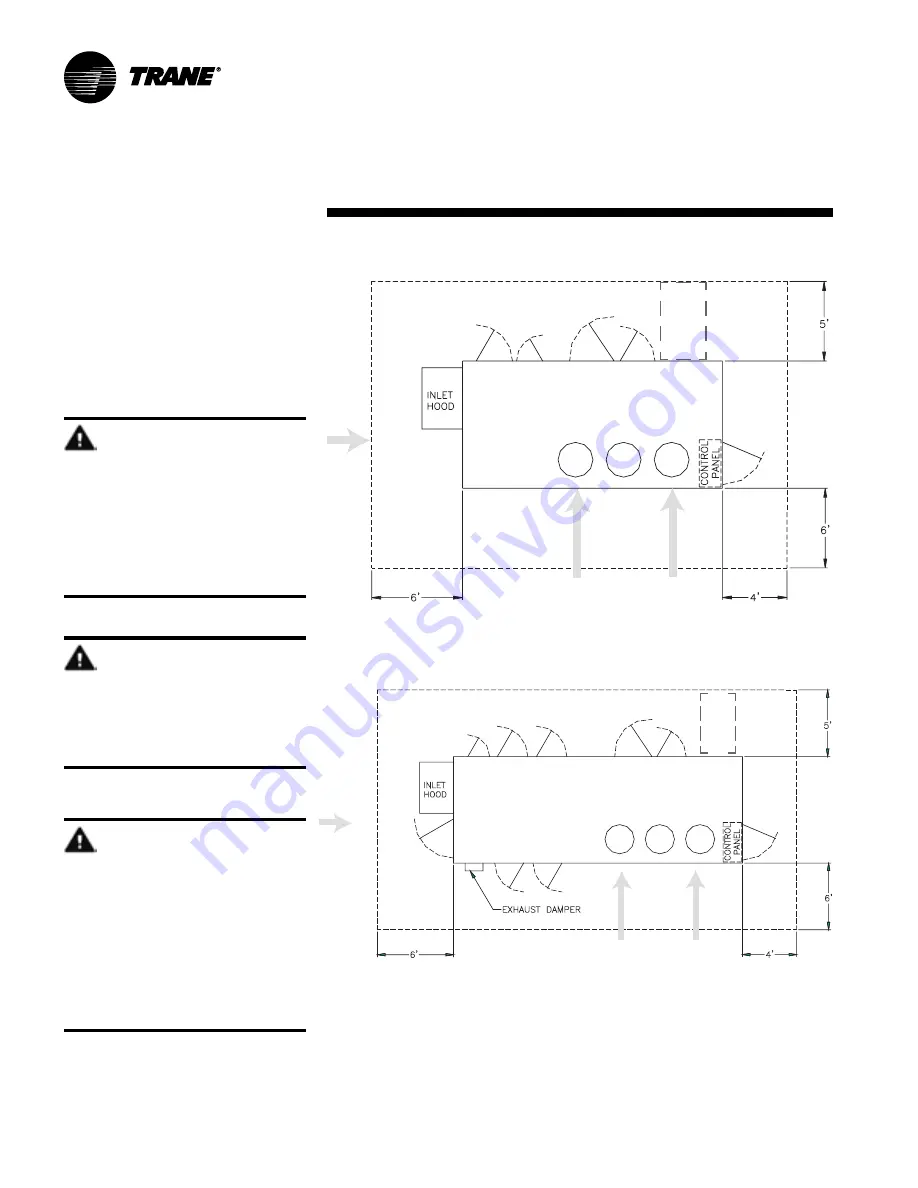
10
FAXA-SVX01B-EN
Installation
pre-installation
considerations
Service Access
Maintain adequate clearances around
and above the fresh air unit to ensure
proper unit operation and allow sufficient
service access. See Figure I-PC-1 for
recommended clearances. If installing the
unit higher than the typical curb elevation,
field-construct a catwalk around it to
provide safe, easy maintenance access.
WARNING!
Hazardous voltage!
Disconnect electrical power source
and remote disconnects before
servicing unit. Follow proper lockout/
tagout procedures to ensure power
cannot be inadvertently energized.
Failure to do so may cause death or
injury.
Figure I-PC-1. Top view of fresh air unit showing recommended service and code clearances.
service access
for removal of
gas or electric
heaters
unit without TE wheel
condenser airflow and
compressor maintenance
air path into unit
WARNING!
Disconnect gas supply!
Before servicing unit, FIRST turn off
the gas supply. Failure to turn off the
gas supply can cause death or serious
injury.
WARNING!
Combustible materials!
Maintain proper clearance between
the unit heat exchanger, vent
surfaces, and combustible materials.
Refer to this manual for proper
clearances. Improper clearances can
cause a fire hazard. Failure to
maintain proper clearances can cause
death, serious injury, or property
damage.
unit with TE wheel
condenser airflow
air path into
service
access for
removal of
Summary of Contents for FADA
Page 83: ......