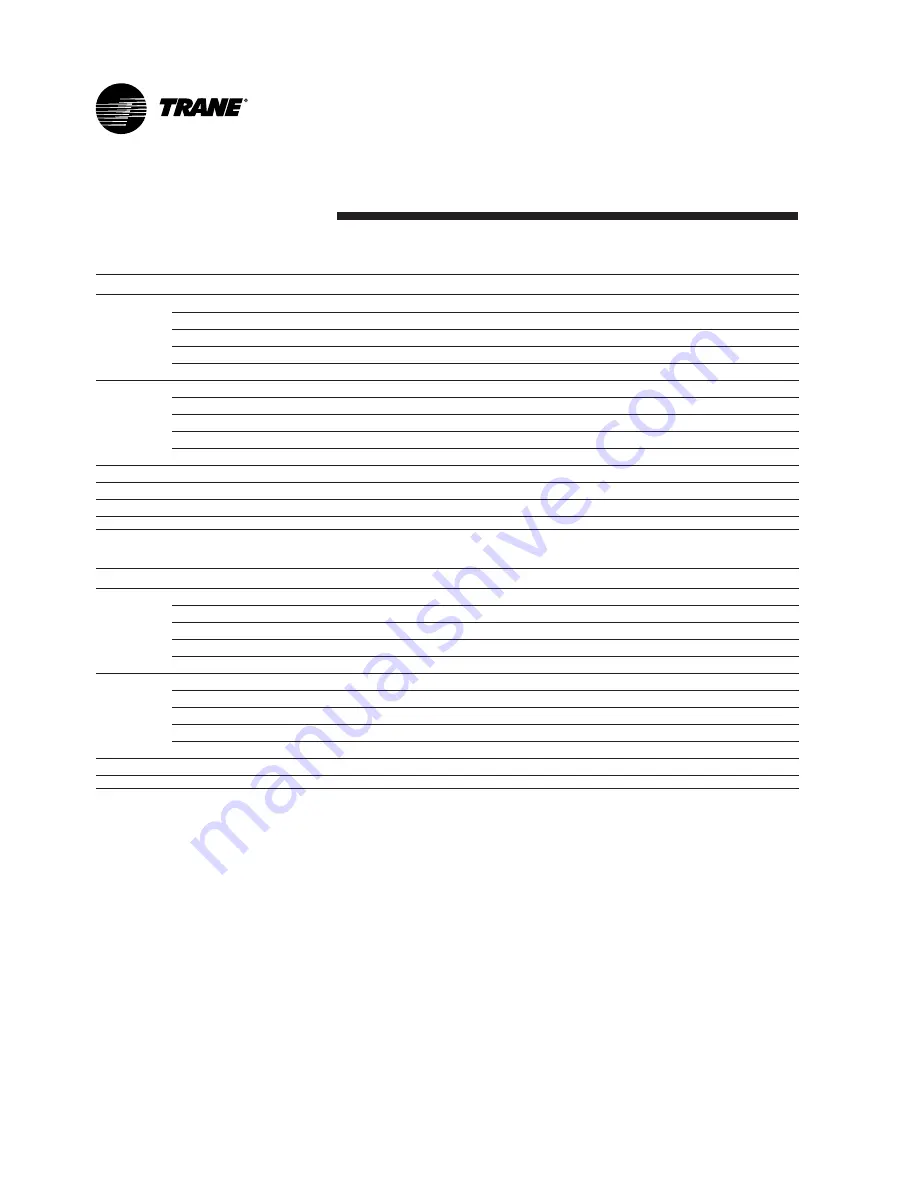
General Data
CG-SVX06D-E4
12
Table 7 - Evaporator hydraulic module
205
206
207
208
209
210
211
212
213
214
215
High head pressure option
Nb Pump set
1
Motor (1)(2)
(kW)
4.0
4.0
5.5
5.5
5.5
7.5
7.5
11.0
11.0
11.0
11.0
Rated Amps (1)(2)
(A)
7.5
7.5
11.1
11.1
11.1
14.7
14.7
20.0
20.0
20.0
20.0
Motor RPM
(rpm)
2900
Low head pressure option
Nb Pump set
1
Motor (1)(2)
(kW)
2.2
2.2
4.0
4.0
4.0
5.5
5.5
4.0
4.0
5.5
5.5
Rated Amps (1)(2)
(A)
4.0
4.0
7.5
7.5
7.5
11.1
11.1
7.8
7.8
10.3
10.3
Motor RPM
(rpm)
2900
Expansion tank volume
(l)
25
25
25
25
25
25
25
35
35
35
35
User volume expansion capacity (3)
(l)
3600
3600
3600
3600
3600
3600
3600
5100
5100
5100
5100
Water strainer diameter
3"
3"
4"
4"
4"
4"
4"
4"
4"
4"
4"
Piping
Steel
Table 8 - Condenser hydraulic module
205
206
207
208
209
210
211
212
213
214
215
High head pressure option
Nb Pump set
2 (in parallel)
Motor (1)(2)
(kW)
3
3
4
4
4
4
4
7.5
7.5
7.5
7.5
Rated Amps (1)(2)
(A)
6.1
6.1
7.7
7.7
7.7
7.7
7.7
13.8
13.8
13.8
13.8
Motor RPM
(rpm)
2900
Low head pressure option
Nb Pump set
2 (in parallel)
Motor (1)(2)
(kW)
2.2
2.2
3.0
3.0
3.0
3.0
3.0
4.0
4.0
5.5
5.5
Rated Amps (1)(2)
(A)
4.2
4.2
6.1
6.1
6.1
6.1
6.1
7.8
7.8
10.3
10.3
Motor RPM
(rpm)
2900
Water strainer Diameter
4"
4"
4"
4"
4"
4"
4"
4"
4"
4"
4"
Piping
Steel
(1) Per motor
(2) Dual Pump Option
(3) Hydrostatic pressure 3 bar at 25°C with 7°C mini