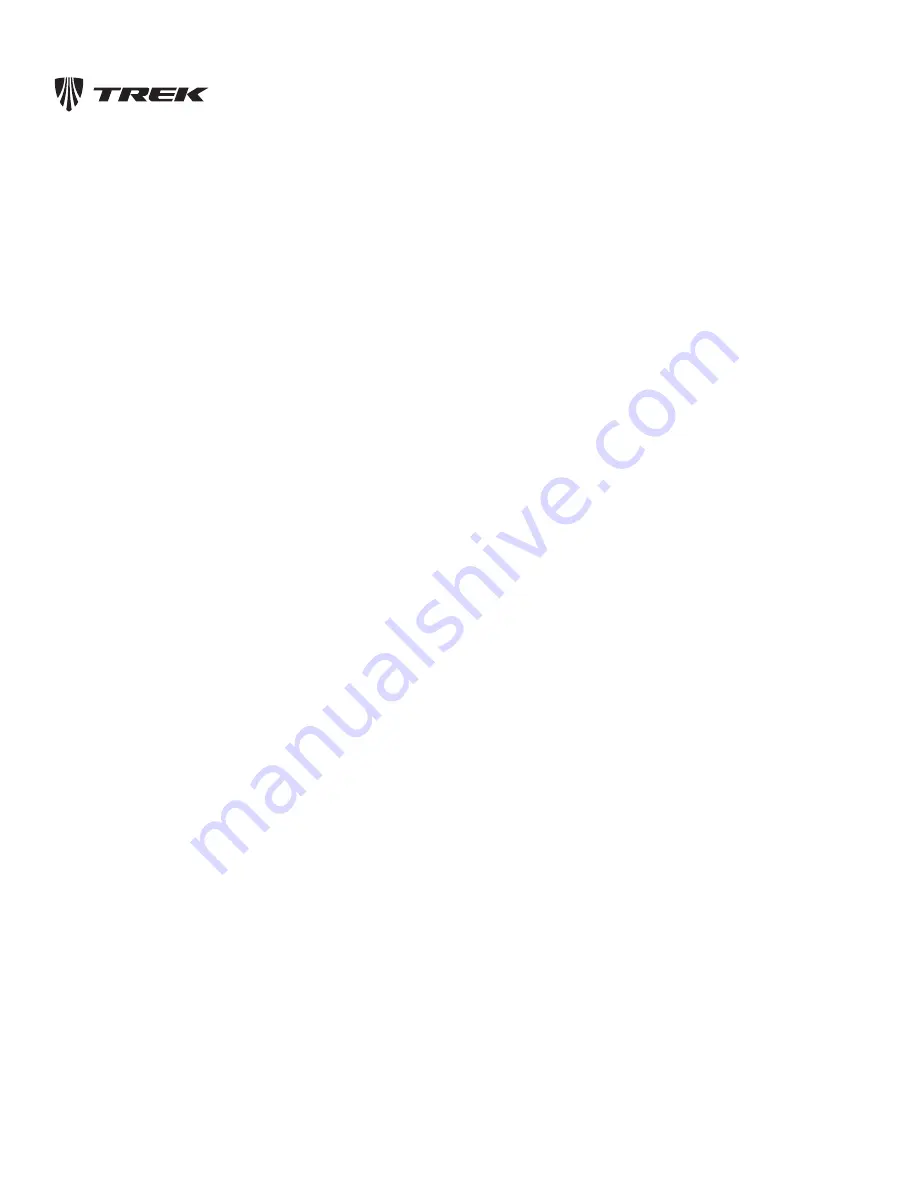
2
TREK SERVICE INFORMATION August 2016
2. Speed Concept General Information
The Speed Concept design incorporates a number of special parts with special features.
This section gives a brief explanation of some of the features, their use and maintenance,
and general information about the bike.
Changes From The Previous Version
The 2014 Speed Concept looks similar to the previous version, but there are many changes.
These changes make ‘upgrading’ to the new design impossible. For example, due to a
larger-diameter steering axle and a 20 mm shorter head tube on every frame size, the new
fork is not compatible with the old frame. However, the benefits to the new design make the
changes entirely worthwhile. Here are some of the changes:
•
Two-bolt, rear-access seatpost clamp
•
Seatpost with two-bolt saddle clamp
•
Larger-diameter aluminum alloy steering axle with integrated bearing preload feature
•
Steering bumper to reduce possible damage under full fork rotation
•
‘Mono’ aero extension, with bottle mount on top of stem
•
New housing routing from bar to frame, with new cover
•
Carbon fiber dropouts on 9 Series
•
Carbon fiber front derailleur hanger
•
Mega seat-box option
Special Features And Assembly Information
The Speed Concept frame and parts incorporate state-of-the-art technology and design.
This may require special consideration or techniques during assembly, use, or maintenance.
•
Compatibility of parts-
Trek only recommends Bontrager parts for the Speed Concept
bike because with these parts the torque specifications and crush strength have been
evaluated by our engineering staff. Other parts might not meet our requirements, and
could lead to damage.
•
Carbon fiber construction-
Carbon fiber composite is by weight the lightest, strongest
frame material available today. Please read about special care needed for carbon fiber
in your Trek bicycle owner’s manual.
•
Integrated fork design-
The leading fork design provides the least wind drag of any
bicycle we have ever designed. With the carefully integrated head tube / fork interface,
hidden head bearings, and hidden brakes, the air flows smoothly across the frame.
However, this design limits the rotation of the fork; if you turn the aerobar too far the
fork will contact the frame, possibly damaging the paint. For 2014 we have added an
integrated fork bumper to reduce damage. However, care still needs to be taken.
•
Internal cable routing-
To minimize wind drag, the cables and housing of the Speed
Concept are hidden to the maximum extent possible.
•
Seatpost for either time trial or triathlon-
The seatpost can be rotated 180 degrees to
gain different positions. In addition, there are two lengths of seatposts and two offsets
available.