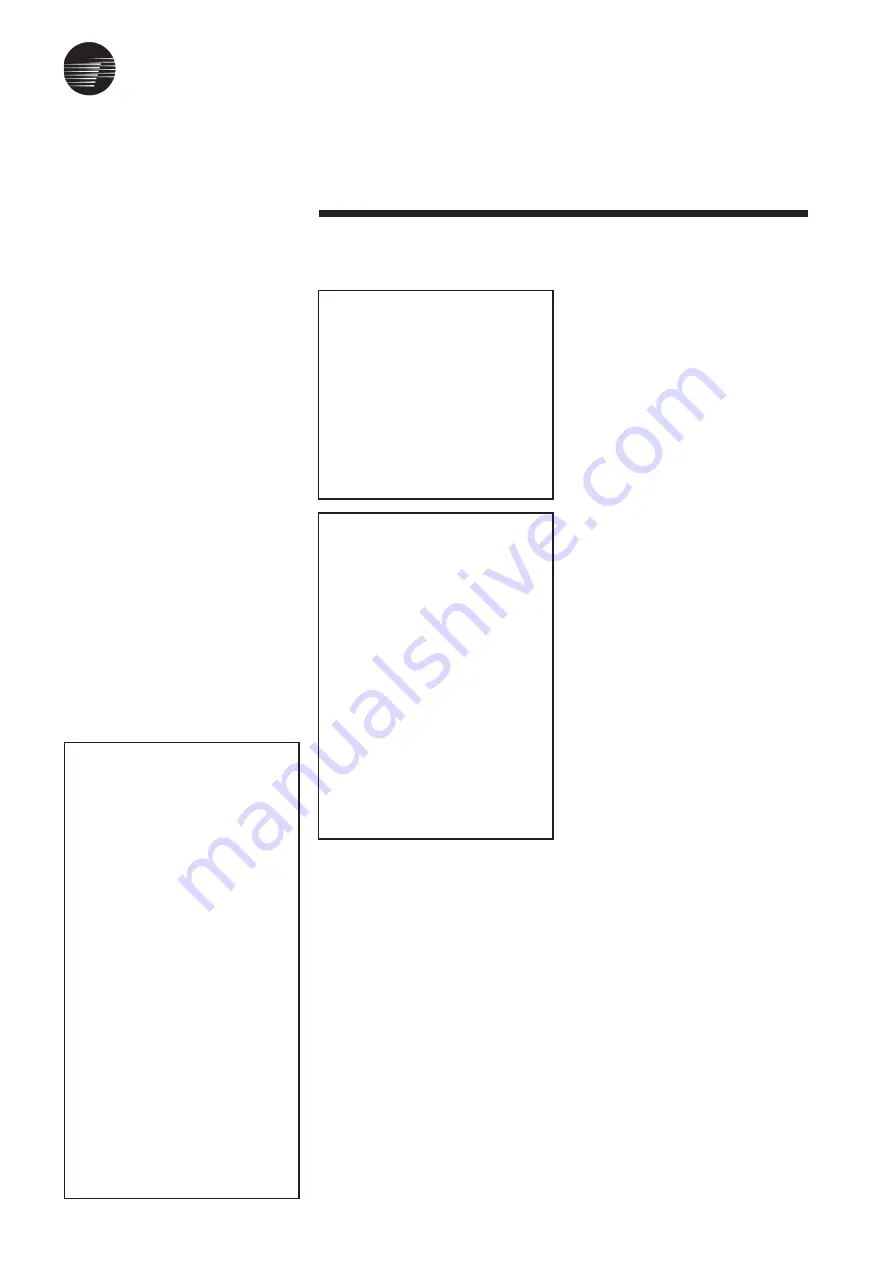
TRANE
®
Coil / Condenser Cleaning
12
Coil Fins and External
Surface Cleaning
Coils should be kept clean to maintain
maximum performance. For operation
at its highest efficiency, the refrigerant
coil should be cleaned often during
periods of high cooling demand or
when dirty conditions prevail. A routine
cleaning schedule (minimum of once
per year) is recommended to prevent
dirt buildup in the coil fins, where it may
not be visible.
Remove large debris from the coils and
straighten fins before cleaning.
Remove filters before cleaning.
Clean refrigerant coils with cold water
and detergent, or with one of the
commercially available chemical coil
cleaners. Rinse coils throughly after
cleaning.
