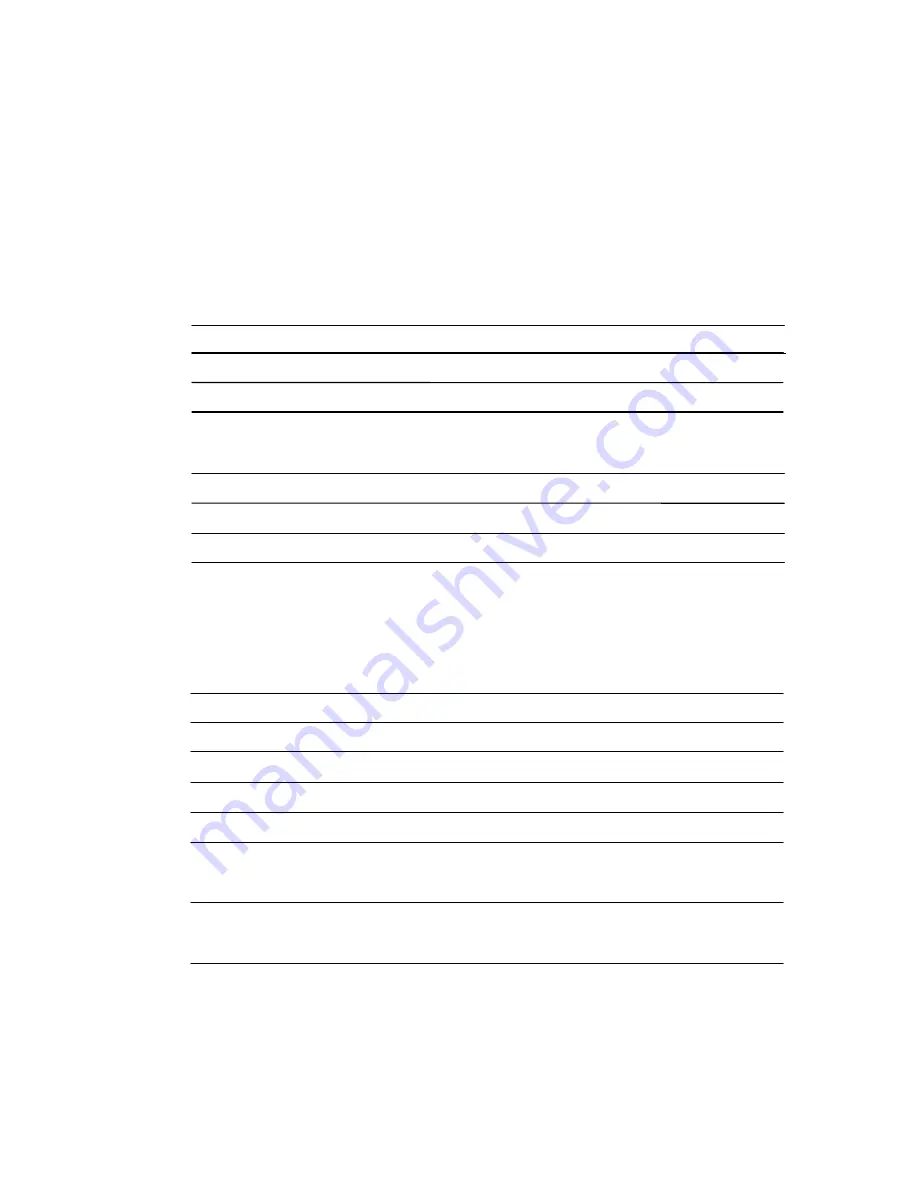
Model 750
Series 700
Maintenance Manual
Page 8
Rev H
Checking Environmental Conditions of OEM Product
The Model 750 is designed to be placed within any OEM product that has been designed
to support the weight of the printer (about 6 pounds or 2.7 kg). Be aware that the
environmental conditions of the location where you place the printer have an affect
on the it’s performance and longevity.
Printer Environmental Conditions
The printer will run its best when stored and operated in an environment
that meets the following temperature and humidity conditions.
•
Operating:
0° to 40°C/32° to 113° F
•
Storage:
-20° C to 70° C *
•
Shipping:
-40° to 70°C *
Relative Humidity
•
Operating:
5% to 90% (non-condensing)
•
Storage:
10% to 90% (non-condensing)
•
Shipping:
95% (non-condensing)
* Exposure to high or low temperatures for periods of greater
than 48 hours will lead to significantly reduced print head life.
Ticket Environmental Conditions
Activation Temperature
Initial
74
±
5
°
C
Effective
83
±
5
°
C
Optimum
90
±
5
°
C
Image
Black
Development
1.35/1.60 (ATLANTEK 0.5 ms)
1.10/1.40 (ATLANTEK 0.35 ms)
Ticket type
Kanzaki TO-381N or approved equivalent
Ithaca Ticket Part Number 100-02108