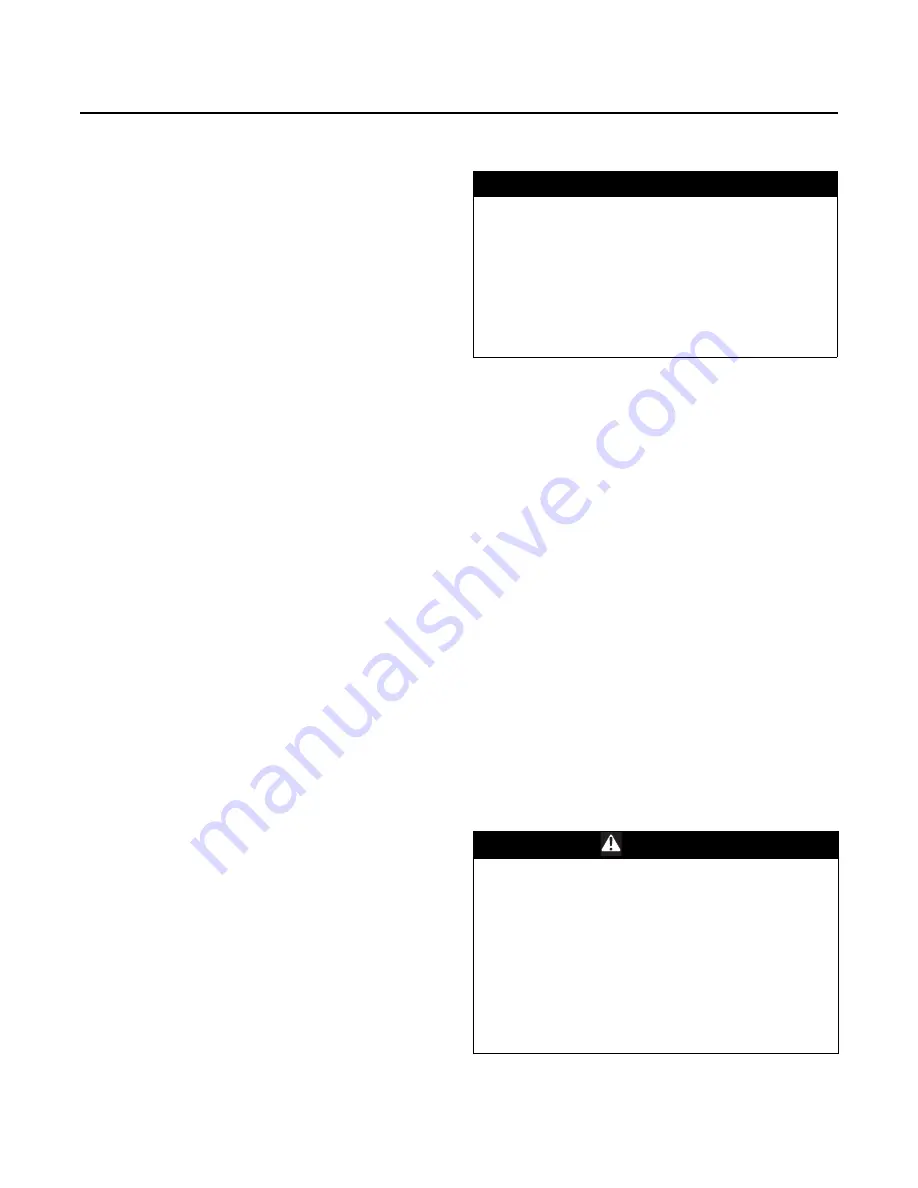
Maintenance
48
RT-SVX46G-EN
•
Record this data on an “operator’s maintenance log”
like the one shown in
. If the operating
pressures indicate a refrigerant shortage, measure the
system superheat. For guidelines, refer to the
“Compressor Startup” section.
Important:
Do not release refrigerant to the
atmosphere! If adding or removing
refrigerant is required, the service
technician must comply with all federal,
state and local laws.
Heating Season
•
Inspect the unit’s air filters. If necessary, clean or
replace them.
•
Check supply fan motor bearings; repair or replace the
motor as necessary.
•
Inspect both the main unit control panel and heat
section control box for loose electrical components
and terminal connections, as well as damaged wire
insulation. Make any necessary repairs.
•
Clean burner area, verify gas heat system operates
properly.
Coil Cleaning
Regular coil maintenance, including annual cleaning,
enhances the unit’s operating efficiency by minimizing:
compressor head pressure and amperage draw,
evaporator water carryover, fan brake horsepower due to
increase static pressure losses, airflow reduction.
At least once each year, or more often if the unit is located
in a “dirty” environment, clean the evaporator and
condenser coils using the instructions outlined below. Be
sure to follow these instructions as closely as possible to
avoid damaging the coils.
Note:
For units equipped with hail guards follow removal
procedure listed below.
Hail Guard Removal
•
Unlatch hail guard.
•
Pull the top of the hail guard outward until the fastener
studs are free of the retaining nuts.
•
Lift the hail guard from the lower retaining bracket and
set aside.
Microchannel (MCHE) Coils
Due to the soft material and thin walls of the MCHE coils,
the traditional field maintenance method recommended
for Round Tube Plate Fin (RTPF) coils does not apply to
microchannel coils.
Moreover, chemical cleaners are a risk factor to MCHE due
to the material of the coil. The manufacturer does not
recommend the use of chemical cleaners to clean
microchannel coils. Using chemical cleaners could lead to
warranty claims being further evaluated for validity and
failure analysis.
The recommended cleaning method for microchannel
condenser coils is pressurized water or air with a non-
pinpoint nozzle and an ECU of at least 180 with pressure no
greater than 600 psi. To minimize the risk of coil damage,
approach the cleaning of the coil with the pressure washer
aimed perpendicular to the face of the coil during cleaning.
Note:
For more details on Microchannel coil cleaning,
please refer to bulletin RT-SVB83*-EN.
Round Tube Plate Fin (RTPF) Coils
To clean refrigerant coils, use a soft brush and a sprayer
(either a garden pump-up type or a high-pressure
sprayer). A high-quality detergent is also required;
suggested brands include “SPREX A.C.”, “OAKITE 161”,
“OAKITE 166” and “COILOX”. If the detergent selected is
strongly alkaline (ph value exceeds 8.5), add an inhibitor.
1. Remove enough panels from the unit to gain access to
the coil.
NOTICE
Coil Damage!
Failure to follow instructions below could result in coil
damage.
DO NOT use any detergents with microchannel
condenser coils. Use pressurized water or air ONLY,
with pressure no greater than 600 psi.
For additional information regarding the proper
microchannel coil cleaning procedure, refer to service
bulletin RT-SVB83*-EN.
WARNING
Hazardous Chemicals!
Failure to follow all safety instructions below could
result in death or serious injury. Coil cleaning agents
can be either acidic or highly alkaline and can burn
severely if contact with skin occurs. Handle chemical
carefully and avoid contact with skin. ALWAYS wear
Personal Protective Equipment (PPE) including goggles
or face shield, chemical resistant gloves, boots, apron
or suit as required. For personal safety refer to the
cleaning agent manufacturer’s Materials Safety Data
Sheet and follow all recommended safe handling
practices.