Mechanical Cleaning of
Condenser
The mechanical method of cleaning
the condenser is used for removing
mud and other loose material from the
condenser. Complete the following:
1. Turn off condenser supply water.
2. Remove condenser end plates by
removing clamp bolts. This
exposes the condenser tubes.
3. Rotate a round brush through the
tubes to loosen contaminant.
4. Flush tubes with water which will
flush the sludge out through the
drain opening in the bottom of the
supply header and the drain
opening in the return pipe.
5. Replace condenser end-plates and
clamps. The end-plates must be
centered when the clamp is
tightened.
6. Replace coil headers with gaskets
and torque bolts to 50 ft-lbs.
Chemical Cleaning of
Condenser
Chemical cleaning removes scale
deposits built up by minerals in the
water. For a suitable chemical
solution, consult a water treatment
specialist. The condenser water circuit
is composed of copper, steel, and cast
iron.
See Figure 5 for a typical piping
arrangement for chemically cleaning
the condenser. All materials used in
the external circulating system, along
with the quantity of cleaning material,
duration of cleaning time and safety
precautions necessary for handling the
cleaning agent, should be provided or
approved by the chemical supply
house.
Caution: Do not clean the refrigerant
coil with hot water or steam. The use
of hot water or steam as a refrigerant
coil cleaning agent will cause high
pressure inside the coil tubing and
subsequent damage to the coil.
Caution: Do not use acidic chemical
coil cleaners. Do not use alkaline
chemical coil cleaners that, after
mixing have a pH value greater than
8.5, without also using an aluminium
corrosion inhibitor in the cleaning
solution. If these instructions are
followed, the unit could be damaged.
WARNING: Some chemical coil-
cleaning compounds are caustic or
toxic. Use these substances only in
accordance with the manufacturer
’
s
instructions Failure to do so may
result in injury, death or equipment
damage.
Caution: Failure to properly drain
and vent coils when not in use during
freezing temperatures may result in
coil freeze-up damage.
Caution: Failure to provide adequate
water treatment in condenser
systems may result in fouling of the
coil and condenser surfaces or
undue metal damage.
Condenser Cleaning
Condensing water contains minerals
that collect on the condenser tube
walls. Cooling towers also collect dust
and foreign materials that deposit in
the condenser tube. The formation of
scale or sludge in the condenser is
indicated by a decrease water flow, low
temperature difference between inlet
and outlet water, and abnormally high
condensing temperatures. To maintain
maximum condenser efficiency, the
condenser must remain free of built-
up scale and sludge, and may be
cleaned either mechanically or
chemically.
Customer Note
The use of improperly treated or
untreated water in this equipment may
result in scaling, erosion, corrosion,
algae or slime. The services of a
qualified water treatment specialist
should be engaged to determine what
treatment, if any, is advisable. Trane-
Ingersoll Rand warranty specifically
excludes liability for corrosion, erosion
or deterioration of Trane-Ingersoll
Rand equipment. Trane assumes no
responsibilities for the results of the
use of untreated or improperly treated
water, or saline or brackish water.
Summary of Contents for WCVS 12H
Page 2: ......
Page 6: ...TRANE General Specification WCVS 270 12H 2...
Page 7: ...TRANE 3...
Page 15: ...TRANE Operation Start Up 11 Figure 4 Fan Duct Layout Comment Figure 5 A A A A R 6o minimum A A...
Page 20: ...TRANE Unit Dimensions Water Cooled Vertical System WCVS 270 330 16...
Page 21: ...TRANE Unit Dimensions Water Cooled Vertical System WCVS 400 470 17...
Page 22: ...TRANE Unit Dimensions Water Cooled Vertical System WCVS 530 600 660 18...
Page 23: ...TRANE Unit Dimensions Water Cooled Vertical System WCVS 730 800 19...
Page 24: ...TRANE Unit Dimensions Water Cooled Vertical System WCVS 900 12H 20...
Page 25: ...TRANE Wiring Diagram With Starter WCVS 270 330 21...
Page 26: ...TRANE Schematic Wiring Diagram With Starter WCVS 400 22...
Page 27: ...TRANE Schematic Wiring Diagram With Starter WCVS 470 530 23...
Page 28: ...TRANE Schematic Wiring Diagram With Starter WCVS 600 660 730 800 24...
Page 29: ...TRANE Schematic Wiring Diagram With Starter WCVS 900 25...
Page 30: ...TRANE Schematic Wiring Diagram With Starter WCVS 12H 26...
Page 31: ......