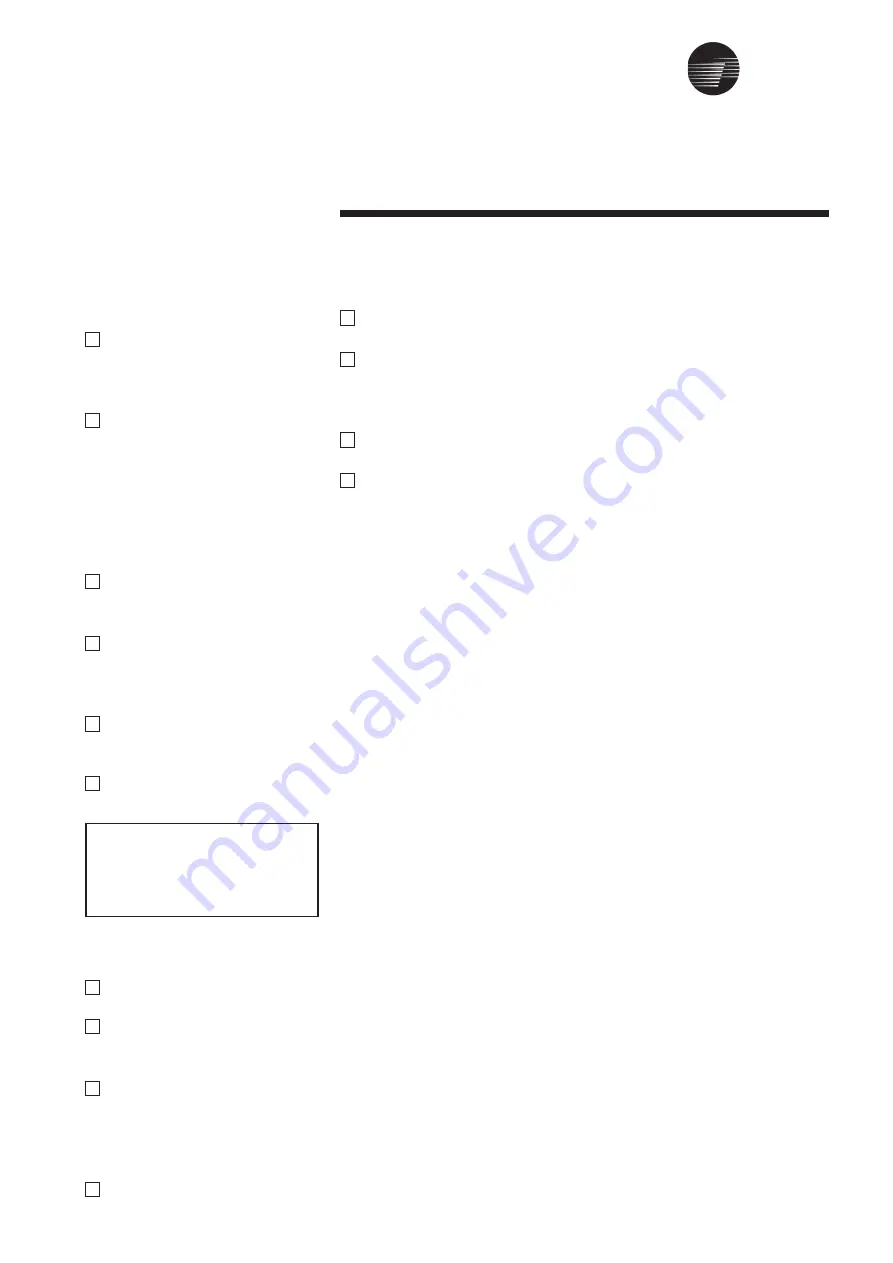
TRANE
®
Operation / Start-Up
9
Check the liquid line sight-glass.
Presence of bubbles indicates
possible shortage of refrigerant or
dirty liquid line filter driers.
