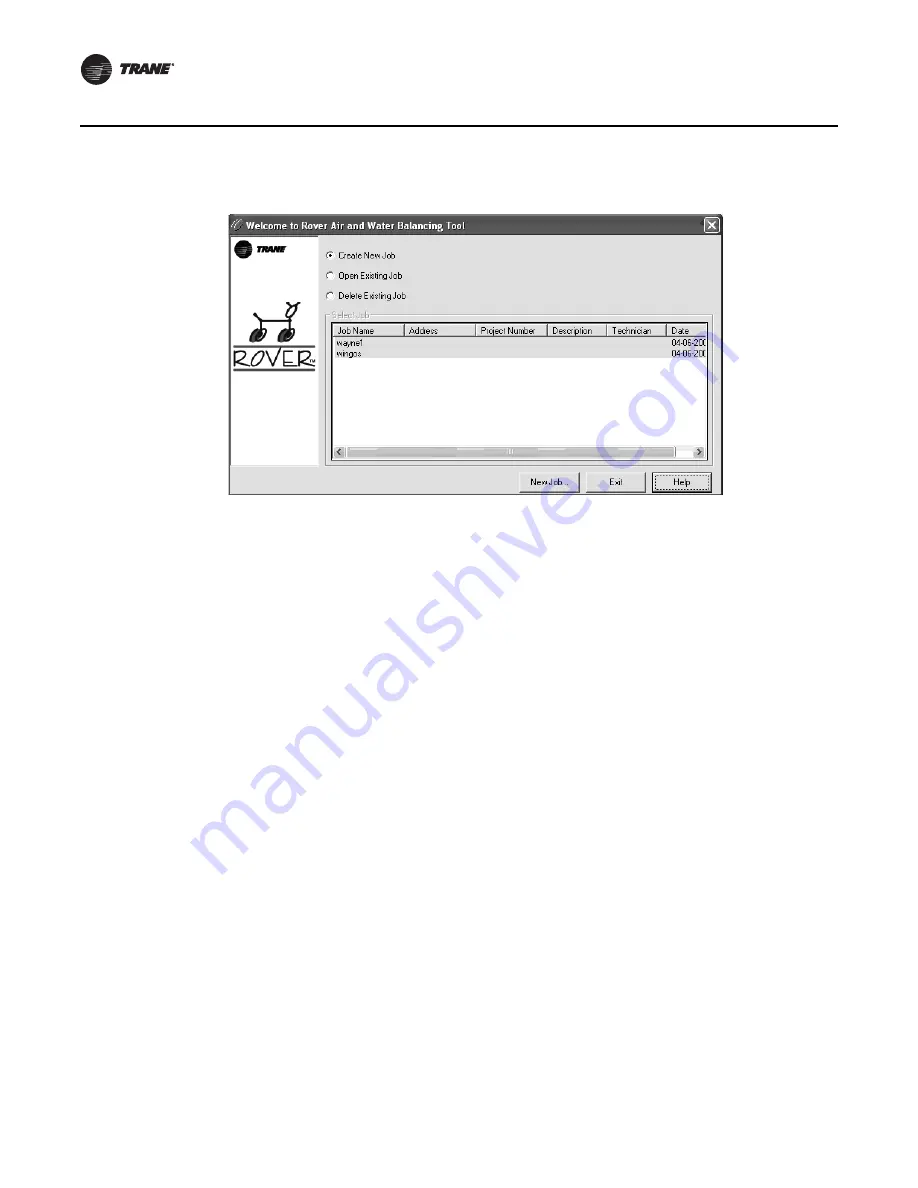
80
VAV-SVP01A-EN
Air and Water Balancing
Create New Job
Click this option, then click the Create New Job button to create a new job.
Open Existing Job
Click this option, select a job from the list, then click the Open Job button to open an existing job.
Delete Existing Job
Click this option, select a job from the list, then click the Delete Job button to delete a job.
Select Job to Open
Shows a list of existing jobs. Use this list to select an existing job to open or delete.
Create New Job / Open Job / Delete Job button
This button changes depending on the option you select at the top of the screen. After selecting
an option, click this button to perform the task.
Exit button
Click Exit to close the Air and Water Balancing tool.
Figure 51. Balancing tool screen
Summary of Contents for VAV VV550 LonTalk
Page 1: ...May 2010 VAV SVP01A EN Installation Operation Programming VAV VV550 LonTalk Controller...
Page 17: ...VAV SVP01A EN 17 VAV Start Up Check Out Procedure Figure 2 VV550 single duct control diagram...
Page 18: ...18 VAV SVP01A EN VAV Start Up Check Out Procedure Figure 3 VV550 fan powered control diagram...
Page 107: ...VAV SVP01A EN 107 Troubleshooting Figure 59 VV550 single duct control diagram...
Page 108: ...108 VAV SVP01A EN Troubleshooting Figure 60 VV550 fan powered control diagram...
Page 110: ...110 VAV SVP01A EN Troubleshooting Figure 62 Single duct with three phase voltage electric heat...
Page 115: ......