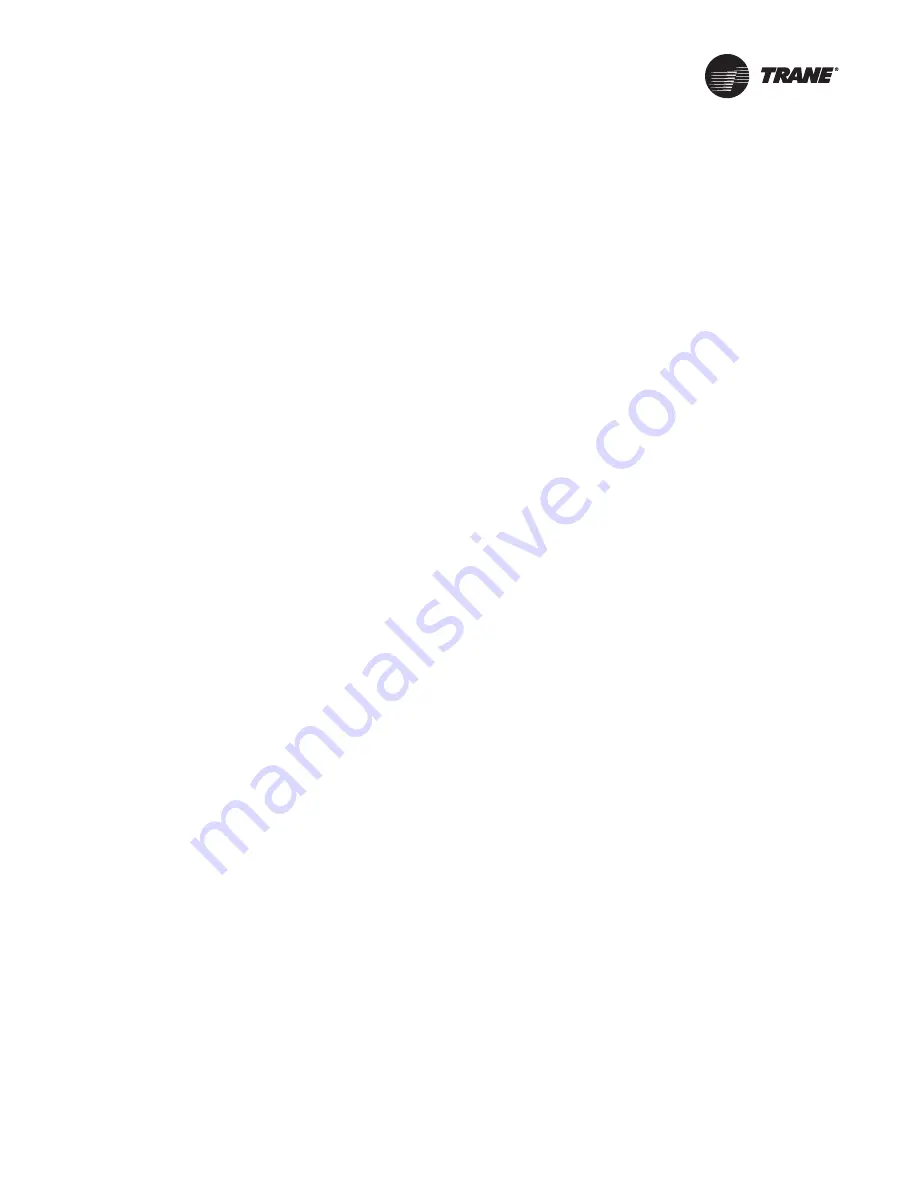
CLCH-SVX03C-EN
49
Coil Piping and Connections
General Coil Piping Recommendations
Proper installation, piping, and trapping is necessary to ensure satisfactory coil operation and to
prevent operational damage:
•
Support all piping independently of the coils.
•
Provide swing joints or flexible fittings on all connections that are adjacent to heating coils to
absorb thermal expansion and contraction strains.
•
If the coil was ordered with factory-mounted controls, install the control valves. The valves ship
separately.
Note:
The contractor is responsible for supplying the installation hardware.
•
For best results, use a short pipe nipple on the coil headers prior to making any welded flange
or welded elbow type connections.
•
Extended drain and vent connections are provided as standard on DD and D coils only. If
extended drains and vents are required on other water coils, they must be field-installed or
ordered as specials from the factory.
•
Pipe coils counter-flow to airflow.
NOTICE
Connection Leaks!
Use a backup wrench when attaching piping to coils with copper headers to prevent damage to
the coil header. Do not use brass connectors because they distort easily and could cause
connection leaks.
NOTICE
Over Tightening!
Do not use Teflon-based products for any field connections because their high lubricity may
allow connections to be over-tightened, resulting in damage to the coil header.
NOTICE
Leakage!
Properly seal all penetrations in unit casing. Failure to seal penetrations from inner panel to
outer panel may result in unconditioned air entering the unit, and water infiltrating the
insulation, resulting in equipment damage.
•
When attaching the piping to the coil header, make the connection only tight enough to prevent
leaks. Maximum recommended torque is 200 foot-pounds.
•
Use pipe sealer on all thread connections.
•
After completing the piping connections, seal around pipe from inner panel to outer panel.