A noticable temperature drop
across the filter driers (more than 5
deg.
0
F) indicates dirt or obstruction
in the filter driers. Replace filter drier
if necessary.
Monthly maintenance
Inspect unit air filter. Clean or
replace if filters are dirty and
blocking airflow.
Inspect coils for excess moisture or
icing. Icing may be due to restricted
air flow or shortage of refrigerant
flow across the coil.
Check condensate flow though
drainpipe. Remove any obstructions
or algae if found.
Check tension and condition of fan
belts.
Inspect fan motor for proper
lubrication.
With power disconnected, manually
rotate the fan wheel to check for
obstructions in the housing.
Check alignment of fan assembly
sheaves. Tighten setscrews for their
proper torques.
Annual maintenance
Check and tighten all setscrews,
bolts, locking collars and sheaves.
Inspect, clean and tighten all
electrical connections.
Inspect the TXV sensing bulbs for
cleanliness, good contact with
suction line and insulated from
ambient.
Check superheat setting of TXV. It
should be 11
0
F to 14
0
F.(6-8
0
C)
Drain the condenser water system
and throughly inspect for fouling.
Clean the condensers.
Note: Belt tensions should be
checked and adjusted at least twice
during the first few days of new belt
operation.
Weekly maintenance
Six month interval
Required Unit Service
Envelope
The following summarizes the envelope
around each unit size which is required
for proper service access. The
assumption in establishing these
service envelopes are listed below:
1.
2.
Adequate service clearance has NOT
been left for the following: (It is unlikely
these service procedures will be
needed).
* Condenser cleaning using the brush
Service envelopes shown are
assumed to be the absolute
minimum space required to service
a unit. It is suggested that unit-to-
wall clearance on all sides be
900mm, except where more room is
already specified; this will allow
easier access to all components for
general unit servicing.
Room for general maintenance of
fans and refrigerant components
was considered. Also the minimum
room required to remove fans, fan
motors and compressor servicing is
considered. Cleaning of the
condenser waterside tubes must be
accomplished by the use of a flexible
type brush cleaning machine.
with a straight rod.
* Relining condensers.
* Relining evaporator coils.
* Replacing evaporator coils.
* Shaft removal.
3.
4.
The clearance specified on the unit
control panel side is the clearance
which is required for general unit
servicing and not that which is
required by local electrical codes.
The required control panel clearance
must be determined by the applicable
codes in that region.
Refer to the unit dimension al data
for recommended clearance.
Summary of Contents for WCVS 12H
Page 2: ......
Page 6: ...TRANE General Specification WCVS 270 12H 2...
Page 7: ...TRANE 3...
Page 15: ...TRANE Operation Start Up 11 Figure 4 Fan Duct Layout Comment Figure 5 A A A A R 6o minimum A A...
Page 20: ...TRANE Unit Dimensions Water Cooled Vertical System WCVS 270 330 16...
Page 21: ...TRANE Unit Dimensions Water Cooled Vertical System WCVS 400 470 17...
Page 22: ...TRANE Unit Dimensions Water Cooled Vertical System WCVS 530 600 660 18...
Page 23: ...TRANE Unit Dimensions Water Cooled Vertical System WCVS 730 800 19...
Page 24: ...TRANE Unit Dimensions Water Cooled Vertical System WCVS 900 12H 20...
Page 25: ...TRANE Wiring Diagram With Starter WCVS 270 330 21...
Page 26: ...TRANE Schematic Wiring Diagram With Starter WCVS 400 22...
Page 27: ...TRANE Schematic Wiring Diagram With Starter WCVS 470 530 23...
Page 28: ...TRANE Schematic Wiring Diagram With Starter WCVS 600 660 730 800 24...
Page 29: ...TRANE Schematic Wiring Diagram With Starter WCVS 900 25...
Page 30: ...TRANE Schematic Wiring Diagram With Starter WCVS 12H 26...
Page 31: ......